gidge348
Senior Member
 
Joined: September 2010
Posts: 426
|
Post by gidge348 on Sept 5, 2013 20:42:12 GMT -5
Hi Anders, do you think it is worthwhile lock wiring the banjo bolts as well? On the salt sometimes you can get a very high frequency vibration set up due to irregularities in the surface. Wont stop the bolt loosing torque but may buy you enough time to shut it down before an internal fire?
Ian...
|
|
|
Post by Johansson on Sept 6, 2013 0:23:30 GMT -5
Hi Anders Is it entirely the banjo fittings or oil bypassing the turbine seal and leaking down into the casing, as I've experienced oil in the casing ?? The 10/98 has a bit more drainage space , whereas you are using a scavenge pump, was it operating correctly , or could it be a slow drain back from a head of oil whilst standing for extended periods ?? Cheers John Hi John, I am not sure, perhaps I should feed the core some oil pressure once I´ve removed the combustor so I can see more clearly what is going on in there. After I drained the casing I tried again just to see so it wasn´t the fiber banjo seals that had dried out after the storage, after a couple of seconds the oil started to flow out of the drain so there is a leak for sure. Both scavenge pumps were working and I could hear when oil reached them so I don´t think they are to blame. Cheers! /Anders
|
|
|
Post by Johansson on Sept 6, 2013 0:33:41 GMT -5
Hi Anders, do you think it is worthwhile lock wiring the banjo bolts as well? On the salt sometimes you can get a very high frequency vibration set up due to irregularities in the surface. Wont stop the bolt loosing torque but may buy you enough time to shut it down before an internal fire? Ian... Hi Ian, The bolt heads are lock wired to each other, the pic was an old one during construction that I picked just to show what it looks like. Cheers! /Anders
|
|
|
Post by Johansson on Sept 6, 2013 6:15:02 GMT -5
I tore down the gas producer a couple of hours ago and found the banjo couplings without any sign of oil leaks, the compressor housing on the other hand was soaked in oil which I also found the reason for. 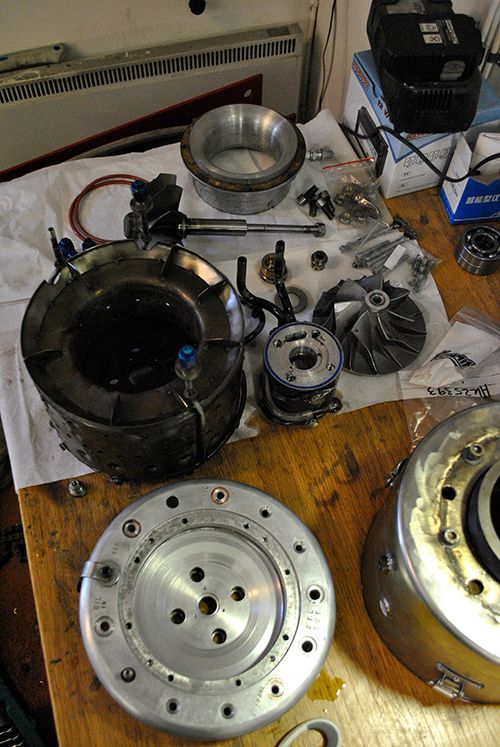 The time I ran the engine and the compressor nut came off and caused a rotor salad I didn´t notice that the piston ring seal on the spacer behind the compressor wheel got damaged, later I changed the seal but apparently I didn´t pay much notice to the aluminum sealing surface in the diffusor housing. 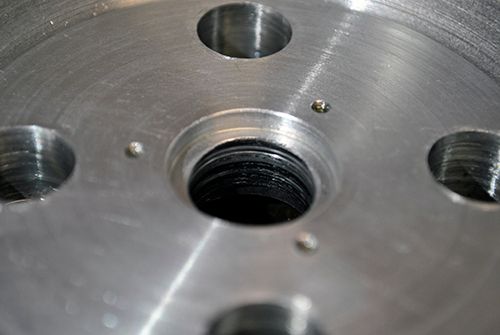 I need to remove the damaged section in the lathe and make a steel bushing that can be pressed in place and act as the piston sealing surface. I will still redesign the oil lines since they sooner or later will give me trouble again, so when I am finished with the engine everything in the construction I have come to regret during the bench testing will be redesigned and hopefully won´t give me trouble again. Cheers! /Anders
|
|
ripp
Veteran Member
 
I'm sorry, I don't speak english, so I torment you (and myself) with a translation program,Sorry
Joined: January 2013
Posts: 237
|
Post by ripp on Sept 7, 2013 3:53:01 GMT -5
|
|
|
Post by turbochris on Sept 7, 2013 12:27:35 GMT -5
Welcome rip, please go to the intro section and tell us more, you seem to know your shit! welcome to JATO!
I see high freq vibration/shaft whip damage in the compressors we use in the lasers. That shit will creep up on ya. been meaning to get into vibration analysis.
|
|
|
Post by ernie wrenn on Sept 8, 2013 20:43:46 GMT -5
Thanks RIP.. Excellent reading.
Welcome aboard...
|
|
|
Post by Johansson on Sept 9, 2013 5:03:50 GMT -5
Hi rip! Welcome to the forum and thanks for the input!
I have very little room for modifying the existing shaft tunnel, I will try to make an internal oil pressure line to the journal bearings with an O-ring gasket between the shaft tunnel and diffusor housing. Any larger mods than that and it would be easier to make a new shaft tunnel.
Cheers! /Anders
|
|
|
Post by turbochris on Sept 10, 2013 11:03:36 GMT -5
silicon o-ring
|
|
ripp
Veteran Member
 
I'm sorry, I don't speak english, so I torment you (and myself) with a translation program,Sorry
Joined: January 2013
Posts: 237
|
Post by ripp on Sept 10, 2013 13:37:39 GMT -5
|
|
|
Post by racket on Sept 11, 2013 4:19:21 GMT -5
Hi Rip LOL.......we want a bit of turbine glow ..............cool running turbines don't make much power ..............even the freepower turbine needs to have some "colour" www.youtube.com/watch?v=CplnY9TG7NECheers John
|
|
|
Post by Johansson on Sept 11, 2013 4:50:34 GMT -5
Hi Rip, Making a new shaft tunnel is probably the last thing I would do right now, after the oil line mods have been made it should work like it should so I see no reason for making a new one. I fixed some air leaks after the video with the glowing turbine was made, so now it runs cooler. And as John points out it is meant to glow.  Cheers! /Anders
|
|
gidge348
Senior Member
 
Joined: September 2010
Posts: 426
|
Post by gidge348 on Sept 11, 2013 8:20:40 GMT -5
|
|
ripp
Veteran Member
 
I'm sorry, I don't speak english, so I torment you (and myself) with a translation program,Sorry
Joined: January 2013
Posts: 237
|
Post by ripp on Sept 11, 2013 14:17:16 GMT -5
Hallo John, You are right. Under load, a Turbine can also glow. Anders Turbine run too hot because the nozzle was too small. I'm sorry, I have read too late the text
rip
google Translation
|
|
|
Post by Johansson on Sept 11, 2013 14:37:13 GMT -5
Last night I started modifying the shaft tunnel, first I cleaned off the remaining cheramic coating from the internal surfaces. As you might remember I coated them to lessen the heat soak from the glowing combustor but most of it came off during the first test run, most likely because of a lazy coater who didn´t prepare the surfaces enough...  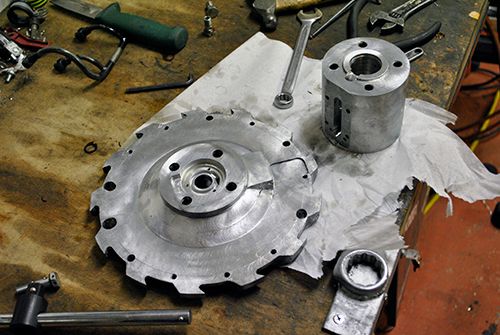 It took a while to figure out how to clamp down the shaft tunnel properly, I really didn´t want it to move during the milling since that would bring mayhem and destruction to my dear shaft tunnel. After making a journal bearing dummy I could fit it like this on the rotary table. 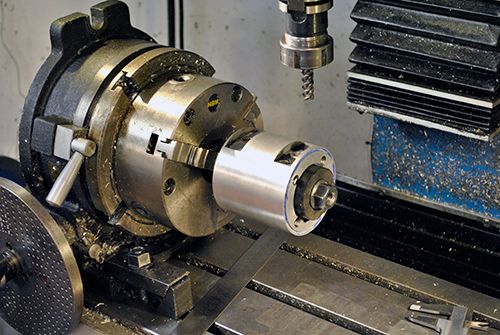 A couple of hours of milling, measuring, thinking and more milling I had come this far. A 30mm wide slot where an aluminum rod will fit, an internal oil channel will be drilled through one end of the rod and oil exit holes drilled that matches the existing holes in the shaft tunnel that feeds the journal bearings. Anyone who understood that?  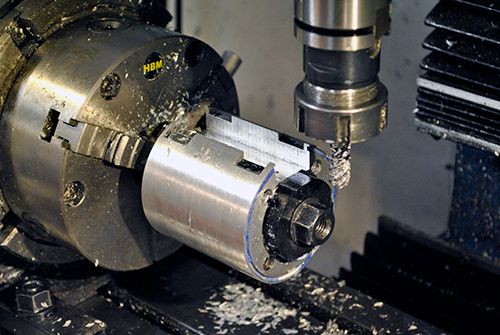 Test fitting the aluminum rod, I´ll make the O-ring grooves in this piece since I can´t afford to make a mistake with the shaft tunnel. 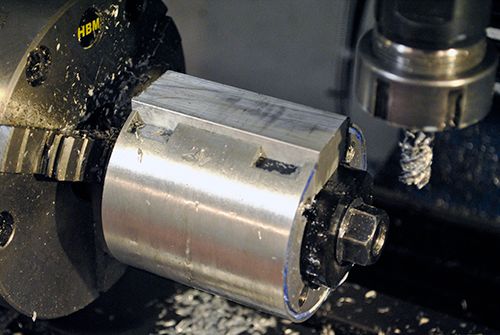 Cheers! /Anders
|
|