|
Post by Johansson on May 19, 2014 22:56:25 GMT -5
Freepower section almost together now. 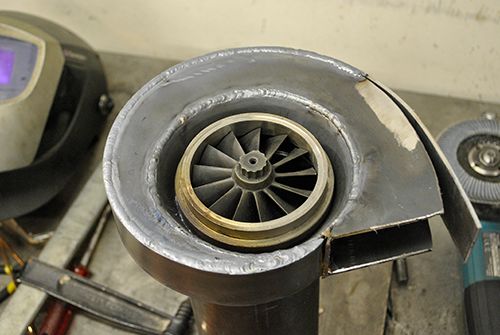 All I need to do is to roll some transition pieces where the holes in the scroll are, then it is time to make the mounting plate that the engine will be bolted to and start making the rear sprocket shaft that connects to the propeller rig. 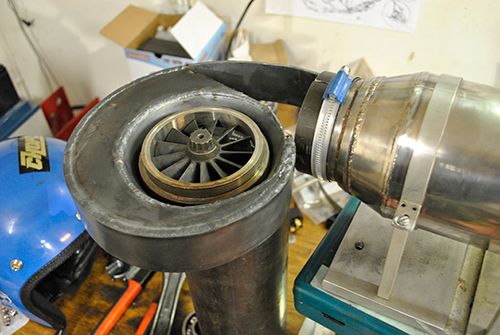 Cheers! /Anders
|
|
|
Post by racket on May 20, 2014 4:07:44 GMT -5
Looking good Anders :-)
|
|
|
Post by Johansson on May 21, 2014 15:01:22 GMT -5
Thanks John!  Last night I worked on the stuff we will bring to the big motor show this weekend, and made the pieces that would make the transition between the jet engine outlet and the snail housing. 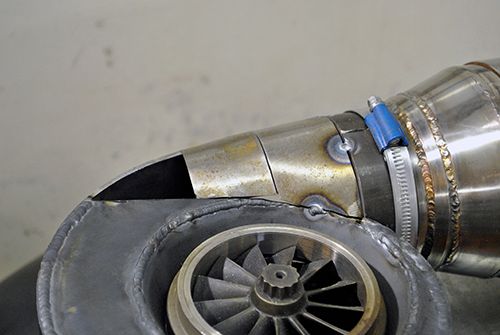 The puzzle is completed and is ready to be welded!  After the housing had cooled down a bit I assembled the package and test fitted it to the boat engine rig. 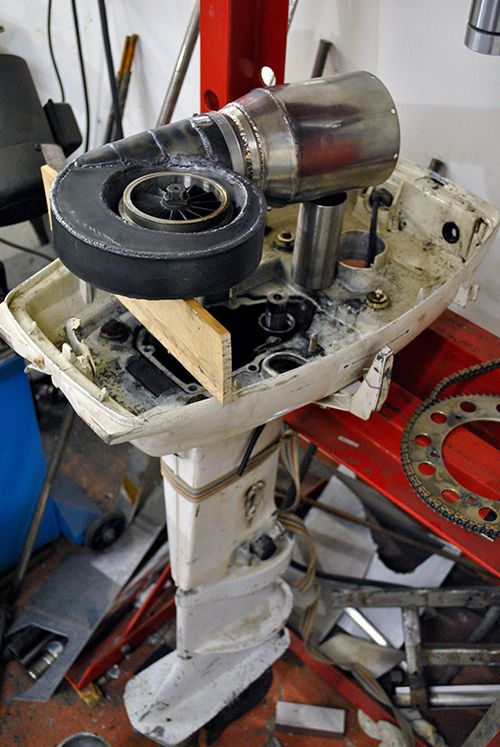 I should be able to fit the engine pretty nicely, whether or not the glass fiber cowling will catch fire is up for debate...  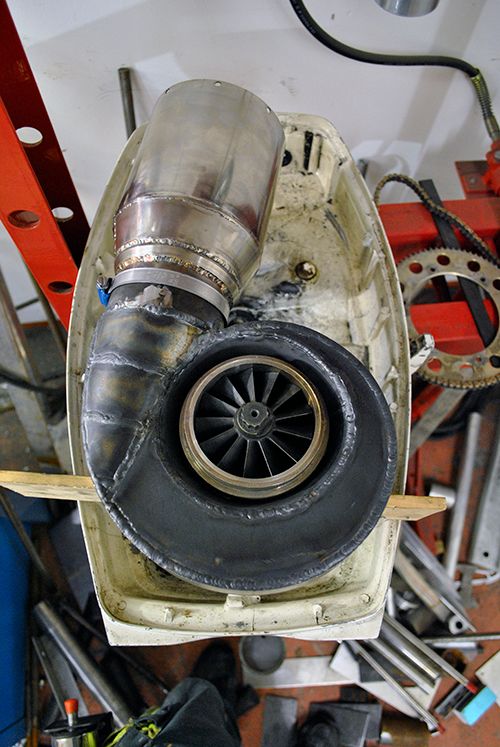 By now it was midnight so the last thing I did was to cut out a 5mm thick aluminum plate on which I will mount the engine. 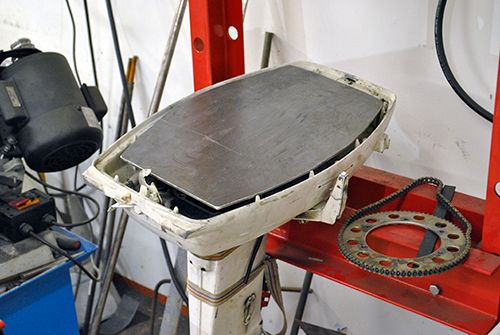 Cheers! /Anders
|
|
|
Post by racket on May 21, 2014 18:18:15 GMT -5
Hi Anders
I can see this working already.
Heh heh , what A/R are you using on the scroll ;-)
Cheers John
|
|
wolfdragon
Senior Member
 
Joined: April 2011
Posts: 287
|
Post by wolfdragon on May 21, 2014 20:11:41 GMT -5
I think I speak for everyone: "FUCK THE FIBERGLASS! The flames will just make it look that much more awesome!"
|
|
|
Post by Johansson on May 22, 2014 0:44:35 GMT -5
Hi Anders Heh heh , what A/R are you using on the scroll ;-) Cheers John A little bit of this and a little bit of that...  I have to admit that I didn´t give it much thought, I just tried to keep the turbine inducer as the smallest area.
|
|
|
Post by racket on May 22, 2014 1:59:01 GMT -5
Hi Anders
LOL..........the "little bit of that" sounds about right :-)
The cummins freepower wheel I used in my kart had a 3.5" exducer and I flowed ~1.1 lbs/sec , so your 3.2" exducer should be able to flow ~0.9 lbs/sec , you're well within the ballpark , even if the A/R is a little tight .
If your temps are a bit high , add a dump nozzle to bleed off a bit of the hot gases as they go into the scroll .
Cheers John
|
|
miuge
Veteran Member
 
Joined: March 2014
Posts: 199
|
Post by miuge on May 23, 2014 2:11:24 GMT -5
That's a really compact assembly! If we had a similar engine we could have built a lot smaller bike 
|
|
|
Post by Johansson on Sept 7, 2014 11:52:49 GMT -5
While waiting for the parts ordered for the turbine bike I have spent some time on the outboard project. My brother visited a couple of months ago and helped me both with drinking some beer and drilling some holes.  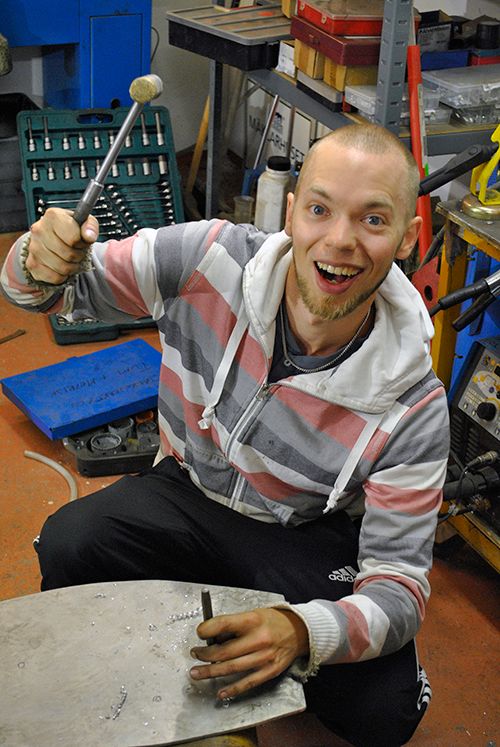 A couple of nights ago I fitted the base plate to the rig. 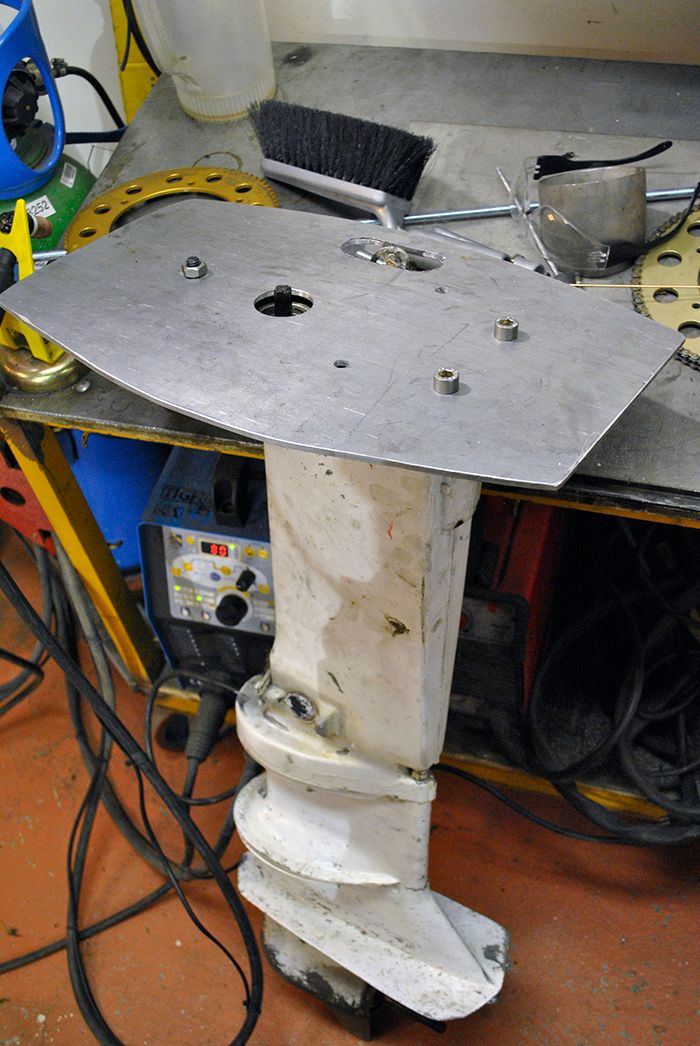 I cut the IC engine crankshaft to source the part with the splined hole that fits the driveshaft, that part was then modified and ended up having a bolt circle that the secondary chain sprocket will fit onto. 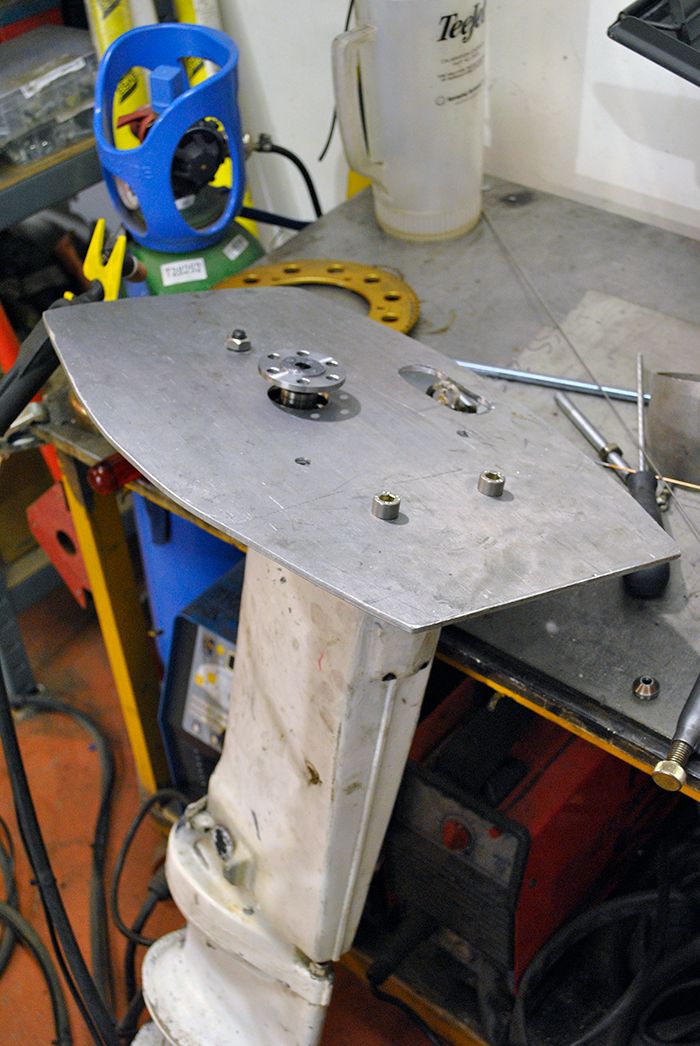 I had to support the driveshaft somehow, so a support bearing holder was made from nylon. 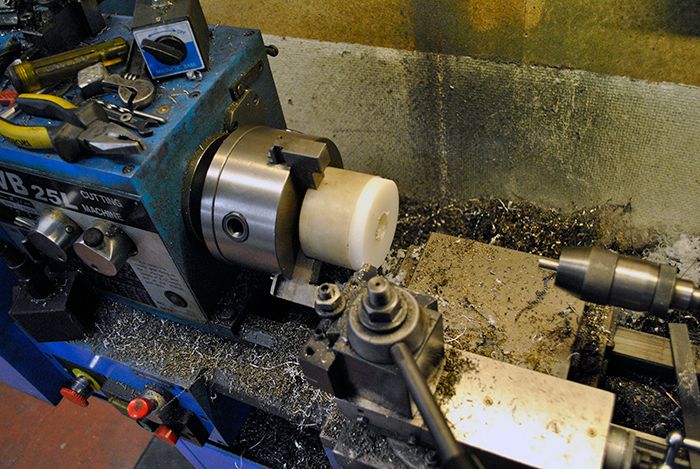 Here it is, bolted to the base plate. 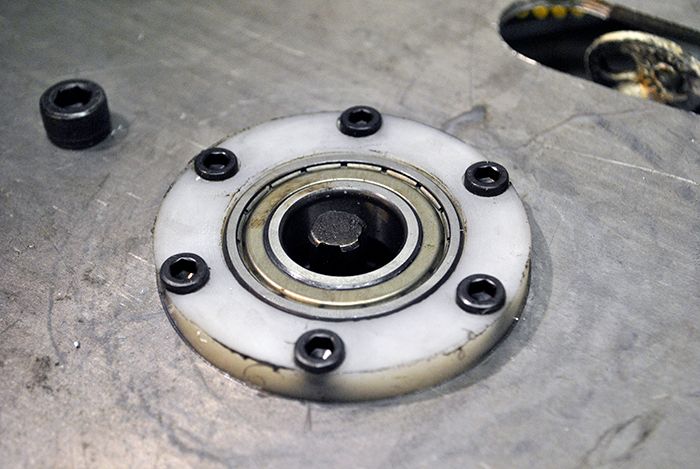 In order to fit the sprocket to the drive shaft I had to make a coupling plate from aluminum. 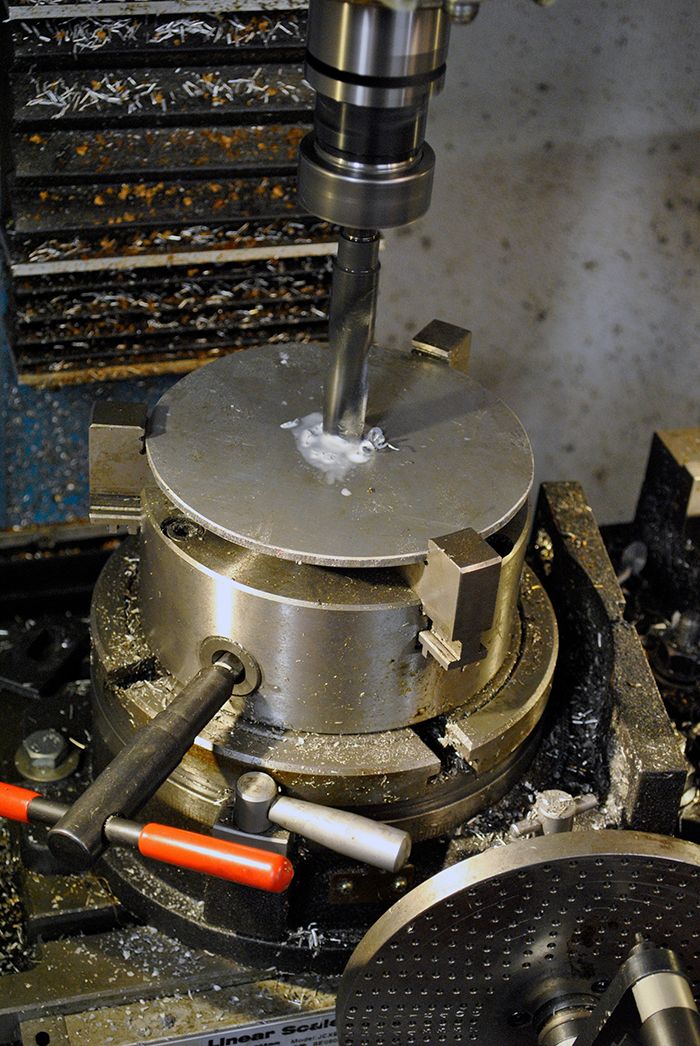 Just look how fancy it turned out! You can also see the new glow plug fitting that I made and welded to the engine cover. 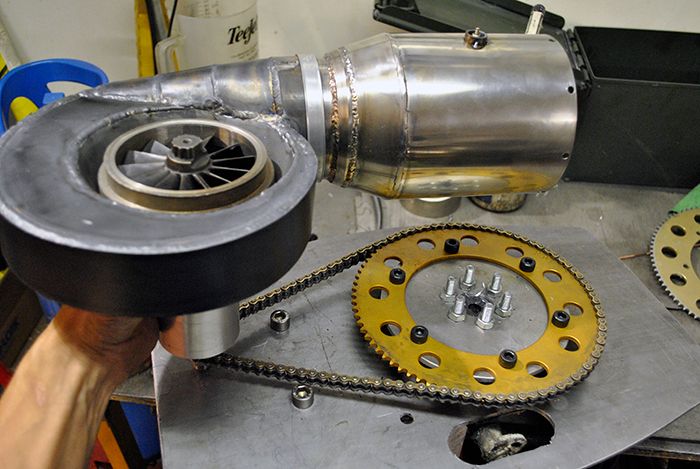 Since my hand would get tired pretty fast holding the engine in place while driving the boat I had to make some mounts for it, I cut a bunch of 3mm steel strips from a scrap sheet of steel at work and tacked an engine stand together the night after. 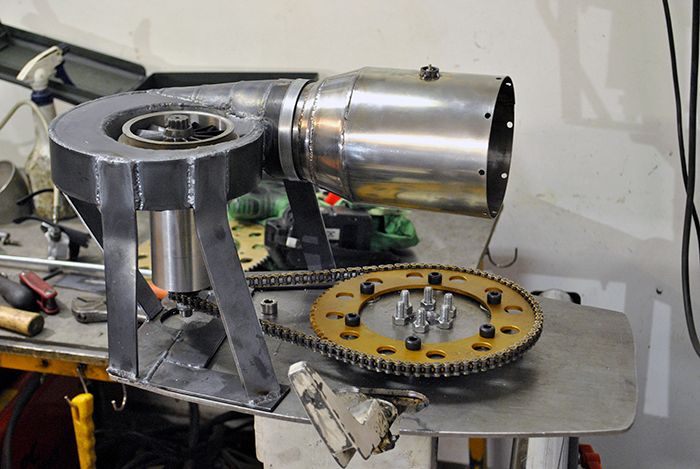 I will make a chain tensioner that I can move the stand back and forth before bolting it down against the base plate, the sprockets align well and I can make it perfect later by adding shims between the stand and base plate. 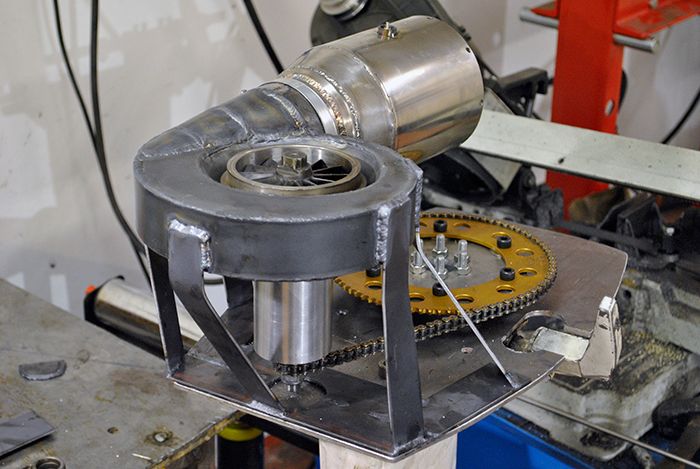 Cheers! /Anders
|
|
niffi
New Member
Joined: July 2014
Posts: 8
|
Post by niffi on Sept 7, 2014 12:32:08 GMT -5
Very, very nice! I guess you use Tig welding for the sheets?
|
|
|
Post by Johansson on Sept 7, 2014 13:16:31 GMT -5
Yup!
|
|
|
Post by smithy1 on Sept 7, 2014 14:41:54 GMT -5
Hi Anders,
I love your ingenuity...well done Sir....I did some repairs to two AMT Olympus engines a year or two back, they're nicely made turbines too..
Cheers, Smithy.
|
|
|
Post by Johansson on Sept 8, 2014 4:44:53 GMT -5
Hi Anders, I love your ingenuity...well done Sir....I did some repairs to two AMT Olympus engines a year or two back, they're nicely made turbines too.. Cheers, Smithy. Hi Smithy, They are very nicely built indeed, if I can make the freepower bearings survive I should have me a pretty reliable engine. I digged through my shelves last night and found a wind screen washer pump, perhaps I could run it through a PWM controller to circulate an oil/kero mix through the shaft tunnel and to a small water cooled tank? The revs won´t be extreme so I think the bearings should survive if I can keep the heat away from them. Cheers! /Anders
|
|
|
Post by smithy1 on Sept 8, 2014 14:32:29 GMT -5
Hi Anders, I have a miniature fuel pump if you need one for your free power lube requirements, the windscreen washer pump may not handle the fuel too well. What type of bearings are you using in the free power unit.. and what rpm do you think it will be running?
It may be possible to run the free-power lube pump from the engine pump PWM signal, just connect the two pumps in parallel..... when the engine is running the F/P lube pump will also be running, that will save having to run two PWM controllers. These little pumps only pull ~2-2.5amps so the engine controller should be able to handle both of them easily.
Cheers, Smithy.
|
|
|
Post by Johansson on Sept 8, 2014 15:13:02 GMT -5
Hi Anders, I have a miniature fuel pump if you need one for your free power lube requirements, the windscreen washer pump may not handle the fuel too well. What type of bearings are you using in the free power unit.. and what rpm do you think it will be running? It may be possible to run the free-power lube pump from the engine pump PWM signal, just connect the two pumps in parallel..... when the engine is running the F/P lube pump will also be running, that will save having to run two PWM controllers. These little pumps only pull ~2-2.5amps so the engine controller should be able to handle both of them easily. Cheers, Smithy. Hi Smithy, I´ll check the bearing size next time I take the shaft tunnel apart, but if I remember it correctly they are 12mm ID sealed precision bearings. I figure I can remove the inner seals to get the lube oil into the bearings and still keep the oil from flowing out of the shaft tunnel, we´ll see how it goes. If everything else fails I´ll buy a set of cheap ceramic bearings and cool them with lake water.  Frankly I have not a clue how much the propeller will rev, but with the gocart chain drive I don´t want to rev the freepower much more than 10.000rpm or so. Is the fuel pump signal from the FADEC a PWM signal? You are probably right about the windscreen washer pump not being up for the job, but since this is sort of a budget build I will at least try it out before opening up the wallet.  Cheers! /Anders
|
|