|
Post by madpatty on Jun 3, 2014 19:55:33 GMT -5
Hi All
Thought of starting a thread on my recent projects that is a free power turbine build for the gas producer that i had built almost a year ago....
Was following up some recent builds on this forum in the same field...
It is an awesome thing how experts here interact with amateurs....
Cheers Madpatty.
|
|
|
Post by madpatty on Jun 3, 2014 20:01:04 GMT -5
Gas producer that i made was built using Holset HX35 with inducer diameter 54mm....
It used to work well on gaseous fuel but caused problems while running on diesel....temperatures sky rocketed sometimes much in the excess of 1100 degree celsius....while on gas they remained below 700 degree celsius...
|
|
|
Post by racket on Jun 3, 2014 20:08:02 GMT -5
Hi Madpatty
Gasious fuel has a faster burn rate generally , and can accommodate shortcomings in the flametube design/size , a change to atomised liquid fuel soon shows them up .
What were your flametube dimensions ??
Did you use Jetspecs to design it ??
What fuel pressure are you using ??
What sort of spray nozzle for the fuel ??
Cheers John
|
|
|
Post by madpatty on Jun 3, 2014 20:32:53 GMT -5
Hi Racket,
That was the problem i realized after completing my build...
Because before starting you never know that such small changes can lead to such big problems...
I didn use Jetspecs But it was a sort of "bypass area" design..sorta followed by RCDon....
Flametube is 4" in diameter and 12" long....
I am currently using fuel vapourisation.....
|
|
|
Post by madpatty on Jun 3, 2014 20:34:51 GMT -5
Sometime during the build i thought of using WASTEGATED turbocharger also.... 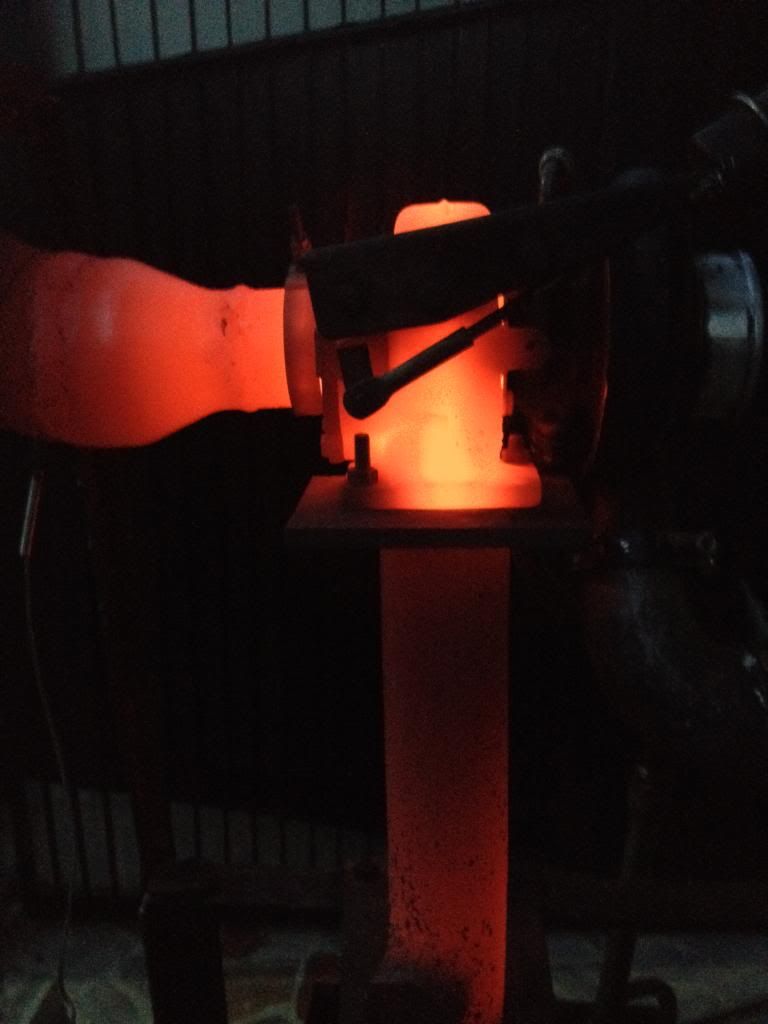 See whats happening on diesel....!!! Cheers Madpatty.
|
|
|
Post by racket on Jun 3, 2014 21:05:07 GMT -5
bad combustion , still burning in the turbine
|
|
|
Post by finiteparts on Jun 4, 2014 0:25:34 GMT -5
The problem with using a bypass area combustor is that you can't be sure that you are getting the correct amount of air into the primary zone for good combustion on liquid fuels...it may just be going around to the bypass area. Gases fuels have very wide flammability limits and thus can forgive many design shortcomings. If you were not getting enough air into the primary zone, because it was going out the bypass area, you might not have enough heat input into your vaporizer to actually vaporize the fuel since the combustion in the primary zone would be very rich. Judging by the picture, the bulk of the combustion heat release is downstream of where I would suspect your bypass area is (at the turbine housing inlet). If the air is getting in there and supporting the combustion there, it would explain the more intense temperatures showing on the turbine housing.
My suggestion is for several things... First I would pull the turbine housing and make sure you didn't burn off the tips of the turbine blades. Second, you might try blocking the bypass area with a welded strip to see if you can get the airflow through the primary holes and get better combustion...but I would really suggest remaking the combustor a bit larger in diameter. From the pictures, it looks like the diameter is too small. I just put up a post explaining why we want combustors as large as possible that you might want to check out.
I didn't mention in that post, that if the combustor suffers from an excessive pressure loss, you will often have to increase the turbine inlet temperature in order to make the power required to run. Often the turbines with small diameter combustors that we see in videos have turbine wheels glowing bright orange, which is likely due to a combination of poor combustion efficiency and severe pressure losses in the cycle. Even a great designed turbo engine is not very efficient to begin with, so when a component has a very low efficiency, it can make things hard to operate.
I hope this helps.
~ Chris
|
|
|
Post by madpatty on Jun 4, 2014 1:40:23 GMT -5
Hi Chris,
Thanks for such a valuable piece of information...
Can you direct me to the post regarding "why we should make combustors as large as possible" you just mentioned...
Cheers Madpatty.
|
|
|
Post by madpatty on Jun 4, 2014 9:59:12 GMT -5
Hi All,
I need some help on choosing the steel pipes for my new combution chamber...
For the flametube i hve found 134.5mm ID and 141.3 mm OD steel pipe...
For the outer combustor can i have found 161.5mm ID steel pipe....
This gives almost 10mm air gap between the flametube and outer can...is that enough??
Are these dimensions good as per the requirement for a 56 mm inducer turbocharger....
Cheers, Madpatty.
|
|
|
Post by madpatty on Jun 4, 2014 20:30:25 GMT -5
Any help will be appreciated....
Cheers, Madpatty
|
|
|
Post by finiteparts on Jun 4, 2014 21:55:45 GMT -5
The post that I am referring to is here: jetandturbineowners.proboards.com/post/8741As for the steel pipes...I tried to find a compressor map for the HX35, with no luck, but I found a similar sized turbo and hopefully it will be similar enough for the initial discussion purposes. So, if we assume you are able to get up near 48 lbm/min at around 3.0 to 1 PR and 0.77 efficiency, then for the annular area that would result between the 161.5 mm and the 141.3 mm pipes, I got roughly a local mach number of 0.19 assuming no losses. If you incorporate some boundary layer flow blockage (roughly 15% range), then the local mach number climbs to 0.22. This is not terrible, but the 134.5 mm tube has your local mach number down to M = 0.17 with the same blockage. So from the perspective of what is best for the annular space between the liner and the casing, the smaller tube would be preferred. Just for clarity, the reason that you want the flow velocity in the annular space around the liner as low as possible is primarily that you want to have the highest possible STATIC pressure difference relative to the space in the combustion liner. Since static pressure drops with flow speed, you need to have the highest area possible to reduce the flow speed. The high static pressure ratio across the liner is desired in order to make sure that the air jets have high penetration into the combustor flow and high turbulence intensity for mixing. Also, the lower the flow speed, the lower the turning losses that are incurred by the air turning into the combustor. So I ran some quick numbers on the pressure loss due to combustion using the smaller tube for the liner and it looks very reasonable since the local mach number is low. I have to go through my worksheet and double check my calculations before I share those numbers because I don't want to give out wrong information. I would suggest that you take a look at the JetSpecs, since there is a history of successful builds done with its help. Otherwise, if you want to design your own combustor, I would suggest get a copy of Arthur Lefebrve's "Gas Turbine Combustion" book and working through some of the design calculations that he lays out. ~ Chris
|
|
|
Post by madpatty on Jun 4, 2014 22:09:37 GMT -5
Thanks Chris,
I didn understand when u said smaller tube will be preferred....??
I wanted a good casing and flametube combination...
JETSPECS suggested 5"ID flametube...and 6-6.5" ID outer casing...
If i go with 5"ID flametube then i cant find suitable diameter outer casing so that annular area is not blocking the flow...
My main question was What if i use 6"ID flametube and 8"ID casing???
Thanks Madpatty.
|
|
|
Post by finiteparts on Jun 4, 2014 23:33:34 GMT -5
Sorry about that! I misread and thought that you had two tube id's available...I missed the "134.5mm ID and 141.3 mm OD steel pipe"...ID and OD terms in that statement....sorry for the confusion.
If you can get a 6" and 8" tube...they would probably work well...but, nothings for certain in the combustion design world!
One of the design variables that combustion designers use is called the "residence time". It is the amount of time that the fuel-air mixture stays in the combustor and has available to complete it's burn out. With a very large diameter combustor, you will have a large residence time and thus a very high probability of having complete combustion prior to it entering the turbine housing. I am not familiar with how Jetspecs determines required combustor length and hole placement, but I would guess that you would need to shorten the length somewhat from it's recommendation since you have a 250% increase in the cross-sectional area from what it recommends.
Another thing to consider is maybe you can find other stuff to make the combustor from. The post previous to the one in the link sent to you above, I showed my first engine and how I made the combustor from a propane bottle that I cut up and the casing was made for truck exhaust pipe. The low pressure ratios of these engines is easily contained by thin sheet...so if you can't find the proper size tube, you might try rolling a sheet and welding it up...or you might even find a stainless steel kitchen container that would work...just a thought.
Is your vaporizer similar to RC Dons?
|
|
|
Post by madpatty on Jun 5, 2014 2:11:11 GMT -5
No, Not like RCDons evap system.
My evap tubes are like the design John used in his "2 shaft kart huild"....
4 separate evaps with an injector for each tube...
|
|