|
Post by Johansson on Nov 5, 2012 14:26:50 GMT -5
They are redesigning the front end to get a rounder shape to the transition cone between the round tailpipe and square valve plate, the design they have now has flat sides which tend to develope cracks after a while. They also released a movie from their years of pulsejet racing so far, they even chose english for the texting which should suit you guys better than swedish. 
|
|
|
Post by stoffe64 on Nov 5, 2012 16:41:15 GMT -5
wow  , fantastic machine, i want to see that thing live!
|
|
|
Post by Johansson on Nov 11, 2012 11:59:33 GMT -5
Then get your ass up to Orsa in the middle of february! 
|
|
|
Post by Johansson on Nov 13, 2012 16:11:27 GMT -5
While I was working on Olovs lathe with the power turbine housing yesterday Olov built a test stand for the rocket engine trolley, the trolley must be able to move forward freely if the load cell is to work correctly but in all other directions it must be held tight(ish) so it won´t tip over. 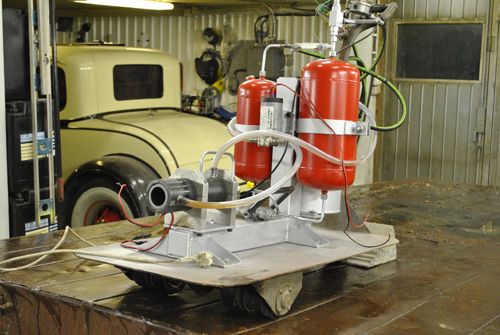 A master craftsman at work!  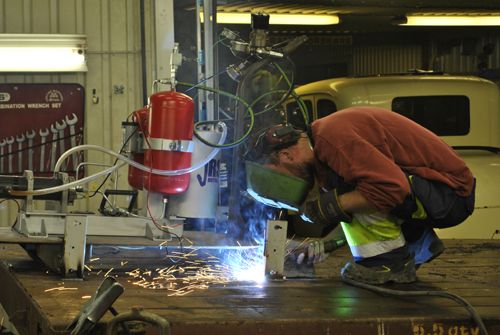 Olov testing the string controlled on/off valve after getting tangled up... 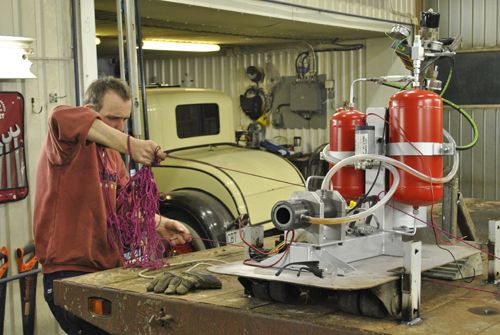 Finally a small note that some might find useful, I have had severe problems finding correct data of liquid nitrous oxide density at different temps. The number I found at a well respected rocketeering homepage turned out to be at boiling temps, i.e. -88.5°C where it has a density of 1.223kg/dm3. Since I have no plans of running the engine when it is -88.5°C outside that number is completely useless and might have fooled me into designing the fuel flow of the engine incorrectly... =( Anyway, this is how the density changes with temperature:  Judging from this the engine might run a little rich on methanol since there will be less N2O flow at the temps I will race in (-15°C to 0°C) but that hardly matters since this year it is more show than go. Test run is planned this sunday so we will know soon. If the engine survives the Speed Weekend race and performs according to expectations we might just build a streamlined vehicle for next year with larger tanks that will take us the whole 2000m track, with 100-120kg of thrust and a drop tank style vehicle it will go really fast by the time we cross the finish line!  Cheers! /Anders
|
|
|
Post by Johansson on Nov 18, 2012 0:18:00 GMT -5
T - 6 hours now, three hours from now we will start assembling the thrust stand and finish the last bits and pieces. Wish us luck!  Cheers! /Anders
|
|
|
Post by pitciblackscotland on Nov 18, 2012 2:44:51 GMT -5
Hi Anders, Love the work you are doing on this rocket engine. Good luck with the test fire of the engine  Cheers, Mark..
|
|
Deleted
Joined: January 1970
Posts: 0
|
Post by Deleted on Nov 18, 2012 3:04:10 GMT -5
hope all gose well today
|
|
|
Post by Johansson on Nov 18, 2012 14:27:54 GMT -5
Hi guys! A very quick reply now, my oldest girl is sick with feber and a nasty cough so I haven´t got time to dig through the 15GB video material we have from today. 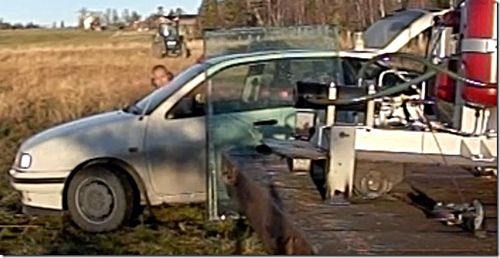 Anyway, it ran ok for the first ever run although with a pretty bad high frequency instability. No thrust reading and the camera that was supposed to record the gauges ran out of memory just before the engine started. The methanol was mixed with 25% water in the first run, the second run it had even more water which made it very difficult to ignite. Tank pressure in the first run was 60 bar and for the second run we increased the pressure even higher to try to cure the instability but since we had problems filling the NOX tank, ignition was difficult and time was running away we didn´t manage to get another run out of it. I´ll get back to you with a longer report later and a (hopefully) well made video. If you have any ideas about the instability or anything else please tell me.  Cheers! /Anders
|
|
|
Post by racket on Nov 18, 2012 15:42:49 GMT -5
Hi Anders
That second run lasted a long time ..................it seemed to me that it lasted too long for the amount of fuel you had and the pressures pushing it into the combustion chamber .
It looked like you had "surge" ( only way to describe it) with a very regularly timed flame pulsing back and forth .
Do you have any one way ( check valves) valves in the lines ??
Its as though the combustion chamber pressure rise is forcing the fuel back to the tank , this then reduces flow and the chamber pressure drops allowing fuel back into the chamber with another sudden pressure rise and the process keeps repeating itself ( surge like) .
You may need smaller diameter fuel/oxidiser lines to reduce the potential flow capacity making it harder to reverse flow and/or check valves .
Just some thoughts from someone who hasn't the faintest idea what they're talking about :-)
Cheers John
|
|
|
Post by Johansson on Nov 18, 2012 16:13:39 GMT -5
Hi John, Good input on the "surge" issue, I have a check valve on the top of the oxidiser tank to keep the NOX from flowing into the methanol tank, no restrictions at all on the liquid side of the tanks. Both videos are from the same run by the way. It just feels much longer at 600fps.  Cheers! /Anders
|
|
stevep
Veteran Member
 
Joined: November 2012
Posts: 120
|
Post by stevep on Nov 18, 2012 18:55:30 GMT -5
Hi Anders, I'm new here (see my intro elsewhere) and I've been following your progress in "lurk"mode. Your work is very impressive, and you've made good progress. Regarding your test run, I think you've made a "screamer"--this is a term that the hybrid rocket folks use when the combustion is uneven enough to create large amounts of acoustic noise and it is considered quite *dangerous*! It is the result of too little pressure drop across the injector. The danger, as rackert suggests, is that hot gasses can flow back into not only the fuel line (the least of your problems) but the *nitrous* line and you do not want that! Reading through your thread, I see no mention of any of the papers at Aspire Space: www.aspirespace.org.ukThere are some very useful papers there --anyone messing with nitrous in rocket motors should read, understand, and heed the relevant ones. I shall just quote a small section from one of them ("Nitrous Safety"): "A common trend is to use too large a hole/holes for the injector, in order to minimize the pressure-drop across it, but this is very dangerous practice. The pressure drop is there partly to prevent very hot combustion chamber gasses having the potential to flow back upstream into the feed system or tank if there is a chamber pressure pulse. Too low a pressure drop across the injector encourages such audible forward-reverse flow oscillations in the chamber. Screaming hybrids are not cool, they're dangerous: hot gasses could get back into the feed system and decompose the nitrous there, blowing up the feed pipework and starting a fire. Use a smaller orifice size to get the chamber oscillations under control." The author goes on to relate a couple of incidents where this happened. The recommended pressure drop is 20% of the combustion chamber pressure (I know you've seen/mentioned this number before). You now have concrete evidence that your orifices are too large. I know you don't like the thought of drilling smaller holes--last sizes I saw you mention were (2) 1.5mm holes for nitrous. That's pretty large for a small motor--I regularly drill .021" (.5mm) holes for my circuit boards and am able to do the same in aluminum to a depth of .25" (5 mm) so I'm sure you can go smaller than 1.5mm. Smaller holes will also give you much smaller drop sizes which will lead to greater efficiency (I know you said you don't care about efficiency for this motor, but still....) The paper I quoted gives some formulas that may help to determine the right size. Also, I would put more distance between yourself and your test stand--when it comes to explosions, distance is your friend. I know you've got a screen between you and the test stand, but it will not protect you from objects falling *down*. And some will (ask me how I know). I hope I don't sound harsh or overly alarmist--I've been around rockets big enough to kill people for a while now, and I just want your kids to have a father after you're done with this. I'm happy to help in any way I can, either with calculations or knowledge--but most of all I want you to be *safe*. --Steve
|
|
|
Post by racket on Nov 18, 2012 23:54:40 GMT -5
Hi Anders
Duh , ..............same run eh :-(
Thats changes things a bit , but not the pulsing combustion .
When I first made the FM-1 engine I had both the start gas and the main fuel going to a common "fuel" manifold , it gave nothing but problems until I had separate systems , I get the feeling your two "fluids are "influencing??" each other some way ...............LOL, just a gut feeling :-)
Cheers John
|
|
|
Post by racket on Nov 20, 2012 3:32:15 GMT -5
Hi Anders
Just been reading my Zucrow text and he talks about low frequency combustion pressure oscillations , at between 60 and 300 cycles per second , and are longitudinal .
Required fuel pressure drop across the injector orifice of both fuel and oxidiser is between 60 and 150 psi in combustors working between 300 and 850 psi . ..................some of the theoretical calculations even go as far as having the pressure drop as high as 50% of the combustor pressure to prevent "oscillations" .
....................as Steve suggests , smaller holes required :-)
Cheers John
|
|
|
Post by Johansson on Nov 20, 2012 14:44:20 GMT -5
Hi Steve and John! Thank you Steve for the insight and wise words of caution, I will, among other things, change to 2x1mm NOX holes and a methanol injector with exchangable metering jets so I can field tune the mixture instead of having to make a completely new stainless injector every time. I will also try to arrange a safer way of operating the engine, preferably while sitting inside the car to avoid falling pieces of metal in case I blow up a fuel tank. Longer throttle ropes are also needed, perhaps I could use a pneumatic piston and compressed air to operate the engine from out of sight. As you can see we had a lot of fun, we fired off a couple of flash powder bombs as well but that didn´t make it to the video. ;D 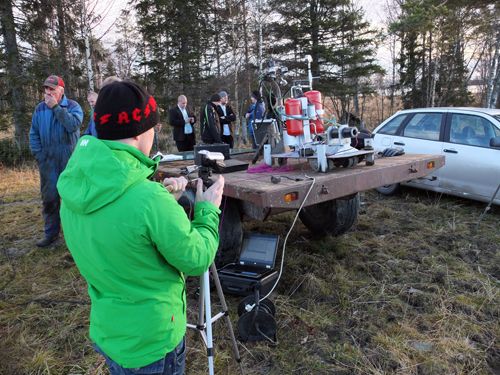 Afterwards I heard that several of my friends (and to be honest myself as well) never really believed the engine would even light, we have had our share of first-time problems so I wasn´t expecting much more than a couple of bangs and some fire. If the engine survived the day I would have been satisfied.   During the second attempt I used a mixture of 65% methanol and 35% water, that might be the reason why the engine didn´t light properly. It was a mistake, some of the assumed pure methanol was already mixed with 25% water so I got a weaker blend than I wanted.  I also had some difficulties filling the NOX run tank from the storage tank, I will talk with some guys who use NOX regularly in race cars and see what they can tell me about it. Hopefully I will have everything set for another test run some time in january. Cheers! /Anders
|
|
8maddog8
Member

Joined: July 2012
Posts: 24
|
Post by 8maddog8 on Nov 20, 2012 19:08:10 GMT -5
Nice work! Looks like a real good learning exercise. Really love the last photo of everyone hiding behind the car 
|
|