|
Post by racket on Dec 14, 2015 1:03:01 GMT -5
Hi Andrew
That mightn't be a bad idea , I'll still "think kart" with the general overall design of the unit for compactness sake .
First things first though , get the gas producer running .
Finished the exducer shroud and the V band flange that goes around it that mates up onto the NGV stub tube.
Pics tomorrow .
Cheers John
|
|
|
Post by racket on Dec 14, 2015 15:57:14 GMT -5
A few pics of the shroud bits Getting the clearances just right , 7 layers of masking tape , and the use of a wire gauge for the axial inducer tip   Finished article , some minor pit marks , but 99.99% OK , she'll do  Mounting flange  Flange is a "loose" fit on shroud to allow minor alignment changes when parts are welded together when in situ on the engine with suitable packing to provide clearances on exducer .  Flange and shroud fit to NGV , there will be an alignment pin fitted between flange and NGV stub to facilitate repositioning after jetpipe has been removed  Cheers John
|
|
|
Post by enginewhisperer on Dec 14, 2015 16:30:51 GMT -5
Hi Andrew That mightn't be a bad idea , I'll still "think kart" with the general overall design of the unit for compactness sake . Yep, it'd definitely be best to stick to the Kart style design for lightness - but once the engine is done it might be nice to have some flexibility in chassis design to package things nicely 
|
|
Chuks
Senior Member
 
Joined: August 2015
Posts: 498
|
Post by Chuks on Dec 20, 2015 16:25:13 GMT -5
hi John... what is the angle of the fatboy'S NGV
|
|
|
Post by racket on Dec 20, 2015 18:28:42 GMT -5
Hi Skynet
Its the required angle for the design mass flow , temperatures, pressures and pressure drop, this will change from engine to engine , so unless you're building an exact copy of the 12/118 engine the angles will be of no use to you .
As the engine hasn't been fired up yet, I'm not providing much detail as I don't want anyone simply following my mistakes, theres a fair few unknowns with this engine and I'm not 100% sure it'll even work , hence my reluctance to provide much information.
Cheers John
|
|
|
Post by smithy1 on Dec 21, 2015 13:27:54 GMT -5
As the engine hasn't been fired up yet, I'm not providing much detail as I don't want anyone simply following my mistakes, theres a fair few unknowns with this engine and I'm not 100% sure it'll even work , hence my reluctance to provide much information. Cheers John Surely you jest...? I've not seen anything you've built that doesn't at least fire up and run.....and most work well, very well in fact. Smithy.
|
|
|
Post by racket on Dec 21, 2015 17:58:11 GMT -5
Hi Smithy
Yeh , but most have had a reasonable match between comp and turb , this one has that "oversized" inducer , I'm still a little concerned about my wisdom in trying to match it with the TV94 turb wheel, time will tell .
Heh heh , I guess I could always "shim" the front cover and fit a 107mm inducered X846 billet comp wheel I have lying around, if it doesn't ;-)
Cheers John
|
|
|
Post by finiteparts on Dec 22, 2015 14:14:45 GMT -5
Hi John, The engine is coming together nicely and it will be nice to see the final product. In my design, the heat soak back to the bearings is a really problematic thing and thus I am doing a lot of work to minimize the conduction path from the hot gas path to the bearing mounts. I thought that I would discuss some ideas on this with you in case you might want to minimize the heat load on your bearings...particularly the rear bearing. Your engine has the NGV plate in direct contact to the bearing housing with only a small cavity for the oil slinger, I think there is a large heat conduction path that could pump a lot of heat into your bearings, oil and compressor flow. Since aluminum has 12.8 times the thermal conductivity of the stainless steel NGV plate (cast iron is only 3.4 times), you will not be limited in the amount of heat that you can suck out of the hot gas path flow. The NGVs will act like a large finned heatsink and should not have much trouble keeping within a few hundred degrees of the bulk gas temperature. So from the viewpoint of the aluminum bearing housing, the stainless NGV system is essentially a large high temperature reservoir. The bearings, oil and compressor housing will be the low temperature reservoir. The compressor is not a problem unless there is a temperature pick-up before the diffuser throat, conduction to the forward flowpath, etc...but due to the aluminum housings, high velocity and leading edges, there will be a large convective heat transfer and thus this may be an issue...so for simplicity, let's assume this has a marginal impact on compressor efficiency or that we capture that effect in our selection of compressor efficiency. Work done at the University of Hanover's Turbomachinery lab suggests only around a 3-4% compressor hit, but that was with a vaneless diffuser. A vaned diffuser will experience a much larger convective heat transfer and provides a easier conductive heat transfer path the to forward section of the compressor, so the impact to compressor efficiency could be a larger issue for us. In fact, the early automotive compressor housings used to insulate them all over so as to not conduct heat out the inlet struts and reduce compressor efficiencies by 4-5% or more. The biggest loss is the heat transfer out of the turbine module...and pumping that into the oil or compressor is just an annoyance. So, if you look at a standard (non-water) cooled turbo, you see that the bearing housing contains an internal cavity that allows the oil to wash the inner surface. Additionally, by the rear slinger, the cavity is open such that the spray of oil off the slinger is allowed to impact the housing inner surface and pull heat away with it as it drains away (note that in the following picture, the upper cavity is also getting the oil spray and froth washing the surface...the connector above the slinger only covers a small section of the circumference around the rear oil slinger). 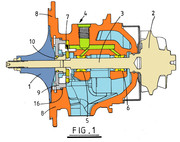 Now, I see that you have something similar to this, but the cavity is sort of small. I also see that you have some cooling holes that will help to reduce the conduction of heat through that wall cross-section. But, I think if you increased the inner diameter of the aft cavity, you would greatly reduce the conduction of heat from the turbine module. The first reason is that you increase the surface area for the oil spray from the slinger to impact and pull heat from. Secondly, you'll reduce the contact area between the NGV plate and the bearing housing with which to conduct the heat. Finally, you get the oil froth away from the rotating shaft and thus reduce the chance to get additional windage losses. Some other ideas...you could use some sort of shim between the bearing housing and the NGV plate that has a very low thermal conductivity to further reduce the heat transfer. Or you could mill away the solid areas between the bolts to further reduce the contact area...leaving a small outer shell that would seal the cavity. Just thought that I would share some ideas and get the creative thoughts stirring. Chris
|
|
ripp
Veteran Member
 
I'm sorry, I don't speak english, so I torment you (and myself) with a translation program,Sorry
Joined: January 2013
Posts: 237
|
Post by ripp on Dec 22, 2015 15:35:55 GMT -5
Hi Chris, the same I wrote already Anders for his JU-01. here a skitze of my turbine S400 which I will eventually build  it is not finished drawing but we can see the oil splash the shaft and the wall and cools it Ralph translate.google.at
|
|
|
Post by racket on Dec 22, 2015 16:08:51 GMT -5
Hi Chris
LOL..............been down all the alternate paths with regards keeping heat from getting to the bearings , the current setup seems to work OK , as always , lotsa compromises mainly caused by the need to be able to actually construct things and provide sufficient flametube between the comp and turb when using the standard shafting .
Theres "blanket cooling" provided over the face of the forward NGV wall , this combined with the cooling holes feeding into the NGV bolt ring cavity and the limited heat path between the bulk of the NGV wall and the actual mounting face from the design of the NGV wall, seems to do the job when helped along by the poor conductivity of stainless.
I'd have liked to provide some sort of heat shielding as in a turbo, but its just not practical .
As theres no great forces placed on the NGV due to the slip joint over the NGV stub , I'm able to reduce the material thickness close to the bearing housing , even the mounting face is only ~6mm thick.
Examination of the shafting after some run times indicates theres no problems , the normal "turbo type" heat transfer appears to be whats happening .
During one of my early FM-1 engine testings the mild steel galvanized lockwire I used on the NGV mounting screws "burnt" , ...............I've learnt a lot since those days :-)
Cheers John
|
|
|
Post by racket on Jan 2, 2016 20:21:05 GMT -5
A bit of an update after the Christmas/New Year festivities . The airflow straighteners have been added to the back of the diffuser wall to guide the air radially to the inner wall of the FT to prevent the "burnout" that occurred with the 10/98 engine. There will be curved "ears" welded to the flametube front wall outer edge to guide air exiting the front of the diffuser down the front of the flametube to prevent it shooting straight past and only feeding the outer wall . A 2 mm thick ring of stainless steel was first mounted to the rear of the diffuser with 6 X 4 mm stainless screws that screw thru the wall into the diffuser vanes . The thin sheet metal stainless radial guide vanes will eventually be spot welded to the ring by the "professionals" , my tack welds are only to hold them in place until then.     Cheers John
|
|
|
Post by Johansson on Jan 3, 2016 3:10:37 GMT -5
Nice vanes John!
Are you going to add a second vane to steer part of the airflow towards the center of the engine? The sheet metal lip I made for the JU-01 welded to the front of the combustor has worked fine for me, no cracked welds or anything.
|
|
|
Post by racket on Jan 3, 2016 15:31:54 GMT -5
Hi Anders
Yep , I'll be welding 13 curved vanes onto the flametube to direct air down the front wall of the FT , the curved vane will be between every second set of axial vanes on the diffuser where the axial lip has been machined away to facilitate the airflow .
Theres ~2-3mm of axial clearance between the front wall of the FT and the radial stainless vanes I've already fitted , this should be enough clearance for any FT axial expansion .
I'm not 100% happy with the current arrangement , but as always its compromises , the FT needs to be shorter in length but our shaft length is limiting the available distance for a decent sized flametube , I might need to machine a bit more metal away .
Cheers John
|
|
|
Post by racket on Jan 3, 2016 21:55:35 GMT -5
Hi Anders
Well , theres been changes :-(
I've had to machine off more of the axial lip on the diffuser wall as it was going to be almost impossible to accurately weld on those 13 curved ears .
I'll be doing something similar what you did with a full circle piece of curved sheet , I'm toying with welding it to the sheet radial vanes so that I can accurately align things and there won't be the worries about expansion changes as there would be if welded onto a 260 mm diameter flametube lip , with a 500 deg C temp rise for the front wall ,the FT expands ~3 mm.
What thickness sheeting did you use for your deflector ring ??
Cheers John
|
|
|
Post by Johansson on Jan 4, 2016 0:06:25 GMT -5
I used 1mm sheet stainless for the ring.
|
|