|
Post by racket on Dec 26, 2010 16:42:06 GMT -5
Hi Anders /Stephan
LOL.......heating water in a pressure vessel is what I use to do for a job as a steam boiler fireman , musta burnt thousands of tons of fuel boiling water over the years.
What you must NEVER do is subject a metal surface to flames without water on the other side (superheaters are a different scenario), all boilers have sight glasses so you can keep the water level in the boiler above any heating surface .
Its EXTREMELY DANGEROUS to play with high temperature/pressure steam contained in large volume vessels unless you're suitable trained and qualified .
LOL.......having said what I have to say ;-) ........................an oxy bottle should be more than strong enough if that precaution of never heating a surface without water on the other side is followed .
Working backwards from your intended steam pressure , its temperature will be known as will the water temperature and the steel of the bottle , a quick check of steel tensile figures at that elevated temperature will confirm if its going to be exceeding the relative stresses that it encounted under the oxy pressures .
Heres a few temps for you, at 200psi steam starts to form at 381 deg F , 300psi 417 F , 450psi 456 F , 600psi 486 F ..................I don't think you need any higher ones .
Gas temperatures in a coal fired boiler are very high but the metal heating surfaces aren't , you might find that a steam boiler running 100 mm dia water tubes will only have tube wall thicknesses of 5mm or so even at 200 psi working pressure
My personal thoughts ..................don't try it , it really is extremely dangerous .
Cheers John
|
|
|
Post by Johansson on Mar 22, 2011 3:16:21 GMT -5
An update on the rocket idea, since we won´t be allowed to race with a pure rocket vehicle because of spectator safety we are thinking about fitting a rocket engine to the existing gas turbine kick and use it as a booster somewhere down the track.
Since the jetbike has higher priority my idea is to build a hybrid rocket instead to cut some manifacturing time, I´ll do some research regarding fuel cell material and nozzle sizing and get back to you.
|
|
|
Post by racket on Mar 22, 2011 14:31:42 GMT -5
Hi Anders
Good to see you're already thinking about next years event , you must have had a very good time out there on the ice :-)
Cheers John
|
|
|
Post by Johansson on Mar 23, 2011 7:22:15 GMT -5
That is the interesting part about racing, when the weekend is over you are exhausted and more or less tired of engines and metal work and promise yourself that you will take a long break from the workshop and catch up with other things for a while.
Three days later you find yourself eagerly making drawings and ordering parts for next years engine project... ;D
Whether we will use the rocket engine on the kick or not time will tell, I have never built a rocket engine so that is the main reason why I want to make one. If it proves to be reliable to the point that I or one of my friends want to stand right in front of it while running then we might consider strapping it to the kick.
Parafine looks like a good choice of fuel right now, easy to cast a fuel grain from and not at all messy like asphalt. Plexiglass is another option but then we would have to order solid bars to make the grain from since it cannot be cast.
|
|
|
Post by racket on Mar 23, 2011 16:30:59 GMT -5
Hi Anders
LOL...... can't keep a man out of his shed for long :-))
Do you have any literature on building your rocket ??
Cheers John
|
|
|
Post by Johansson on Mar 24, 2011 2:50:38 GMT -5
I´ve found good guidelines at www.thefintels.com/aer/rocketindexold.htm so we have all the information we need to build a test engine. We need to know Isp for the fuel and oxidizer at the chamber pressure we will run at, and that figure we can only find by testing.
|
|
|
Post by racket on Mar 24, 2011 3:28:02 GMT -5
Hi Anders
Heh heh heh , lotsa fun stuff on that Link :-) .................... it'll get you where you want to be .
Cheers John
|
|
|
Post by Johansson on Oct 25, 2011 15:52:27 GMT -5
Long time since I posted here, mainly because I haven´t had time to think about the bipropellant project. That is however about to change, I talked to Olov today and we found out that there is roughly two-three days of build time left on the jetkick before it is race ready so we will have plenty of time this winter to build the 500N rocket engine!  I´ll start sourcing some material for the engine and make up some crude drawings and get back to you.
|
|
|
Post by racket on Oct 25, 2011 19:36:22 GMT -5
LOL........deviate ;-)
|
|
|
Post by Richard OConnell on Oct 25, 2011 23:48:01 GMT -5
Rockets make me smile 
|
|
|
Post by Johansson on Oct 26, 2011 16:55:41 GMT -5
I started the build today, 500N felt a bit whimpy so I decided to build a 1000N engine instead. Much easier to build when the throat diameter is large enough for the lathe tools to fit in there. 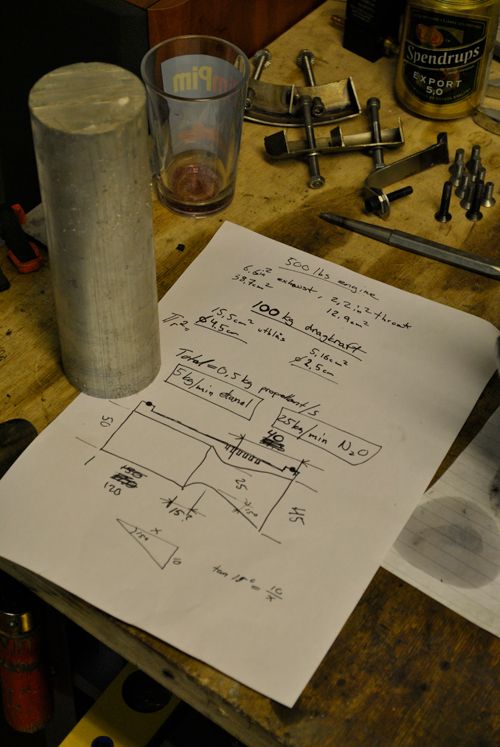 The throat is 25mm in diameter, nozzle exit 45mm in diameter and the combustion chamber is 45mm x 120mm long. The engine is made from one piece of aluminum with a hydraulic cylinder as the cooling jacket for the regenerative cooling, it will also act as a burst screen in case the engine decides to blow up on us or burn a hole in the CC wall. 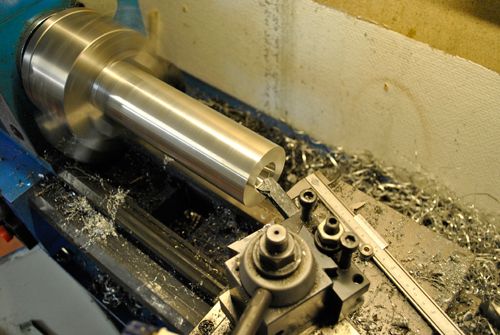 We will run it on nitrous oxide and methanol, the fuel tank will be pressurized by nitrogen since there isn´t any reasonable priced fuel pumps that can produce the kind of pressure and flow needed. 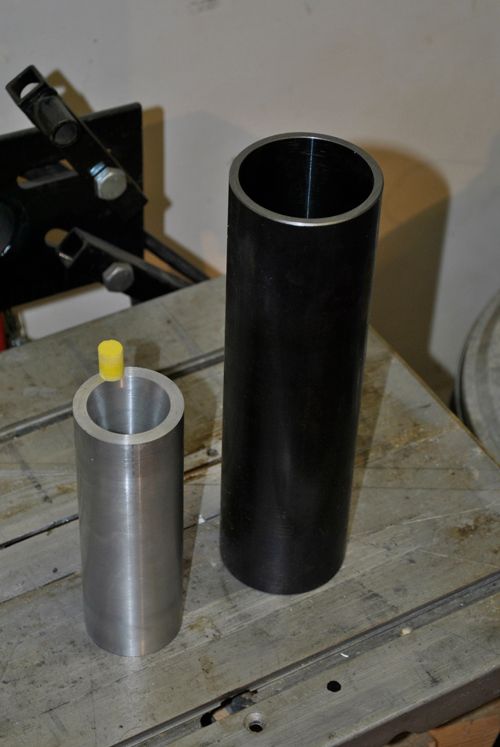 The back side of the combustion chamber, not much to see at this point. 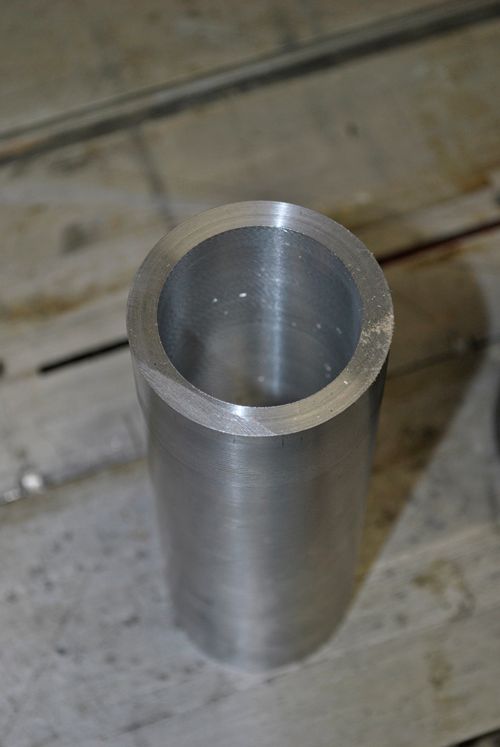 Cheers!
|
|
|
Post by propellanttech on Oct 26, 2011 17:42:07 GMT -5
Have you thought of using the self pressurizing nature of the NO2 to use for pressurizing the fuel??
I have seen this done, and it is real slick, but the parts must be of non-organic composition.
It is a simple method, but complex in design. It is somewhat of a duplex steam water pump, for a simple explanation.
It will waste some of the NO2 (to decomposition), but lightens the load somewhat of the extra tank, and also lowers the risk of the higher pressure of N2. The weight difference is up to how well you can design the pump, with respect to weight. With aluminum, and a small pump, the weight savings could be significant.
If you want to go more simplistic, look up RATT motor works. They have a slick tri-brid (one oxidizer, two fuel) rocket motor design. It uses a piston to pressurize the fuel from the NO2. It's as simple as it gets.
I'm a rocket junkie as you can tell.
James
|
|
|
Post by Johansson on Oct 26, 2011 23:03:41 GMT -5
I had an interesting email conversation with Carolynne (the hybrid rocket dragster lady) earlier about using hydraulic cylinders as N2O tanks and a piston with nitrogen pressure above to control the injection pressure and assure that no N2O boils off in the feed lines. The thought about using N2O to pressurize the methanol sort of gives me shivers, what if a piston seal springs a leak and lets the nitrous oxide through to the methanol without us even knowing it?  It would be simple as hell, but I don´t know if I dare to take the risk. (And that is something I don´t say every day...  Another reason why a regulated nitrogen supply would be a better choice is because I then can alter the nitrogen pressure to adjust the fuel mixture in case it runs lean or rich instead of having to make a new injector plate with smaller holes. Any needle valves or other restrictions in the feed lines are a big no-no since I want to have the pressure drop over the injector and nowhere else.
|
|
|
Post by enginewhisperer on Oct 27, 2011 1:07:25 GMT -5
you could also use CO2 to pressurise the fuel (similar bottle pressure to N2O, liquid storage, etc)
|
|
|
Post by propellanttech on Oct 27, 2011 10:28:35 GMT -5
I had an interesting email conversation with Carolynne (the hybrid rocket dragster lady) earlier about using hydraulic cylinders as N2O tanks and a piston with nitrogen pressure above to control the injection pressure and assure that no N2O boils off in the feed lines. The thought about using N2O to pressurize the methanol sort of gives me shivers, what if a piston seal springs a leak and lets the nitrous oxide through to the methanol without us even knowing it?  It would be simple as hell, but I don´t know if I dare to take the risk. (And that is something I don´t say every day...  Another reason why a regulated nitrogen supply would be a better choice is because I then can alter the nitrogen pressure to adjust the fuel mixture in case it runs lean or rich instead of having to make a new injector plate with smaller holes. Any needle valves or other restrictions in the feed lines are a big no-no since I want to have the pressure drop over the injector and nowhere else. The problem with using high pressure nitrogen. All components must be able to take full pressure from the nitrogen tank. This is a safety factor in case something goes wrong with the regulation system. If the system can not take the full pressure bad things could happen if the regulation goes wrong. With a piston, you would only use the vapor (decomposed) component of the NO2, and the risks are somewhat diminished. The only risk is at the end of the burn when the vapors are consumed from the tanks. Then there is a risk of a back flash. Also the seals should be some type of o-ring, not a typical ring seal. When dealing with items such as this, it is always risk management. I think I would rather have a back flash, than a tank bursting from over pressure. Either way, it was just a suggestion. James
|
|