|
Post by astilwell611 on Oct 27, 2014 20:52:44 GMT -5
Hello all, I've recently become interested in turbojets and decided to build one. I did a lot of research over the internet and used jet specs to design my cc and flametube.My engine is running off of propane and uses a 1/8" hose barb as the injector. The hose barb is crushed at the end so that it will hold pressure.I am having problems getting a consistent ignition. At first it would just blow gas into the cc for a while and blow out a fireball. I fixed this by adding a "diffuser" over the hose barb to direct the propane towards the spark plug. This helped ignition but it still isn't very reliable. Sometimes it will start right up and others it wont start at all. Any suggestions on how to make ignition more reliable? Maybe the injector is the problem, any suggestions for a different injector design? I uploaded all the pictures of my setup that I have at this time to try to help you guys out. I also added a video of it "running" using a shop vac, please excuse me I was excited lol. I'll try to answer any questions the best that I can.  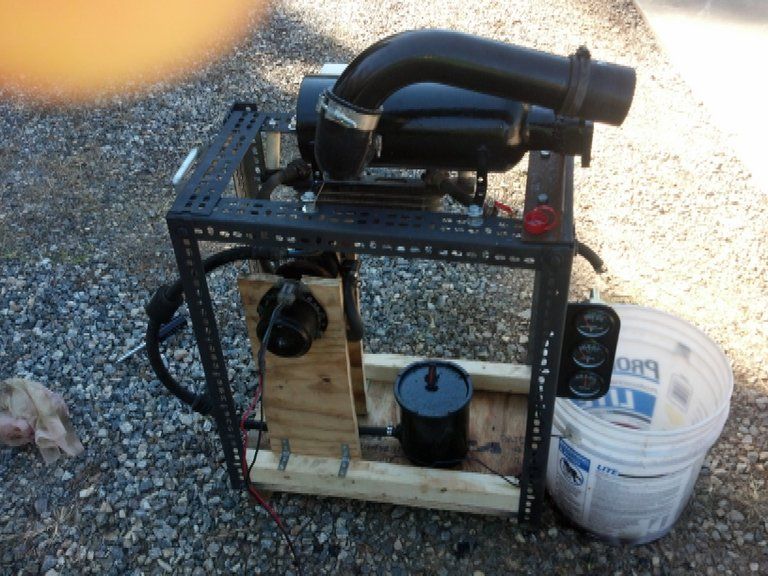 vid1309.photobucket.com/albums/s625/astilwell611/2014-10-26_02-11-05_787_zpsuoo0zr0j.mp4
|
|
|
Post by racket on Oct 27, 2014 21:30:19 GMT -5
Hi
Your propane injector needs to "spray" radially within the flametube , an "axial" injector will have problems .
The simplest method is to have a tube for the injector , seal the end of it and drill 6 small holes around the tube wall ( ~60 degrees apart) , this will spray the propane out over the flametube cross section .
Cheers John
|
|
|
Post by astilwell611 on Oct 28, 2014 10:54:10 GMT -5
Hello John, I assumed that the injector was the problem so what sized holes need to be drilled and can you elaborate on what you mean by 60 degrees apart? Does that mean to stagger the holes? Do you know of any post on here that show a good example? My idea is to use one of these, cap the end and drill holes in it. What are you comments on length from the spark plug? In theory closer is better right?  Thanks Austin
|
|
|
Post by madpatty on Oct 28, 2014 11:39:29 GMT -5
Hi Austin, 6 holes should be placed all around the injector tube....60 degrees apart means- 6 holes equally placed in a circle all around the circumference of the injector tube...
Ideally the injector openings should be at same axial distance as the primary holes(that is discharging just infront of the primary holes).
It appears you are using a brass fitting for the injector....i personally dont like anything except stainless steel in the hot combustion area... For the injector i just used a 3/8" ID stainless tube with one end welded shut....i then drilled 3x 0.7 mm holes equally spaced around in that tube...
Cheers, Patty
|
|
|
Post by racket on Oct 28, 2014 15:25:37 GMT -5
Hi Austin
You could use that as your injector , but be very careful that things can't "unscrew" and go through the turbine wheel .
As long as the propane spray discharges into the vicinity of the spark plug it should ignite
You'll need 6 injection holes , make them as small as you can so that theres a decent injection velocity , 1/32"- 0.8mm diameter holes preferable , but if you need to go to 1/16" - 1.6mm , thats OK .
Patty ,........... remember you had problems with only 3 holes as the fuel spray didn't effectively cover the flametube's cross sectional area.
Cheers John
|
|
|
Post by astilwell611 on Oct 29, 2014 12:06:49 GMT -5
Hello everyone
Thank you guys for you input. I went to lowes last night and picked up a brass cap that is six sided. I plan to take advantage of the drill press at work today and drill a hole in each side. Patty, I havent had any problems with the brass fittings with the few test runs I have got to work. So I'm not too worried about them. John, I use thread sealant on all the fitting joints and make sure their tight. I have a good amount of experience with turbos so I know how fragile the turbine blades are and such.
Austin
|
|
|
Post by Johansson on Oct 29, 2014 17:56:35 GMT -5
Welcome Austin to the forum!  Thread sealant won´t survive the heat after shutdown, make sure to lock it by some mechanical means. Cheers! /Anders
|
|
|
Post by astilwell611 on Nov 10, 2014 0:47:37 GMT -5
Hello all, Sorry for the slow updates but being in college I don't get a ton of free time to work on the gt engine. However, I did manage to make it home this weekend to do some tinkering. I changed out my injector with better results but lighting the actual flame still proved difficult. I decided the culprit was my bbq ignitor. So after a trip to the autoparts store I built a hv circuit using an ignition coil, auto relay, and a capacitor. This lead to reliable ignition of the propane with every attempt. So I decided to bolt the turbo on and give it a shot. The turbo deffinatly spools up much more than last time. I still cannot get it to self sustain, after removing the shop vac the turbo slowly spools down. I do not have any pressure or temp gauges yet but, plan to order some this week. Which should I look at measuring first? Should I look more at the pressure inside the combustion chamber or boost pressure from the turbo? I will attach some videos and pics of my most recent progress. Thanks Austin My new injector is very similar to 8MadDog8's my spark plug is closer to the injector though.  Here is a video of the flame charactaristics with the new injector. Its less orange than the video makes it out to be but there is still some orange to the flame. vid1309.photobucket.com/albums/s625/astilwell611/photobucket-19821-1415597551110_zpsd1e435ef.mp4This is a video of the spool down I was talking about. The fuel pressure stays steady at 80ish psi. vid1309.photobucket.com/albums/s625/astilwell611/photobucket-14014-1415597506255_zpscfa54983.mp4There was a nice bit of soot on the turbo when I removed it at the end of the day. 
|
|
|
Post by enginewhisperer on Nov 10, 2014 1:44:25 GMT -5
that turbo appears to have an integral recirculation (blow off) valve in the compressor cover. (the pressed metal cover with 3 bolts holding it onto the compressor housing)
You'll need to block it off or lock the valve closed (connecting the vacuum line port directly to the compressor outlet pressure should work)
|
|
|
Post by astilwell611 on Nov 10, 2014 14:59:16 GMT -5
enginewhisperer,
It just so happens that I have a block off plate for the turbo I wasn't sure if the recirc. valve would cause any problems or not. Just out of curiosity why does it need to be blocked off? does it keep the turbo from reaching maximum boost?
Austin
|
|
|
Post by enginewhisperer on Nov 10, 2014 16:28:41 GMT -5
yep, as soon as you get any real positive pressure in the compressor outlet, the valve will open and circulate the air back into the inlet.
It's there so that on a car, when the throttle closes the air has somewhere to go, instead of stalling the compressor and putting a lot of extra load on the bearings.
|
|
|
Post by astilwell611 on Nov 10, 2014 19:37:47 GMT -5
Yeah I know what its purpose is I just wasn't sure what effect it would have on the engine. So do you think that the valve was the reason it wouldn't self sustain?
Austin
|
|
|
Post by enginewhisperer on Nov 10, 2014 21:01:52 GMT -5
hard to know, but if the valve was opening then it would definitely stop the engine from self sustaining.
|
|
|
Post by astilwell611 on Nov 17, 2014 13:21:40 GMT -5
Hello all,
Just a quick update, I blocked off the bypass valve with a block off plate. I also added a boost and egt gauge to the engine. However, I just don't think that my shop vac moves enough air to let the turbo overcome itself. I took my gas powered leaf blower into the shop to have it fixed, so hopefully next weekend I'll have enough juice to get it to selfsustain.
Austin
|
|
mitch
Senior Member
 
Joined: August 2014
Posts: 285
|
Post by mitch on Nov 19, 2014 10:15:56 GMT -5
Using a leaf blower is a good idea, to start mine I have to use a large Stihl blower going nearly full throttle to bring it to idle!
|
|