|
Post by madpatty on May 25, 2015 13:03:48 GMT -5
Video showing the inconsistent ignition:-
Cheers, Patty
|
|
|
Post by Johansson on May 25, 2015 13:25:23 GMT -5
Hi Patty, Nice looking afterburner! I had the same problem with my old jet cart afterburner, it turned out I used a low pressure fuel pump so when the afterburner lit the pressure in the pipe increased and lowered the pressure drop over the injector causing a flame out. A new Bosch EFI fuel pump from a car solved the problem for me as can be seen in the end of the video. Damn, I got a bit nostalgic from watching the video. It was probably 10-11 years ago, back then I got lots of more hair but just as little brains...  Cheers! /Anders
|
|
|
Post by madpatty on May 25, 2015 14:38:30 GMT -5
Hi Johansson, Thanks for sharing that info.
But i am already using a Bosch EFI pump drom a car.... And this is the same pump which i used to get engine P2 at about 20 Psi so hopefully it has got enough juice to overcome afterburner pressure. Has it?
Cheers, Patty
|
|
|
Post by Johansson on May 25, 2015 15:13:48 GMT -5
Hmm, two 1mm nozzles fed from a Bosch EFI pump should pump loads of fuel into the afterburner. Have you measured the flow? To me it looks like it is running lean in the video.
Do you have any way of adjusting the fuel flow during a run?
|
|
|
Post by racket on May 25, 2015 18:32:23 GMT -5
Hi Patty
Heres some flow test numbers from my GT6041 afterburner design phase ..............
The engine will require ~4 litres/min of fuel to the A/B ,................... with 20 spray orifii , thats ~200 cc/hole/min .
A test rig was manufactured using a short "blind ended" length of the same 3/8" OD stainless tubing as the fuel ring is constructed from and a single 0.7mm hole was drilled in its side , the tubing was then pressed into a fitting that was screwed onto a garden tap .
When water pressure was applied to the test rig it squirted horizontally ~10 feet at the required 200ml/min flow through the 0.7mm oriface , this was much further than expected :-(( ........................but upon application of the leafblower to simulate the gases exiting the turb exducer , the jet of water was reduced to ~2 - 3 inches before it disintergrated into a spray going "backwards .
This was still a considerable axial distance so I opened up the hole to 1.0mm diameter , this increases flow area by about 2 times , so a decision to reduce the number of holes in the A/B sprayer to 16 was made , this would now require a flow of ~250ml/hole/minute , ....................this produced a horizontal jet of ~6 feet when the test rig was fitted to the garden tap .
The leafblower reduced the axial squirt to between 1 and 2 inches ................getting more like it :-)
There was one unfortunate side effect of having a squirt of fuel going axially towards the imaginary turb wheel exducer's gas flow and that was that some of the "fuel/water" was blown straight back onto the spray ring where it flowed around to the downstream side of the tubing and was blown off in large droplets , not the best thing for fast combustion :-(....................
Patty , your engine has an inducer roughly half the diameter of the GT6041 , so only 1/4 the flow area , I considered I needed 16 X 1mm dia holes , this would indicate you'd need ~ 4 X 1 mm holes to flow sufficient fuel if using an EFI pump producing ~60psi of fuel pressure.
The afterburner will consume at least three times the gas producers fuel flow, and depending on A/B fuel burn efficiency it could be more than 4 times, they are extremely thirsty creatures.
Cheers John
|
|
|
Post by madpatty on May 25, 2015 20:30:18 GMT -5
Hi Johansson, Yes i got a PWM controller controlling the fuel flow...
Hi Racket, Is there a possibility if i can modify those two injectors...what if i drill larger than 1 mm holes to get more flow area....say 1.5mm holes.
Another option:- Can the holes be drilled in the same fuel lines(each fuel line with 2 x 1mm holes) or i need two more fuel lines?
How much is the possibility considering the sizes that dump region is not able to anchor the flame at all?
Cheers, Patty
|
|
|
Post by finiteparts on May 25, 2015 22:34:41 GMT -5
Hi Patty,
Nice to see you blazing forward on the afterburner (yes, a pun was intended there! Ha!)
Just curious, is the compressor staying at roughly the same pressure? The reason I ask is because the afterburner will back-pressure the turbine and if the nozzle area is too small you will loose pressure ratio across the turbine...and it seems like the first light off sort of slowly goes out...could that be due to a loss of airflow? The old Century series fighter jets often had trouble with A/B lightoffs. They would punch the A/B, it would ignite and a pressure wave would travel back to the compressor and cause it to surge. Not exactly what the pilot was hoping for in the middle of combat!
Second, if the engine is running fine during the A/B light offs, how far into the stream are the injection holes? You could try moving them more toward the outer wall to help the capture rate of the dump diffuser/flameholder region. The capture rate of the fuel droplets is probably pretty poor for that style stabilizer and you could easily be blowing the vaporizing droplets straight out the back. Remember that in order to burn, the droplet must first evaporate. The combustion occurs with the gaseous state of the fuel not the liquid state. Larger droplets take longer to vaporize and the volume of a sphere goes up as the radius cubed, so more smaller holes are preferred.
If you have any streaks or anything in the exhaust pipe to show you which way the flow was swirling (I am assuming that the exhaust flow out of the turbine probably has some residual swirl left in it), you could try to turn the injector to allow the fuel jet to flow across the exhaust flow. This might help shear the droplets into smaller sizes, allowing for quicker droplet vaporization.
You could try to spray on the outer wall and let the fuel film break around the 90 degree lip at the dump section. This is sort of like what they do in pre-filming airblast nozzles...but the benefit to you is that the fuel may vaporize off the heat of the wall, then flow near the wall surface and get entrained into the recirculation zone easier. The down side is that you might experience fuel coaking on the walls if the liquid fuel temps rise too quickly. I wouldn't point those upstream...I would shoot them 90 degrees from the injector to the wall.
Finally, I think you have enough fuel for the moment. I wouldn't try to increase the flow, because you have shown that you have enough to hold a flame...so you are not too lean...you could be a bit rich because the flame looks pretty ragged due to liquid droplets still burning outside the nozzle, but that could be a function of a poor capture rate in the flameholder. Remember, the goal is to raise the gas temperature before you leave the nozzle. Any burning outside the nozzle is just a means of wasting fuel to create a wow-factor...it does nothing for your thrust.
Good luck!
Chris
|
|
|
Post by madpatty on May 25, 2015 22:42:34 GMT -5
Hi Chris, The fuel holes are in say, 30% and 70% along the diameter of the pipe.(i guess it makes sense)
But fortunately i got fuel lines that can turn 360degrees(designed that way) so i can tilt the fuel holes towards the wall rather than spraying them towards turbines so that fuel spray is more towards the wall rather than turbine.
Or i should tilt them 90 degrees entirely towards the wall perpendicular to the turbine axis.?
Cheers, Patty
|
|
|
Post by madpatty on May 25, 2015 22:54:16 GMT -5
Hi Chris, The compressor pressure was too low when the afterburner was able to be ignited that any change in pressure was negligible.... The afterburner was able to ignited only at barely self-sustain point 3 Psi P2 and when as soon as i opened the throttled, the flame got blown out.
As far as lightoff is concerned i dont think it was due to loss of airflow because afterburner was sort of loving less airflow(airspeed) to get ignited and lit off as soon as throttle level was increased.
Cheers, Patty
|
|
|
Post by finiteparts on May 25, 2015 23:04:54 GMT -5
I would say the first thing I would try it leave them pointing towards the turbine, but bring them out to around 80 and 90% of the tube diameter.
My guess is that the fuel being injected at the 30% diameter location is not getting trapped in the flameholder at all...it is going straight out the back end. As for the 70%, the residual swirl may be carrying it outward toward the wall so that it gets pulled into the flameholder region, maybe. That toroidal vortex that forms in the dump region should be pretty strong, so if you get the fuel there, it should hold a stable flame.
Turning the fuel injectors will do exactly what I was referring to. You might even try to turn them at various angles to see the effect, of course after you've tried moving the fuel holes up. Don't try to move the fuel holes and turn the injectors at one time...if you did, you will not know what is happening and if something helps which one it was.
Good luck,
~ Chris
|
|
|
Post by finiteparts on May 25, 2015 23:10:23 GMT -5
Ok then, that sounds like you have a flame anchoring problem. You need to get the fuel to the flameholding region...so I think moving the injection holes closer to the outer diameter will give you a better chance of getting the fuel into the dump section. I think the filming idea might also work pretty good...
Good luck!
Chris
|
|
|
Post by Johansson on May 26, 2015 1:53:24 GMT -5
On our old jet kick we had two 1mm injectors fitted just downstream the turbine at a 90 degree angle to the flow, they were positioned in a tangential fashion so the jet of fuel would rotate clockwise around the duct wall to get the best "hang time" before reaching the recirculation zone.
On our new afterburner we have a three legged flame holder made from high temp stainless tubing cut in half, this is a definitive improvement since it produce enough restriction in the pipe to keep a stable flame front directly downstream the injectors. The flame holder also acts as a glow plug to further decrease the risk of a flame out.
Cheers! /Anders
|
|
|
Post by madpatty on May 26, 2015 8:45:47 GMT -5
Hi Guys, A good news to report. Afterburner ran nicely at full power. finitepartsi rotated the angle of fuel delivery holes because that was the easiest modification i could do as it only needed loosening and re-tightening of few adapter joints. I aligned them pointing towards the outer walls of the afterburner almost perpendicular to the turbine axis. AND 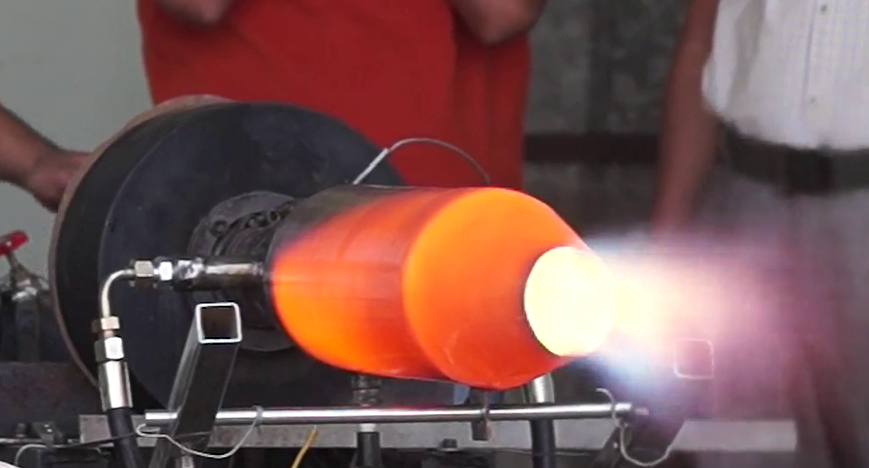 Cheers, Patty
|
|
|
Post by madpatty on May 26, 2015 8:46:24 GMT -5
The Video:-
Cheers, Patty
|
|
|
Post by finiteparts on May 26, 2015 9:42:23 GMT -5
Hi Patty,
That's looking good. The flame is nice and translucent which means you are getting the majority of the combustion to complete in the A/B duct before it exits the nozzle. That ragged, nasty yellow flame you had in the previous video is what it looks like when the fuel is still burning as it is coming out of the nozzle. The carbon in the flame (break the hydrogen to carbon bonds and form carbon particles which we call soot) causes that yellow flame. The carbon particles glow yellow in the flame and make it so that you can't see through the flame. It is an indication that you have incomplete combustion. But your translucent flame is just what you want to see.
Your light off was a bit slow. You might try to run the engine for a bit longer before trying to light the A/B...it may give the parts a bit more time to heat up and aid in ignition. Are you running kerosene, diesel? Another thing that you might try to help your light-off is to make a JP-3-like fuel...JP-3 is a mix of kerosene, aviation gasoline and diesel. The addition of the gasoline raises the vapor pressure and makes it more volatile, lowering its boiling point. I would start off small with only a 10% or so mix of gas in the kerosene or diesel (you don't have to add kerosene to the diesel if you are just running diesel, or vice versa)...then move up from there.
The other thing that might help is the spark energy. The required amount of spark energy increases as the gas flow speed increases, so if you can find a more powerful ignition source it might help on the relight. Where is the spark plug located? It should be really close to the dump plane...probably right in the flame holding region.
Good luck!
Chris
|
|