miuge
Veteran Member
 
Joined: March 2014
Posts: 200
|
Post by miuge on Jun 25, 2015 12:09:49 GMT -5
Just wondering if the oil pressure/return "block" could cause lack of air at inner wall holes, blueing seems to be at about the same area?
|
|
|
Post by madpatty on Jun 25, 2015 12:14:37 GMT -5
Hi Miuge, Even i thought the same but the hotspot and blueing is only near the oil inlet. The oil outlet side is totally clear.
If that was the case then the blueing would hv occured on both diametrically opposite sides.
Cheers, Patty
|
|
|
Post by racket on Jun 25, 2015 17:56:11 GMT -5
Hi Patty
A fuel ring with the injectors flowing within plus/minus 5% of the average should mean that there won't be any hot segments to burn your NGV .
When I was building my first "micro" type engine, the FM-1 , I setup the fuel ring with plastic tubing on each injector running to 15 identical glass measuring cylinders ( old coffee jars) so that I could easily test the flow consistency at varying delivery pressures .
Cheers John
|
|
|
Post by racket on Jun 25, 2015 19:16:22 GMT -5
Hi Patty
There was one other thing I noticed , there appears to be be a couple of circular coloured areas on the front wall which look like they've been "blow torched" by a flame exiting the evaporators , the mixture of fuel and air exiting the evaporator should be too rich to ignite , unless the injector isn't flowing its correct amount of fuel , the underfuelling creating a combustable mixture , this might account for your burnt evap outlets .
Cheers John
|
|
|
Post by madpatty on Jun 25, 2015 19:25:38 GMT -5
Hi Racket, So that accounts for lesser flowing injectors where there are hot spots on the front wall....am i right? I will check them.
So is there anything else i should try/change or just the new fuel ring and test the engine on diesel.
Cheers, Patty
|
|
|
Post by racket on Jun 25, 2015 22:00:00 GMT -5
Hi Patty
A new fuel ring thats been tested and flows verified , without that theres no point changing the flametube holes etc etc .
You will need to flow test at the rate your engine will burn fuel at , ~0.5 lbs of diesel per minute , ~280 ml/min or ~17 ml/min/injector .
Cheers John
|
|
|
Post by madpatty on Jun 26, 2015 11:23:46 GMT -5
Hi Racket, Today i did a test run using diesel.
Same hotspot and this time exagerated than before...i can see small red flames coming from the same 1'o clock spot.
I have got no clue why combustion is exiting the combistor at that very spot... What if at that area there is lack of air supply to the inner flametube.?
The turbine exducer shroud only gets hot at that spot. But combustor showed a more consistent pattern....
More areas were purple this time.
But i am now concerned about that hotspot. Fuel injectors were tested for consistent flow.
Cheers, Patty
|
|
|
Post by madpatty on Jun 26, 2015 12:58:38 GMT -5
Here is the hotspot:- 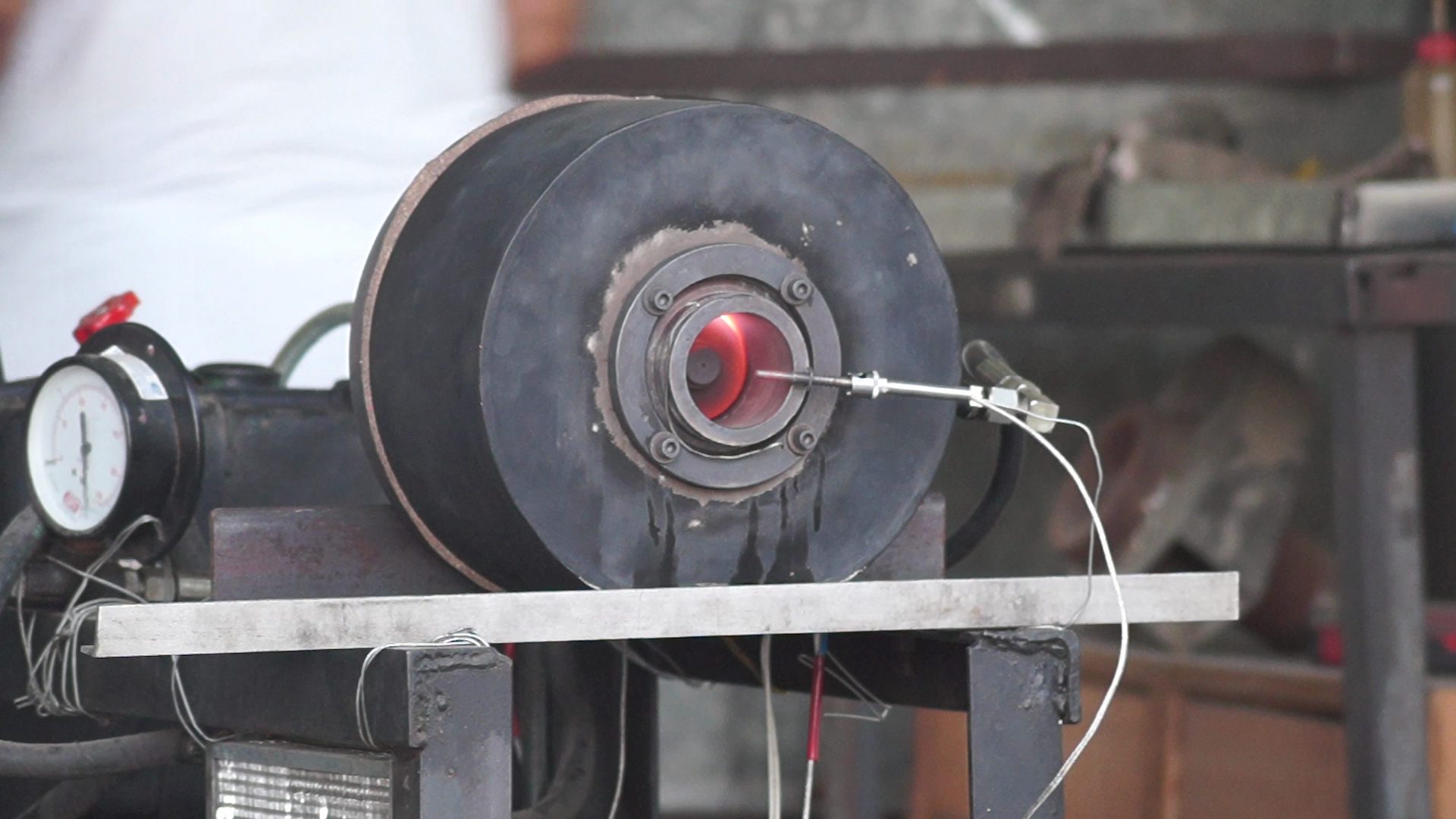
|
|
|
Post by racket on Jun 26, 2015 18:32:55 GMT -5
Hi Patty
If the fuel injectors flowed at plus or minus 5% of average, at the flow I suggested in my last email, and the fuel is injected onto the inner wall of the evaporators ,then there must be an aberrant airflow issue, all other things being equal .
You'll need to add more dilution air at the hot spot , though looking at your earlier pics of the outer wall it appears as though combustion is delayed a bit in that segment of the FT , perhaps you may need extra primary air to speed up combustion rather than it waiting until some secondary air is added , its difficult to say as I can't see the orientation of all the components at the same time just from 2 dimensional pics .
Just looking at the heat pattern on the outer wall it appears as though theres too much fuel for the available air until the secondary air enters , but if the injectors are flowing equally then its got to be aberrant air distribution and the only way to cool the hot spot is extra dilution air.
As a first thing to try , I'd add 3 extra Primary holes on the outer wall, between the evaporators, at the "hot spot" segment where it appears that combustion is delayed, have them on the same axial line as the rest of the Primary holes , the extra air may speed up combustion in that area reducing the chance of flames getting to the NGV .
If this doesn't displace the combustion further forward into the flametube you may have to increase your main dilution hole area at the hot spot , but try one thing at a time .
Cheers John
|
|
|
Post by madpatty on Jun 26, 2015 20:31:16 GMT -5
Hi Racket, So as to keep the uniformity of the hole pattern can we be just increase the diameter of some holes rather than increasing the number.... Or increasing the number is more effective?
And if the number is to be increased then one hole between three respective primary holes(i.e three total holes to be added) in the hotspot section of the outer flametube...?
Cheers, Patty
|
|
|
Post by racket on Jun 26, 2015 21:29:10 GMT -5
Hi Patty
Add 3 holes the same diameter as the other primary holes , positioned between the primary holes in the primary zone , in the segment thats experiencing the hot spot
Cheers John
|
|
|
Post by madpatty on Jun 27, 2015 19:52:54 GMT -5
Hi Racket, I ran the engine yesterday on gas after adding extra prinary holes... There was clearly no more hotspot just a consistent reddish line all across the periphery.
It appears as if i need some more holes in the primary region because the temperatures are a bit on higher side with this combustor as compared to the old one though that one wasnt good for diesel. What do u say?
Cheers, Patty
|
|
|
Post by racket on Jun 27, 2015 21:17:16 GMT -5
Hi Patty
Temperatures have "nothing" to do with holes, temperatures are caused by backpressure and component efficiencies along with ambiant conditions .
If you have a consistent "acceptable" colour around your turbine, then thats all you can hope for , the holes sizes/areas should be adequate , but not being able to physically handle your engine components and make observations limits any suggestions I can make .
Just how much hotter are your temperatures with this FT compared to the old FT ?
Unless you also measure thrust , jetpipe pressure , ambiant temp/pressure , fuel pressure and P2 pressure at your "elevated" temperature and compare them with your previous data its impossible to know whats actually happening , the increased temps could be caused by increased backpressure but at the added bonus of extra thrust .............without data you're "flying blind" .
Cheers John
|
|
|
Post by madpatty on Jun 27, 2015 21:34:45 GMT -5
Hi Racket, With all the components same and nothing extra added to create excess backpressure...
At the same P2, same ambient conditions i dont expect the temperatures to increase by 100 degrees.
Earlier the temperatures used to be around 530-550 degrees but now they were around 650 degrees at 20 psi P2.
Cheers, Patty
|
|
|
Post by racket on Jun 27, 2015 22:40:08 GMT -5
Hi Patty
NO , they aren't the same components , you now have a fuel ring with equal flows and an equal temp going into your NGV and out through the exducer , this could now be producing a higher fuelflow/temp over the segment of exhaust you are measuring temps at, thats why I like to have two thermocouples situated diametrically opposed in the jetpipe so that if there is some variations I've got more chance of observing it. .
If temps are too high , open up the jet nozzle a millimetre or so to reduce back pressure , you've got to remember your comp wheel is still "too big" for the turbine, its not an ideal match so temps will be higher than if they were .
Cheers John
|
|