tegwin
Member

Joined: February 2012
Posts: 19
|
Post by tegwin on Mar 14, 2013 13:35:18 GMT -5
Again, thanks for the advice. For the price of a couple of bits of pipe and some gas from what you have said it will be well worth me fitting a propane ignition system  Can get on and start drawing up the parts and getting things made 
|
|
tegwin
Member

Joined: February 2012
Posts: 19
|
Post by tegwin on Mar 16, 2013 18:09:16 GMT -5
Busy day in the workshop today machining couplings and mounts to join my high pressure fuel pump to a large 12V motor.
I think I more or less have the pilot/main fuel and oil supply systems under control so this leaves the final "major" system... A starter...
I don't really want to go down the route of using a leaf-blower to start the engine and given the size of the turbo I don't think a 12v blower will be up to the job. So this leaves me with coupling a motor to the compressor via some sort of clutch.
How do most people start their engines?
I am estimating that I will need a motor capable of about 25-30K Rpm and around 600W. Does this seem reasonable? As for a clutch, the little wren turbines use a bendix type centrifugal clutch which should do the job. My only concern is the loading the motor will put on the spinning turbo. Am I likely to damage the bearing going down this route do you think?
This is the sort of thing I am envisaging.
|
|
|
Post by racket on Mar 16, 2013 19:21:10 GMT -5
Hi Tegwin
You'll probably find that the exhaust from a household vacuum cleaner will start your sized engine, if not, then a decent sized leafblower should , I used a leafblower on my TV84 with its 3.5" inducered comp .
The GT6041 turbokart in the video.....( have you read the Build Thread here on Site ??) required a huge 4hp leafblower prior to Smithy fitting the brushless motor , though that brushless is very big and expensive .
A lot will depend on how much rotary drag from the bearings you have during a spoolup , the GT6041 has a modern "balanced" thrust bearing with not a lot of drag , the thrust bearing Anders and I used with our TV94 rotors has a huge amount of drag and is the reason why we need such strong starters.
There should be a brushless motor that will easily start your engine and if you use the usual RC turbine coupling on the brushless you should be OK .
Cheers John
|
|
tegwin
Member

Joined: February 2012
Posts: 19
|
Post by tegwin on Mar 17, 2013 17:33:59 GMT -5
Hi John. Do you know if there are any calculations that allow a volume/pressure head of air required to start a specific engine? I have a centrefugal workshop air blower like the one in the image... which could run off 12V...Nothing compared to a proper leaf blower but I am keen to get everything running "hands off" and all from a single 12V battery. I am sure I have seen the turbokart build thread in the past but I don't seem to be able to locate it now. Search seems to be a bit hit and miss. The Bendix arrangement certainly looks the part! Thanks. Duncan
|
|
|
Post by racket on Mar 17, 2013 20:14:08 GMT -5
Hi Duncan Setup a water manometer , 2 metres of 3/8" plastic tubing with a foot of water up each leg of the "U" , then stick one end of the plastic tube into the blower outlet , if you can get a 6 inch water height difference in the manometer that should be sufficient . LOL......you could always try running 24 volts through the blower to get extra pressure and flow for a short burst , pressure increases as the square of the impellor tip speed so a doubling of rpm will give 4 times the pressure . This is the GT6041 Thread jetandturbineowners.proboards.com/index.cgi? board=diygeneral&action=display&thread=78 .... just 5 down the List from your Thread in the DIY section Cheers John
|
|
tegwin
Member

Joined: February 2012
Posts: 19
|
Post by tegwin on Mar 27, 2013 13:46:18 GMT -5
Not yet managed to experiment with the blower but I have re-build the combustor using a larger bore tube and more appropriate hole layout. 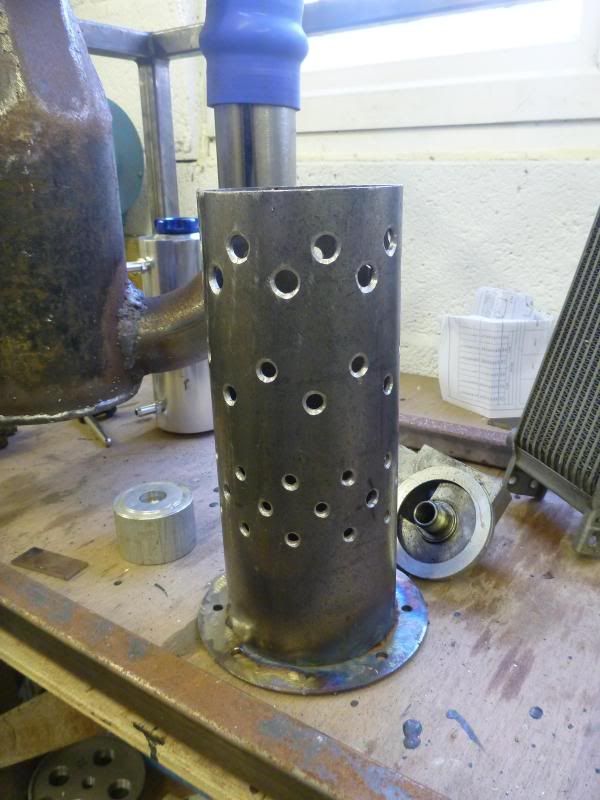 Have also been busy fabricating mounts to join my motor and fuel oil pump together. Seems a fairly compact solution and not too expensive either which is always a bonus.  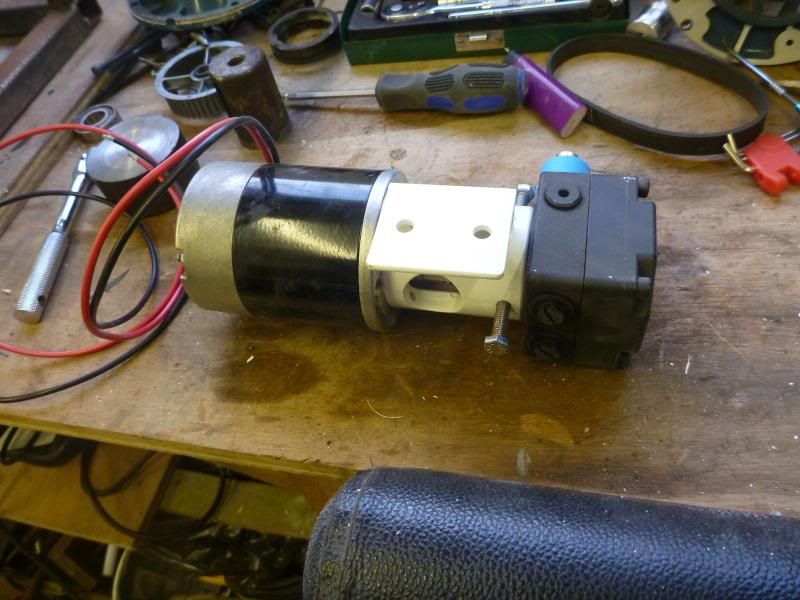 Next to be dealt with is the oil supply pump, then I can start trying to plumb it all together. Seems a huge variety of threaded connectors on each component!
|
|
|
Post by stoffe64 on Mar 14, 2014 3:54:28 GMT -5
how is the build going friend? cheers/stephan
|
|
tegwin
Member

Joined: February 2012
Posts: 19
|
Post by tegwin on Apr 2, 2014 5:43:03 GMT -5
Hi guys. Thought I would post an update and ask for some help. Diesel nozzle, gas nozzle and combustor drain: 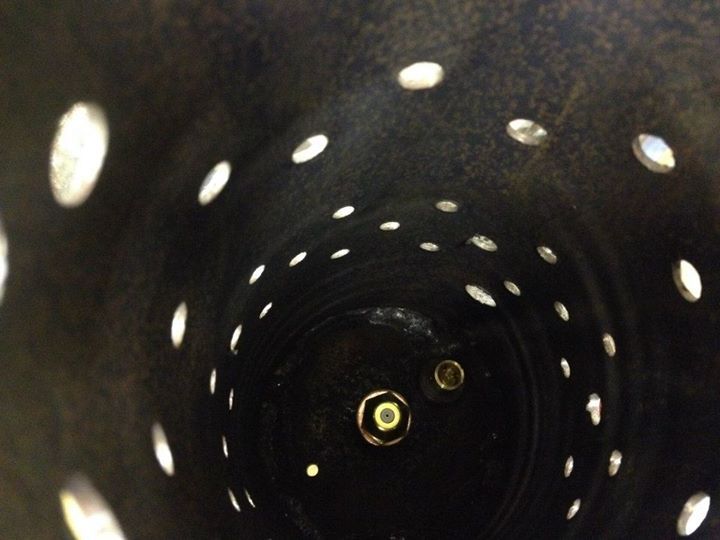 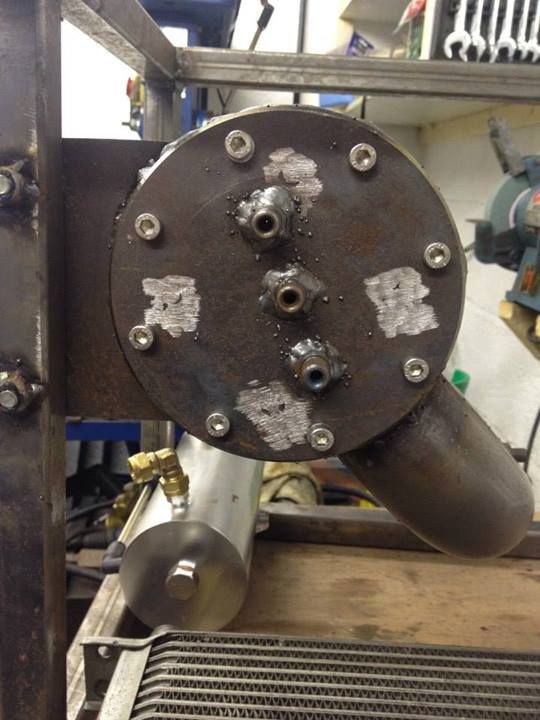 Propane test: 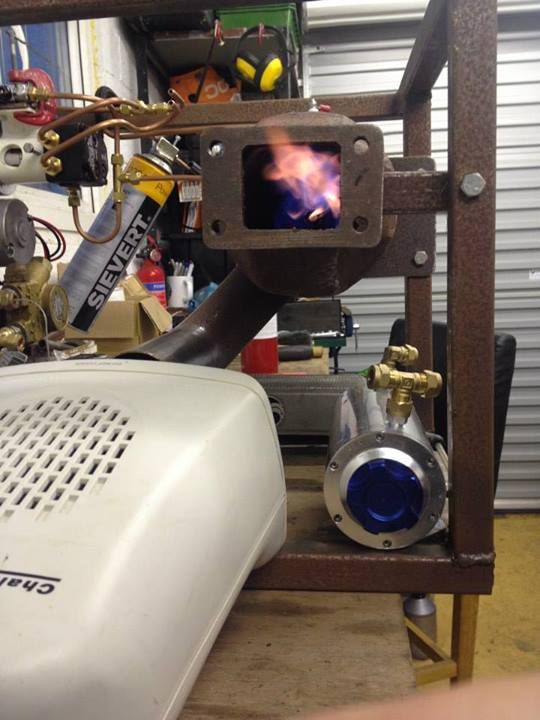 Diesel pump: 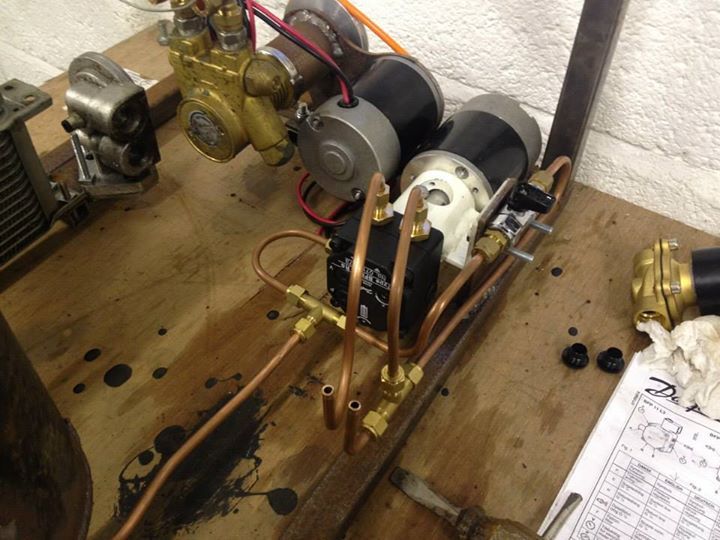 So having spent ages plumbing the diesel pump in to place using a diverting fuel system like this: 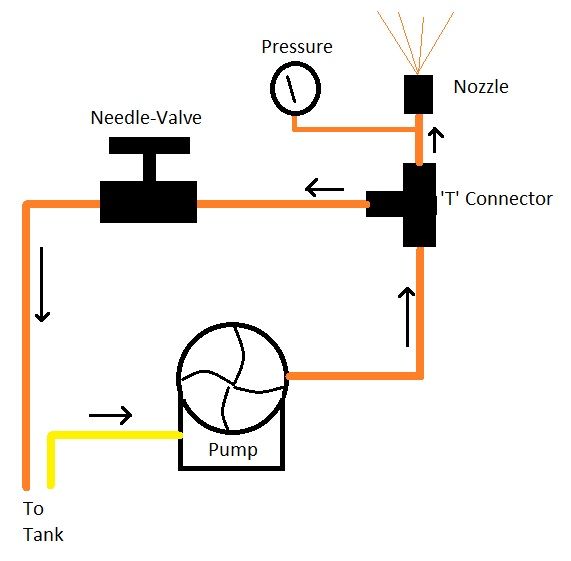 I had a go at burning some diesel. I can get the gas to light off easily with the sparkplug and then get some diesel to burn however I seem to be only burning half of the fuel, the rest drips out of the combustor drain. I suspect I have poor atomisation or insufficient air being fed into the combustor. The nozzle is a 6GPH unit. I am a bit stumped as to what to try next. This video shows what is going on. The yellow flame is the diesel burning. Ideally the combustion all needs to be occurring inside the combustor so I am not really sure what is going on...Thoughts appreciated 
|
|
|
Post by racket on Apr 2, 2014 19:57:37 GMT -5
Too much fuel for an "atmospheric" test , you need only a small fraction of the turbine engine use , replace the spray nozzle with a 1 gph one .
Cheers John
|
|
tegwin
Member

Joined: February 2012
Posts: 19
|
Post by tegwin on Apr 3, 2014 4:55:27 GMT -5
Thanks for the reply John. Are you suggesting that when the combustor is up at working pressure it may well burn the fuel properly in its current setup?
|
|
|
Post by racket on Apr 3, 2014 17:41:29 GMT -5
Yep, once the compressor is supplying pressurised air things will be OK with the larger spray nozzle, but with just a leafblower supplying air the limited airflow only requires limited fuel to achieve the desired discharge temperature from the combustor , this temperature will be the same as your "running" T I T , which would be up to 150 deg C hotter than our usually measured TOT , so aim for a discharge temp of ~800 deg C (without external flames) during your "atmospheric" testing, there should only be a small flame at the primary zone end of the flametube , preferably within a few inches of the spray nozzle.
The limited fuel flow during an atmospheric test will require a small spray nozzle to produce the required fine atomisation , you'll need to be running a fuel pressure of >50 psi to get anything like half decent atomisation .
LOL...........I've never conducted an atmospheric test on any of my engines , so I'm only conveying what I've been told is the way to do it :-)
Cheers John
|
|
tegwin
Member

Joined: February 2012
Posts: 19
|
Post by tegwin on Apr 4, 2014 4:53:54 GMT -5
Thanks for the explanation John. That makes pretty good sense. Other than checking that I can get ignition an atmospheric test of the combustor is not going to tell me much I guess. My only concern is that before full combustion pressure is reached I am going to have too much fuel which in all likelihood is going to give me a hot start. I suppose that's easily changed with a different nozzle. (or potentially a separate diesel nozzle for start up) Need to get the oil system plumbed in and then I can give it a go and see if I can get the thing to actually run without melting the spinning bits... One thing I have learned is that my gas nozzle is hopeless, too much air flow and it gets blown out. Think I need to look at that before I go much further
|
|
|
Post by racket on Apr 4, 2014 19:01:57 GMT -5
Generally theres not much problem during a start even when quickly opening the fuel up to idling flow rates , the turbine parts are cold and they take time to heat up so no danger of melting anything as long as spoolup is restricted to less than 30 seconds , the unpressurised air tends to keep flame temperatures lower than when running pressurised.
How are you going to "throttle" the engine , just with the needle valve ??
What you can do is fit a "safety" ball valve on your line between the pressure gauge tee and the spray nozzle and prior to spoolup with this valve closed and the needle valve off its seat by a predetermined amount and the pump operating ,there will be a pressure reading on the gauge , this pressure will be higher than when the ball valve is opened and the engine running , but once you have the engine idling simply close this ball valve and whatever reading you have on the gauge you simply set the needle valve throttle at that pressure reading before each start .
Slowly opening the ball valve during spoolup whilst watching the pressure gauge allows us to get a predictable spoolup to idle.
A propane pilot light will give you a reliable ignition of the liquid fuel spray , so spend a bit of time getting it sorted :-)
Cheers John
|
|
kerndog
New Member
Joined: March 2014
Posts: 1
|
Post by kerndog on Apr 6, 2014 8:33:57 GMT -5
We used two burner nozzles and pumps (ADC model) and achieved very good results for our project so far. The nozzle looks very similar to yours. We used a spark plug for ignition and two nozzles feeding from a manifold to feed a S586 based jet project. If you don't mind profanity and a crude build, it can be seen here: www.youtube.com/watch?v=6dxe21Sp_P4Another video on the same channel at 17:30 shows what I think is good response for the flame using the same diesel nozzles. I know its very rough around the edges, the budget was next to nothing and just getting it started and idling was an accomplishment for us. I didn't want to thread hijack, but since we used similar parts, I felt I could speak on your thread. We used an air compressor discharge line straight from the tank for spooling the turbo and atmospheric testing. When conducting atmospheric tests, if we used a full compressor tank at 175 psi and opened the valve over a 2 second period after ignition the flame went from extending beyond the turbine mounting flange 18" to roaring and staying within the combustor.
|
|
|
Post by angryseabass on Apr 10, 2014 10:23:10 GMT -5
Hi Tegwin Propane/LPG injection to provide a "pilot light/flame" for the subsequent injection of the diesel spray ( with its fairly coarse atomisation at the low idle flow range pressure) will produce an easier ignition with the usual spark plug arrangement that can be "over whelmed" by the diesel spray causing it to cease sparking as it gets flooded. Propane/LPG injection is commonly used in liquid fueled steam boilers to provide positive ignitions. ..................once the liquid fuel is positively ignited the propane/LPG is shut off . . There are "off the shelf" liquid fuel ignitions available for the RC micro turbines , at quite reasonable prices , checkout a large online supplier , they use a "glowplug??" with liquid fuel flow across the glowplug wire to produce a "flame" to preheat the evaporators ,............ most RC micro turbine engines use propane/LPG preheat .......................I've always used it on all my engines because I've never had a "turbine" grade ignition system with its very high energy (lethal) power output that can cope with "flooding" levels of liquid fuel spray . Cheers John Hi Everyone , I have been lurking for a few months now and have learned so much from this site, thank you everyone . I am about half done my build and will try and post some pics and info soon. I have one question ,I am planning on using diesel fuel to run my engine and was planning on using propane to start it. I have an automotive fuel pump from a Subaru and will be using a injector nozzle of some sort .If I use propane to ignite the diesel coming out of the nozzle will I need to build an evap system as well or will combustion continue once everything gets nice and hot without evap tubes ?. Thanks for any help/advice .
Mike
|
|