|
Post by racket on Sept 19, 2017 17:25:44 GMT -5
Hi Anders
I'll do some numbers once I have those flow throat areas to get an idea of what might be going on .
The crack across your laby tip seal is pretty wide ( 4 -5mm ??) , I wonder why it hasn't closed up on cooldown , there must be enormous bending stresses in the blades either side , I did notice some wear marks in the seal shroud , could the sudden temp rise have allowed contact .....................is the wheel permanently "bigger" than its original diameter ??.
With your temp measurements in future , you might need thermocouples in different positions , perhaps a couple very close to the gas producer turbine exducer to check its outflow temp and then a couple more closer to the freepower NGV inlet to see if theres been any combustion in between once the gases have slowed to combustible speeds.
One thing I was going to ask, did your temps go straight up to high temps immediately on spoolup , or only once the oil and other metal bits warmed up somewhat ?? ....................I'm trying to workout if its fuel or oil burning and if it needs a hot metal surface for combustion .
Was there any "burning" on the interstage ductwork , ID and/or OD ??.
Yep , plenty of time to chew over the unknowns with JU-01 whilst burning kero in JU-02 :-)
Cheers John
|
|
|
Post by racket on Sept 21, 2017 4:30:26 GMT -5
Hi Anders Just been having a look at last years onboard camera www.youtube.com/watch?v=mcR_Q7AF1Eg , the temps ended up at roughly the same max , ............LOL, I hope that isn't against a "peg". Last years vid sorta indicates "normal" temps initially then they start to climb as it either took time for "fuel" to be fed to the interstage or it required the interstage material to heat up above ignition point for the "fuel" to start to burn .................interesting :-) Cheers John
|
|
|
Post by Johansson on Sept 21, 2017 12:24:58 GMT -5
Hi John,
One thing that talks against the oil/fuel leakage theory is that there is no smoke whatsoever from the exhaust, not at idle and not while running (as far as I can tell from the videos).
No signs of local burning inside the interstage, if by that you mean spots of blued/blackened metal. It all looks the same to me. No cracked and bent interstage vanes either that had blocked off parts of the NGV flow area.
It might perhaps be that the combustor is unable to burn all of the fuel so that streaks of fuel is sent downstream the turbine at high revs?
Cheers! /Anders
|
|
|
Post by enginewhisperer on Sept 21, 2017 17:08:47 GMT -5
maybe there's some strange combustor airflow happening that lets a vapouriser or two send liquid fuel out?
|
|
|
Post by finiteparts on Sept 21, 2017 20:05:37 GMT -5
Hi Anders,
I just got a chance to log in again and it is interesting to see the condition of the hardware. This is my theory based on the limited data from the photos.
Labyrinth seals are not really meant to rub against solid metal...they usually rub against something that is abradable like a very thin metal honeycomb or soft carbon material. When you have a clearance closure, the abradable material will give way and allow your turbines seal teeth to "live". Your power turbine is rubbing against a solid steel casing and there are some deep looking grooves on that casing. It takes alot of frictional energy to convert solid metal into liquid!
When you lost clearance and the turbine began to rub, it requires large amounts of input torque to keep it going...since you are applying the resisting force as far out on the turbine as possible. Potentially this torque was supplied by additional fuel or even by converting the motorcycles momentum and back-feeding torque through the gearbox to the turbine.
Now for the sake of argument, let's say that the rotor maintained its center-line and wasn't excited to some vibrational mode that would deform the outer seal diameter. If the rotor heated faster than the outer casing (very likely) and then the seal tooth started to rub the housing, the rub would put a lot of heat into the outer diameter that would cause the seal tooth to grow in diameter, increasing the rub and thus causing a self-exciting thermal run-away. The outer ring could have cracked when part of the rub "welded" to the outer casing and then snapped free due to the rotational inertia of the system. That might be one scenario that could have caused the cracking. The "braking" effect of the rotor rub could also explain higher temperatures as the power turbine would have less capacity to provide torque to the wheels since a portion of the absorbed power had to overcome the rub, thus a higher EGT.
Another scenario as to why the rotor cracked could easily be that the rub excited a vibrational mode and the tip seal cracked due to high cycle fatigue.
Finally, it could also be that the crack already existed and finally let go during this run. It should be remembered that these are usually Life-Expired parts and it could easily be that the fatigue build up over its life had already created internal cracks that finally showed up. The 250 engine has had a sorted past with contained and uncontained turbine failures, that has improved over the years, but the reason these wheels end up on eBay might be because they are old wheels that were phased out for the new designed components.
If you could put up some more photos of the rubs on the PT shroud and a close up of the fracture surface we might be able to back out some info. If you can't get any good close up photos of the fracture surface, maybe you can look to see if you see the tell tail fatigue "beach-marks" or if it looks more like a ductile/tensile fracture surface...(just Google "fatigue beach marks to see some example pictures).
Thanks!
Chris
|
|
|
Post by Johansson on Sept 26, 2017 15:44:13 GMT -5
Thanks Chris for your thoughts on this, I´ll take some pics of the wear marks and post them here for further discussion. Anyway, I think I might have found a reason for the high temps. The freepower guide vanes have distorted from the heat and narrowed the bypass area quite a bit. It was difficult to measure but the total NGV bypass area I got was 6090mm2 with a 9240mm2 area on the turbine wheel. 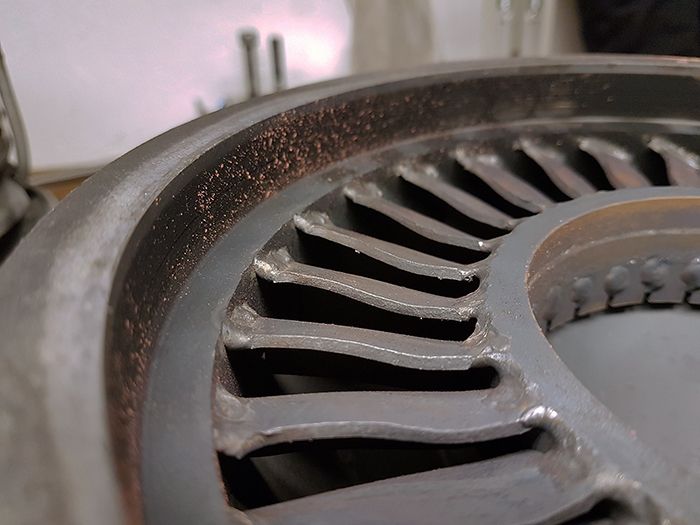 I haven´t dug deep enough into the build thread to find what the original NGV area was, I know I posted it some time during the construction so the numbers are around here somewhere. Cheers! /Anders
|
|
|
Post by Johansson on Sept 26, 2017 16:01:56 GMT -5
Compare this to a pic I found from after the first One Mile race, the vanes are much straighter then: 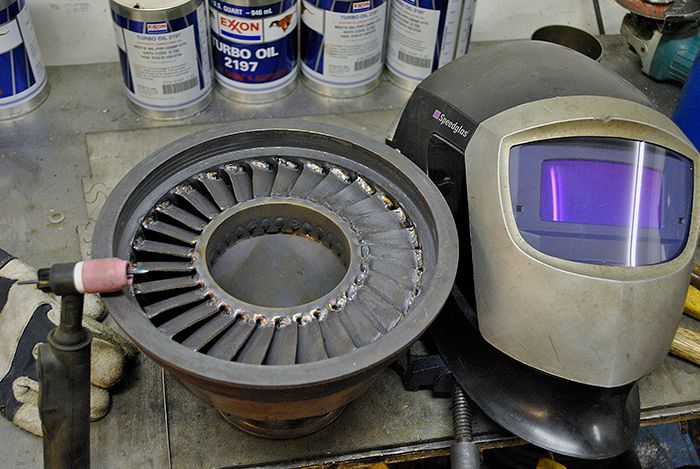
|
|
|
Post by racket on Sept 26, 2017 18:17:25 GMT -5
Hi Anders
Thanks for the areas ...............the NGV area isn't too bad , the wheel is still what it should be .
BUT.............the NGV has a nice buckle in the blade even now when its cooled down ..............lets have a think about when you fire the engine up.
The inner ring of the NGV is substantial and can't be "crushed" inwards , the outer ring is very strong as well and due to the thickness will take some time to heat up and expand to a greater diameter .
Now we come to those stainless vanes jammed between , they'll suddenly be subjected to say a 550 degree rise in temp at a minimum , 45 mm long vane of stainless will expand ~0.5 mm , but theres no where to go, so they buckle , that reduces flow area , which in turn starts to force turb temps higher , which in turn exacerbates the situation and before we know it we've got ITTs of 1,100 C and those vanes are trying to expand by 1.0 mm , but that thick outer rim in mild steel with half the coefficient of expansion has still only had a temp rise of maybe a few hundred degrees , those vanes are severely buckled :-(
On cool down , the vanes will shrink back to their "original" length pretty quickly whilst the outer ring will take longer , this should/may then end up leaving the vanes in some sort of tension even though theres still some buckling evident .
It might be an interesting experiment to fit the interstage duct to the JU-02 when you fire her up to see just how those vanes move around once the heat comes on, or even just put a large propane flame onto a vane to see what happens .
Expansion changes will need to be seriously considered when using the C20 NGV , allowing it to "move around" whilst staying concentric with the wheel .
Cheers John
|
|
|
Post by finiteparts on Sept 26, 2017 19:10:15 GMT -5
Hi Anders and John,
Yep...reduced flow area is a better reason for sustained higher temps than rotor rubs.
John, I agree with your description except for the end. As the vanes grow out and buckle, they also exceed the material yield stress and thus take on a permanent set. So when they cool back down, they will not shrink back to their original shape because they have already yielded in compression. They might go into a tensile stress state, but it is much less now that they have permanently grown in length, albeit, bent and not linear. It is good to remember that the yield strength of most material drops with temperature and if they are stainless (like a 300 series), then the yield stress limit drops really fast!
I have some PT6 first stage NGVs that also show the buckling due to poor thermal loading and they also exhibit the trailing edge cracking that you get from the repeated cycling of the NGVs between these compression then tension conditions. Eventually, the material reaches its LCF limit and cracks.
Stainless is really a garbage material for making hot, structural parts...but unfortunately, nickel and cobalt alloys are expensive and hard to machine (and weld sometimes)...so I understand the need to make stuff out of stainless. A John alluded to , many stainless steels (particularly the 300 series) have some high coefficients of thermal expansion, so when they get hot, they really grow. This makes it hard to keep them from yielding...so it is important to design the part so that it is only restrained at one location, that way it can grow without building up so much internal stress that it yields. NGVs are definitely tough to only restrain on one end. But I think you now have an actual NGV that is cast from a more stable nickel based allow, so hopefully, this isn't as bad of an issue going forward. As John said, mounting the NGV ring will be challenging.
Good luck!
Chris
|
|
|
Post by Johansson on Sept 28, 2017 14:06:15 GMT -5
That theory sounds perfectly plausible John, the heat makes the vanes expand and close the gap even further and when they cool off they return to this state. That might be why the engine idles at ok temps and after a short while the temp increases.
I have learned from this that I need to design the JU-02 interstage duct so that no stress is transferred into the NGV module.
One thought is that I will mount both the gearbox and gas producer rigidly in the frame and make a sliding coupling where the freepower NGV is. This way the interstage duct can grow and shrink as it wants to during the heat cycles and there won´t be any forces acting on the NGV.
Cheers! /Anders
|
|
|
Post by racket on Sept 28, 2017 16:47:06 GMT -5
Hi Anders
Yep, mounting the NGV will be a challenge , especially trying to maintain concentricity with the wheel assuming you'll be using the wheel shroud extension on the NGV rather than the interstage duct , but probably easier if you use your current setup and have the NGV free to move around even if its not exactly concentric with the wheel.
Would it be possible to "spring load" it at the OD so that it could expand and contract whilst still maintaining a rough concentricity .
A little bit of thought needed to get a satisfactory mounting , ..............but a lot less work than making a NGV :-) ............we'll throw some ideas back and forth to find a solution.
You might also need a bit more of a "warm up" period before your full throttle run to reduce the thermal risks.
Cheers John
|
|
|
Post by smithy1 on Sept 28, 2017 21:00:49 GMT -5
Hi Anders & John,
Would it be possible to use a proper RR250-C20B 4th stage NGV in Anders' setup..?? Not sure if I have one but I'll have a look though our "Quarantined" and time expired parts area next week...might be an option for you....at least you'll know the area is pretty close to correct...the only thing which may throw a spanner in the works is the missing 3rd stage wheel the 4th stage is expecting to see there...I wonder if we could fit them both in there??
Cheers, Smithy.
|
|
|
Post by racket on Sept 28, 2017 23:20:26 GMT -5
Hi Smithy
Yep, thats what Anders intends to use , he now has a couple of 4th stage NGVs , may need to blank off several of the passageways to get the right flow area , but thats for further down the development track , use as is for now and see how the temps are , then slowly blank off segments to get the temps/backpressure just right .
With the amount of energy we hope to have exiting the gas producer, a 2 stage freepower would be a better proposition to keep rpm down, but maybe too complex to fit :-(
Cheers John
|
|
|
Post by Johansson on Sept 29, 2017 14:40:20 GMT -5
We´ll figure something out guys. Have a nice weekend! 
|
|
|
Post by racket on Sept 29, 2017 23:02:37 GMT -5
Hi Anders
My head was clear enough today to do some maths , its been a bit fuzzy from a bout of the flu this past few weeks , so decided to checkout what might be required of a 2 stage freepower ..........it doesn't look good using C20 3rd and 4th stage wheels :-( , just not enough pressure energy to start with , resulting in gas speeds a bit too low to get the mass flow through ...........LOL, we need 1 and a half stages ;-)
A set of C30 wheels would be OK , but they're as rare as hens teeth .
Looks like we live with the C20 4th stage and "manipulate" things to get the best result , either "split" the outer seal for higher temps, or even remove it entirely for a higher rpm capability ...........at least I can now discount the idea of 2 stages, 1 it is .
Cheers John
|
|