|
Post by Johansson on Jan 20, 2012 12:25:02 GMT -5
More than a couple of nights if you consider the thickness of it... ;D Rest assured my russian friend (we have had previous email contact discussing steam rockets) that I will post videos of the rocket firings, a friend of mine has a high speed digital video camera that should produce some interesting footage. 
|
|
mator
Junior Member

Joined: January 2012
Posts: 76
|
Post by mator on Jan 20, 2012 12:30:34 GMT -5
Mmmmm.... High speed cameras are very interesting, I think!!!! And very practical.
|
|
|
Post by Johansson on Jan 21, 2012 16:53:53 GMT -5
Today I made the flow test rig for the injector plate, I used a fire extinguisher filled with water and pressurized with 10 bar from the garage compressor. First I hooked up the methanol injector and tested it. 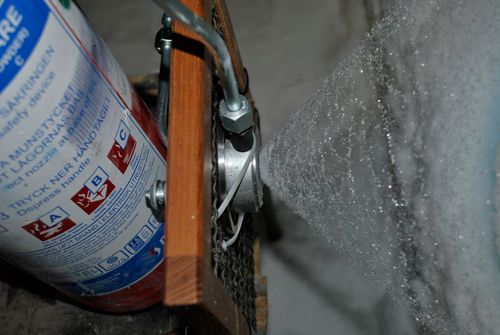 A nice and even 360° cone, it looks a bit crappy on the pic since the shutter time was set very short but it is as good as it gets with only 10 bar pressure. 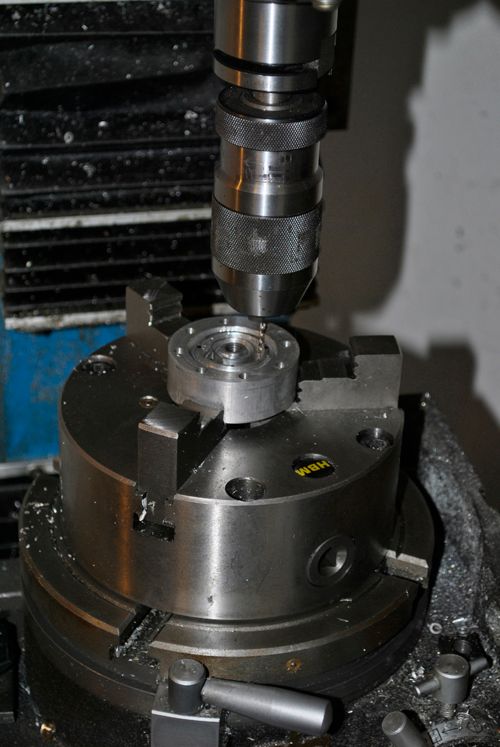 After that I drilled 8 1.5mm holes for the N2O, a design error earlier in the injector plate build kept me from drilling more holes (the feed hole for the fuel is overly large and therefore in the way) so this injector will be for initial testing only and a new one with 16 or so 1mm holes will be made later. 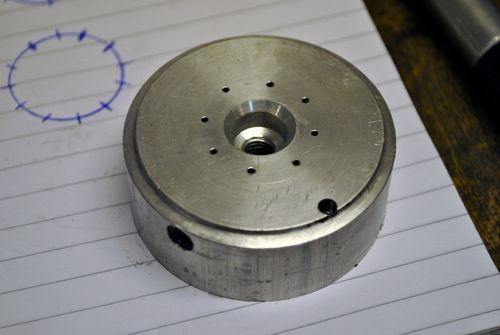 I fitted hydraulic lines for this injector as well and made sure to leave enough room for a pair of ball valves on the feed lines so I can test each injector separately later. 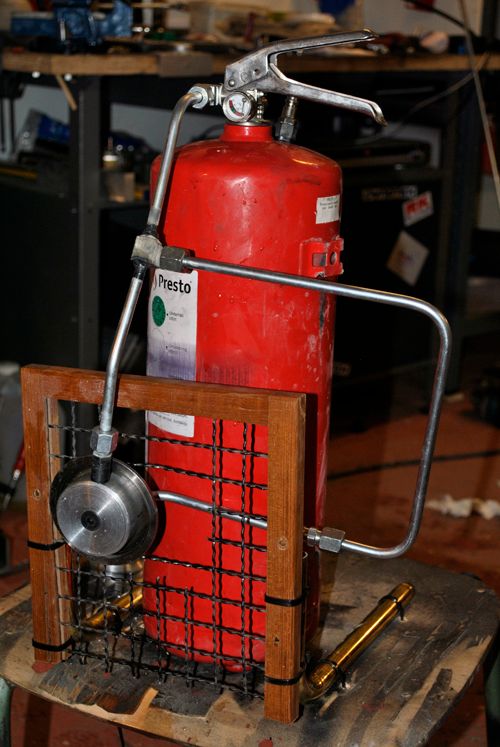 With the tank filled up with water I tested it again with both injectors flowing, it was clear that the 1.5mm holes are too large since the jets goes straight through the 360° fuel cone. Not much work to make a new injector plate so it will be interesting to do a new test with more and smaller N2O holes.  I might even drill the oxidizer holes at an angle towards the centre, I drilled them at a straight angle now just to see how it would work and I think it would be an improvement if the holes are drilled so they meet a couple of centimeters downstream. Cheers!
|
|
mator
Junior Member

Joined: January 2012
Posts: 76
|
Post by mator on Jan 22, 2012 10:21:29 GMT -5
Mmmm... Interesting work!! Is it possible then to make tests with 50 bar pressure? You have chosen 50 bar pressure in propelant injection sistem of your engine?
|
|
|
Post by Johansson on Jan 22, 2012 12:55:59 GMT -5
Not with the tank I am using now, 20 bar would work but anything higher than that would feel unsafe.  Even though the feed pressure will be 50 bar the pressure drop will only be 30 bar since the combustion pressure is expected to be around 20 bar, so when I have the high pressure "flight" tanks built I will use regulated scuba tank air pressure to simulate a real time run at 30bar injector pressure. I am more and more convinced that I will use an inert gas to pressurize the fuel and oxidizer tanks, here where the outside temps can differ 60°C depending on the season it would be difficult to run a self pressurizing rocket without severe mixture problems. Another benefit with this is that the thrust will be constant thoughout the run instead of an initial thrust peak that falls off more and more. 
|
|
mator
Junior Member

Joined: January 2012
Posts: 76
|
Post by mator on Feb 9, 2012 11:47:43 GMT -5
|
|
|
Post by Johansson on Feb 9, 2012 12:32:54 GMT -5
Never heard of him, thanks a lot for the links! 
|
|
mator
Junior Member

Joined: January 2012
Posts: 76
|
Post by mator on Feb 9, 2012 13:25:28 GMT -5
Yes. He is crazy guy!))) I like his rocket bikes and dreaming of my bike))) ;D
|
|
mator
Junior Member

Joined: January 2012
Posts: 76
|
Post by mator on Feb 11, 2012 6:55:07 GMT -5
Do you suggest to take optimal components ratio in your engine? Which temperaure do you want to have in combustion chamber?
|
|
|
Post by Johansson on Feb 13, 2012 12:17:26 GMT -5
Nothing in this engine will be optimal in any way, I am glad if it doesen´t melt and produce some decent thrust.  Later I will bother my dull head with combustion temps and such but for now all I want is a fire show! ;D
|
|
mator
Junior Member

Joined: January 2012
Posts: 76
|
Post by mator on Feb 13, 2012 13:03:19 GMT -5
I just want to say, that if you dont want to have melted metal after explosion, you can let fuel components burn in not optimal ratio. In this case temperature will be much less. You can rise 2 times the flow one of components (which is cheaper maybe), than needed. And temperature of burning will decrease in several times. But if you caculate cooling and sure that component-coolant won't be overheated of course you can run your engine by optimal ratio of components. Have you calculate some parameters of your engine? I mean strength calculations, thermodynamics (heat flows in engine). If not, you will need to get into the bunker to be sure in safety))))))
I both think about oxygen-propanbutane engine. This components, as I think will be the most cheapest and easiest in purchasing. And put it on a bike))))
|
|
mator
Junior Member

Joined: January 2012
Posts: 76
|
Post by mator on Feb 13, 2012 13:16:26 GMT -5
I have a special program in my univercity, for calculating chemical reactions. If you want, I can help you.
|
|
|
Post by Johansson on Feb 14, 2012 1:32:12 GMT -5
I will let it burn a bit rich to hopefully save the nozzle throat from melting.
The outer jacket of the engine is made from a hydraulic cylinder steel tube so in case the engine blows up the scrapnel should blow out of the nozzle end, but rest assured that we will stay in cover during the first runs. =)
For now I would like to keep the calculations to a minimum, John has provided me with some "rough" nozzle dimentions and the rest of the engine is more or less a qualified guess on my part.
I find it more interesting that way, later I will punch some numbers to try to optimize it but not at this stage.
|
|
|
Post by Johansson on Feb 18, 2012 9:02:59 GMT -5
After a couple of less successful injectors I finished a triplet injector today with a central 1mm fuel injector and two 45° angled 1.5mm NOX injectors who all meet a centimeter downstream. 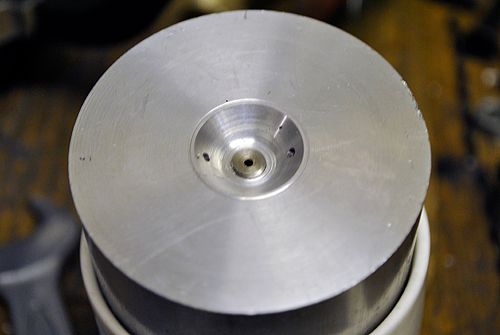 I used 10 bar air pressure an got a nice spray pattern, afterwards I flow tested each injector for 30 seconds and got 0.7L fuel flow and 3.0L nitrous flow. I opened up the fuel injector fom 1mm to 1.5mm to get the 0.5L/10s needed, the nitrous injectors will be kept at this size for now. Cheers!
|
|
mator
Junior Member

Joined: January 2012
Posts: 76
|
Post by mator on Feb 19, 2012 1:49:06 GMT -5
Cold Sweeden)))) Is it possible to make more injectors? In real rocket engines trere are hundreds of them. But on smaller engines of course lesser than hundreds))) And: you cool your engine by fuel? Alcohol?
|
|