tegwin
Member

Joined: February 2012
Posts: 19
|
Post by tegwin on Feb 21, 2012 9:36:58 GMT -5
Thought I would say hello and introduce my new project... after years of having "better things to do" I have finally got myself organised and started collecting parts for a lo-cost twin shaft turboshaft engine. I dont have access to a TIG welder(only mig) so for the time being I will build this out of mild steel. This restricts things to a fairly conventional gas powered turbine. Evap tubes from MS sound like a bad idea! I had wanted to build my own turbine housing for a proper cylindrical combustion chamber rather than the typical "bolt on the side" jobbie that most turbos use, but without stainless and TIG I think this would be a bad idea for now! The idea is to build a self supporting turboshaft engine so all systems will be 12V with FADEC for one press start/stop.... thats the plan anway! The turbo is a reasonably sized K28. 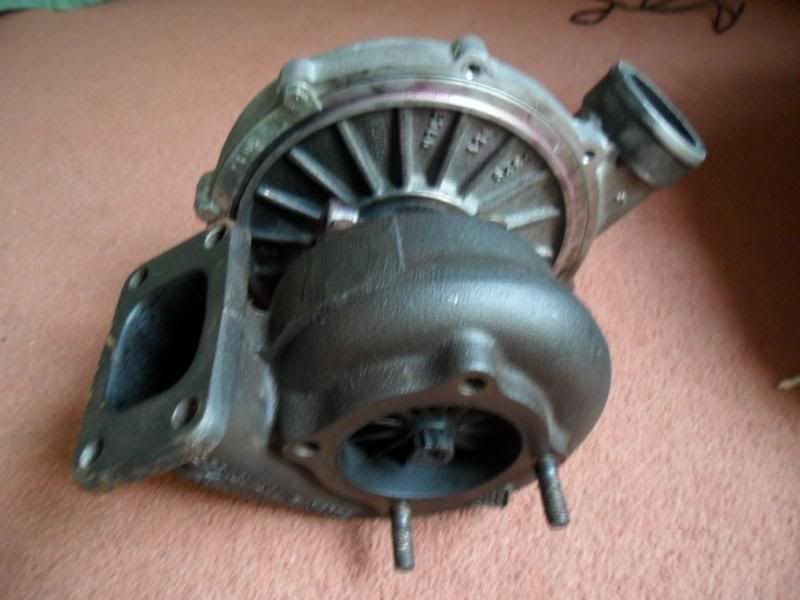 Have an oil cooler, filter, pump etc 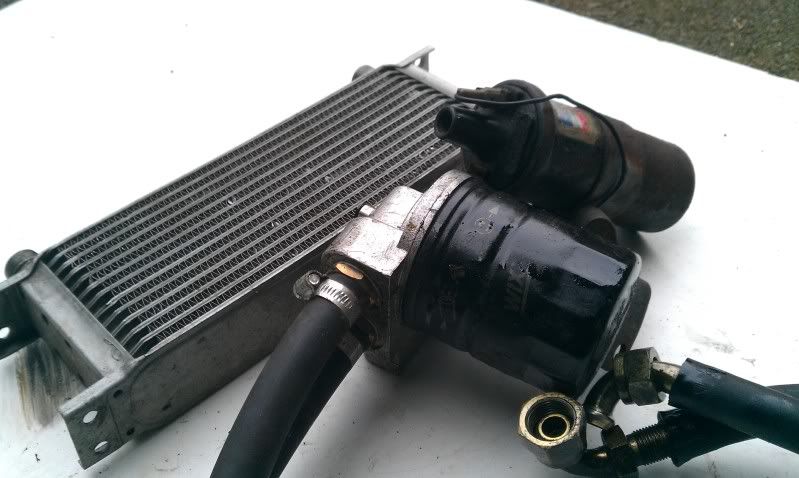 My research suggests I am going to need to spin the turbo up to around 25-30,000RPM to start things going. I dont want to use a leaf blower. So I could try and find a 12v blower with enough grunt like this one? www.ebay.co.uk/itm/2500-Ltr-Boat-Bilge-Blower-12v-Electric-Turbo-Blower-/110818008480?pt=UK_CarsParts_Vehicles_BoatEquipment_Accessories_SM&hash=item19cd449da0, or fit an electric motor to the compressor using some kind of bendix arrangement to engage the starter.. What have other people used to start their engines? Assuming I need around 30,000RPM, what size motor (brushless) should I be looking for? As soon as all my bits start turning up in the mail I can start designing the combustor and getting stuff stuck together :-)
|
|
|
Post by racket on Feb 21, 2012 16:38:29 GMT -5
Hi Tegwin
Welcome to the Group :-)
I think you'll be needing closer to 45,000 rpm for a reliable idle setting , your comp is only a bit over 3" dia , ............... leafblowers need pressure as well as CFM , the pressure component is needed to allow for the restrictions to flow across the engine , without "pressure" there will be little flow and minimal start capacity .....................unless the bilge blower can produce a pressure of at least 12 inches of water head , ~0.5 psi, you'll need to find something else.
MIG can be used for stainless , just need the right "wire" and some gas.
With "brass bush" bearings theres considerable start load , any brushless motor will need to have plenty of torque as well as rpm , on 12 volts alone you might not find that .
Cheers John
|
|
tegwin
Member

Joined: February 2012
Posts: 19
|
Post by tegwin on Mar 10, 2013 14:36:02 GMT -5
So I started this project over a year ago and actually have done very little... Not good. So I want to try and get it going. But I think I am going to need some help from some of you well educated guys. Currently things look like this:  I need to sort a fuel system, a lubrication system and a starting system... (So not much then!) Figure I will tackle one at a time...so fuel system... Looking at the research I did way back I recon a 6GPH 80 degree nozzle should be a good place to start. The plan is to use diesel with a recirculation type system to meter the fuel to the nozzle like this:  I have been given a Danfoss RSH125 fuel oil pump which is rated at about 45 gallons/hour at 30 bar (435psi). However the DC motor I had intended to use won't be man enough to spin the pump. The issue I have is, I am not sure how much pressure/flow rate I will need so selecting a pump is an issue. The smaller Danfoss fuel oil pumps can deliver around 10Gph at 100-150PSI... But I am not sure that would be enough. Any thoughts?
|
|
|
Post by racket on Mar 10, 2013 19:49:06 GMT -5
Hi Tegwin 10GPH is probably big enough , your dump fuel control is OK , but I'm not too happy about that flametube , how did you determine hole sizes/placement as well as diameter of flametube??
Cheers John
|
|
tegwin
Member

Joined: February 2012
Posts: 19
|
Post by tegwin on Mar 11, 2013 5:06:26 GMT -5
Hi John. Thanks for the reply. So the 10GPH pump might be ok but would a pressure of 100-150PSI be enough to atomise the fuel suitably to get a good ignition/burn? (I did not intend to use an evaporator) I can't find the document now but I think it might have come from the yahoo turbine group. It had some simplified formula for calculating tube sizes, bypass area and hole area in the combustor. I wish I could find the calculations/drawings I did but i cant locate them to help validate the design  What is it specifically that you don't think looks right on the combustor?
|
|
|
Post by racket on Mar 11, 2013 16:36:32 GMT -5
Hi Tegwin 150psi will produce reasonable atomisation . "Bypass Area" .......I hope you don't mean theres an annular gap at the outlet end of your flametube .....................this is an antiquated method of dilution air presentation and fraught with potential problems , must better to use a "full length" flametube (with slipjoint for expansion) with dilution holes of a certain fixed area rather than the bypass area which will change depending on flametube axial expansion . There is Jetspecs on the DIY Gas Turbines Site for flametube/combustor sizing ... . tech.groups.yahoo.com/group/DIYGasTurbines/files/1_Starter%20Pack/ Could you give me the diameters of your compressor wheels inducer , and the exducer diameter of the turbine wheel ( hole in and hole out) , and your flametube hole sizes and number and its dimensions , so that I've got a better idea of what your flametube should be sized ...............hopefully its just camera angle thats making it look wrong . Cheers John
|
|
tegwin
Member

Joined: February 2012
Posts: 19
|
Post by tegwin on Mar 12, 2013 13:06:10 GMT -5
Hi John. Not sure what document I used to design this comsbustor but the jet-specs makes a lot more sense! I do indeed have an annular gap between the end of the flametube and the combustor for "bypass". Doing a re-design and altering things is not an issue if it means this thing might actually work properly  The turbo inlet is 62mm and the outlet is 73mm. The current combustor is as follows: Flametube diameter=85mm, Length 245mm Combustor housing diameter=140mm There are 56x6mm holes and 21x8mm holes giving a total area of 2865mm^2 Can not remember the by-pass area between the combustor and flame tube but It was something around 1500mm^2 I guess from looking at it. I could modify the existing setup (assuming tube diameters are acceptable) and remove the bypass and alter the holes as per jetpsecs.
|
|
|
Post by racket on Mar 12, 2013 17:24:36 GMT -5
Hi Tegwin
With a 62mm comp inducer you'd normally only be needing ~3,000 sq mms total flametube hole area , but you appear to have a fairly larger turbine stage so possibly a bit more area wouldn't go astray , maybe 3500 sq mms .
At 85mm dia your flametube is a bit small if wanting to use sprayed liquid fuel at modest fuel pressures ( 150psi) , I'd suggest going up to ~100mm as theres still plenty of clearance in your 140mm outer can .
Make the flametube full length with a "rattly" slip joint at one end , it won't matter if theres some minor air leakage thru the slipjoint as long as the joint doesn't bind up when the flametube is fully expanded at running temps .
As for holes in the flametube ,... Primary zone holes opposite the fuel spray , ~1,050 sq mms made up of 6mm holes with 3 or 4 opposing holes of 8mm dia for some centre penetration , so lets go 30 X 6mm and 4 X 8mm in maybe 3 rows positioned just above, at, and below where the spray would hit the walls , this will depend on your spray angle and fuel nozzle position .
Secondary holes mid way down the flametube , lets go 14 X 8mm holes .
Tertiary holes near the outlet end of the flametube , 16 X 12mm holes .
Try and give the holes a bit of a "countersink"( bellmouth) at the inlet side to aid airflow into the holes .
Your current setup with a large annular bypass normally causes problems due to the air taking the easiest route and simply slipping through the bypass starving the Primary Zone of air with combustion problems the result , by making all of the air pass through wall holes there is a more controlled distribution .
Hope this helps :-)
Cheers John
|
|
tegwin
Member

Joined: February 2012
Posts: 19
|
Post by tegwin on Mar 12, 2013 18:40:50 GMT -5
Hi John. Thank you for clearing that up. Very useful and much appreciated. I will see if I can get hold of some 100mm diameter tube and get drilling. Need to find some way of altering the diverging end of the combustion chamber so I can fit a slip ring for the flame tube to sit in. Should be a fun challenge  I had intended to fit the nozzle central in the end of the flame tube and to use an automotive type spark plug to ignite the diesel. Do most people mount the spark plug on the end plate next to the nozzle or half way up the combustor where the fuel is more likely to be atomised? Again, thank you for taking the time to help! Starting to feel a bit more motivated to get back into the workshop! 
|
|
|
Post by racket on Mar 12, 2013 19:26:35 GMT -5
Hi Tegwin
If fitting the spark plug to the side of the flametube fit it where the starting propane can easily be ignited , if fitted to the endcap ( which is easier) there can be ignition difficulties with a vertical combustor , your "underhung" one won't suffer as badly due to the propane being heavier than air will fall to the bottom where the plug is , a lot of engines use that position successfully and it doesn't require the "complexities" of the side mount.
A slip ring could be welded into the tapered section of your outer can , it doesn't have to be a perfect seal , if theres a few gaps here and there just deduct their area from the main dilution holes (12mm ones) in the flametube by drilling less 12mm holes .
Make a cardboard template for the slipjoint first , much easier than cutting metal ......LOL, if you're like me I have to make half a dozen before I get close to the right shape :-)
Cheers John
|
|
tegwin
Member

Joined: February 2012
Posts: 19
|
Post by tegwin on Mar 13, 2013 4:48:17 GMT -5
Hi John. Yes, cardboard is the way forward! I wish steel was as easy to cut  Interesting that you mention using propane to start the engine. Is this the norm? I was rather hoping that the atomised diesel could be lit off directly without the need for a propane system. I think I need to build the fuel supply system and do some experiments to ascertain how difficult/easy it will be to ignite the diesel using a sparkplug. Thanks.
|
|
|
Post by stoffe64 on Mar 13, 2013 4:56:11 GMT -5
hello Tegvin! you can also use a glowplug from a car, that should ignite the mix qite ok i think! cheers/stephan
|
|
tegwin
Member

Joined: February 2012
Posts: 19
|
Post by tegwin on Mar 13, 2013 8:20:35 GMT -5
Hi Stephen.
That is an intersting point.
Quick bit of research suggests the flash point of diesel is around 60c and the autoignition temperature is around 210c.
Most glow plugs reach temperatures of around 500-800c.... So in theory, a glowplug WOULD do the job! Will have to experiment with one.
|
|
|
Post by racket on Mar 13, 2013 17:14:03 GMT -5
Hi Tegwin
Propane/LPG injection to provide a "pilot light/flame" for the subsequent injection of the diesel spray ( with its fairly coarse atomisation at the low idle flow range pressure) will produce an easier ignition with the usual spark plug arrangement that can be "over whelmed" by the diesel spray causing it to cease sparking as it gets flooded.
Propane/LPG injection is commonly used in liquid fueled steam boilers to provide positive ignitions. ..................once the liquid fuel is positively ignited the propane/LPG is shut off . .
There are "off the shelf" liquid fuel ignitions available for the RC micro turbines , at quite reasonable prices , checkout a large online supplier , they use a "glowplug??" with liquid fuel flow across the glowplug wire to produce a "flame" to preheat the evaporators ,............ most RC micro turbine engines use propane/LPG preheat .......................I've always used it on all my engines because I've never had a "turbine" grade ignition system with its very high energy (lethal) power output that can cope with "flooding" levels of liquid fuel spray .
Cheers John
|
|
|
Post by Johansson on Mar 13, 2013 17:26:10 GMT -5
I vote for a propane pilot flame during startup as well, we used a small 2GPH starting spray nozzle on the kick sled but despite 5 bar fuel pressure and a strong spark we had severe problems getting the diesel mist to ignite.
A propane injector into the primary zone solved the problem.
|
|