|
Post by racket on Jan 4, 2016 0:55:21 GMT -5
Thanks , might try something a tad thinner to make it easier to bend over a wooden former .
What sort of radius did you have on the curve , I was thinking ~6mm might be enough now that I'll be taking air from the complete circle of diffuser annular axial outlet rather than only half the "segments, having full annulus and some 15mm axially for the air to turn , the radius on the curve isn't critical .
LOL............if it doesn't look right , I can always make another one :-)
|
|
|
Post by Johansson on Jan 4, 2016 3:10:46 GMT -5
I have no idea about the radius, I just bashed it into shape so it would fit between the FT and diffusor wall. 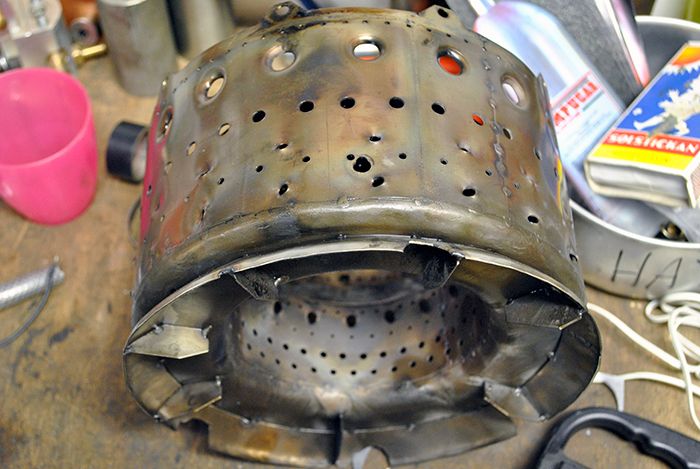
|
|
|
Post by frankenhealey on Jan 6, 2016 8:08:50 GMT -5
I have no idea about the radius, I just bashed it into shape so it would fit between the FT and diffusor wall. 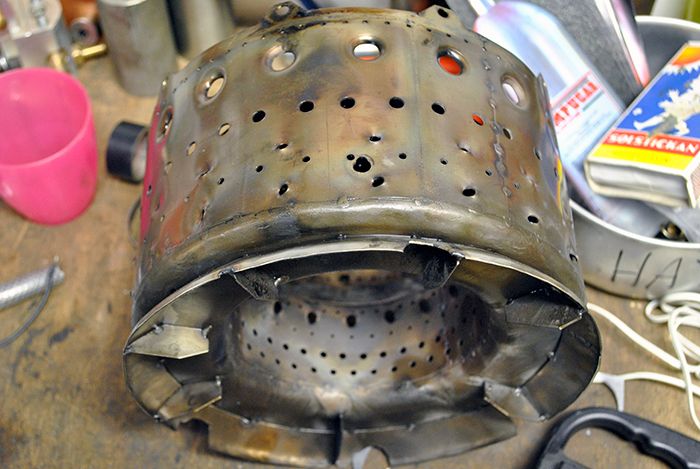 My kind of engineering
|
|
|
Post by racket on Jan 14, 2016 22:20:45 GMT -5
Hi Guys The air deflector is made     Just the outer can to go Cheers John
|
|
|
Post by pitciblackscotland on Jan 14, 2016 22:36:19 GMT -5
Almost there John Cheers, Mark.
|
|
|
Post by racket on Jan 14, 2016 22:43:47 GMT -5
Hi Mark
Yep , I'll get along to the sheet metal guys next week and talk to them about rolling up a bit of 1.6mm stainless sheet to make the outer wall , then I need to make a die for the concave rear end wall that the exhaust stub slipjoint is fitted into , a few weeks work ahead .
Cheers John
|
|
|
Post by Johansson on Jan 15, 2016 3:08:31 GMT -5
Very nice deflector John!
|
|
|
Post by racket on Jan 15, 2016 3:29:31 GMT -5
Hi Anders
LOL, don't look too closely at the welding , that 0.5mm thick sheeting is easy to burn through :-( ..................I need your welding skills.
The finished article appears to be strong enough though , so hopefully it'll do the job .
Cheers John
|
|
|
Post by Johansson on Jan 18, 2016 5:42:19 GMT -5
0.5mm? Is there any reason to go that thin? As you say, it is a bitch to weld that thin SS.
|
|
|
Post by racket on Jan 18, 2016 21:40:46 GMT -5
Hi Anders
The only reason for using 0.5mm was it forms easily over a simple to make wooden former/die and it doesn't disturb the airflow like a thicker one would as it "splits" the air at the diffuser outlet .
To make life as easy as possible with the welding I slit the deflector with a 0.5mm Dremil disk and positioned the 0.5mm axial supports through the deflector by ~1.5 - 2 mm then used the TIG to melt that projecting bit of 0.5mm stainless down onto the deflector , no welding filler rod required , some of the welds were OK but a few were crap , probably from my shaky hand :-(
It'll do the job.
Took the compressor cover/diffuser wall to the sheet metal guys to have a suitable outer can wall rolled up and welded for me , I'll have it back on Friday when I can start thinking about making the concave rear wall and slipjoint , slowly slowly its getting there :-)
Cheers John
|
|
|
Post by Johansson on Jan 21, 2016 2:58:56 GMT -5
Hi John, Ok, so 0.5mm SS is easier to form than 1mm? I´ve always assumed it was the other way around, 0.5mm being to flimsy to stay in shape. Proves you learn something new every day!  Slowly slowly you say, I´d say you are making tons of progress! Cheers! /Anders
|
|
|
Post by racket on Jan 21, 2016 19:00:33 GMT -5
Hi Anders
Yep , 0.5mm is very easy to work with , and once it has a rolled edge it stiffens up the article considerably , then being welded to the support vanes makes for a very strong article .
Got the outer can back from the sheet metal guys this morning, its "OK??", but I'll need to give it a good inspection before using it , I would have liked it a bit tighter fit over the front cover , also they cleaned up the outside weld seam to make it look "pretty" , I wished they'ed left it in place and done a better finish/cleanup on the inside where the O'ring is .
Cheers John
|
|
|
Post by smithy1 on Jan 21, 2016 19:44:11 GMT -5
Hi John, Been doing a little thinking about fuel pumps etc....Our "clone" Bosch 044 pumps seem to be able to supply all the pressure & fuel we need at 13.8v as my test results can verify. However....I've been thinking about running two pumps in series, essentially these pumps will run a certain flow at a certain pressure differential across their pumping element. Bare with me...For example the 044 pump can flow say 150L/h @ 70psi outlet pressure with zero psi inlet pressure. My thinking is that the available outlet pressure will increase if the inlet pressure is increased so the differential across the pump is still the same....so the outlet pressure is basically increasing in line with the inlet pressure.
If we supply the second of the pumps with 50psi from the first pump.... should not the outlet pressure from the second pump also increase by ~50psi..?? I'm planning on doing some testing next week to see if I can verify this, need to get a few fittings etc and get it all sorted before I bring it into work.
Might resolve your fuel pressure issue.
Cheers, Smithy.
|
|
|
Post by enginewhisperer on Jan 21, 2016 20:37:37 GMT -5
you might explode the pump body 
|
|
|
Post by racket on Jan 21, 2016 21:21:28 GMT -5
Hi Smithy
Yep , you'll be effectively doubling the power available for the same flow .
Final pressure would be a combination of both pumps, the last pump would have its internal relief valve "preloaded" with the extra pressure from the first pump, effectively increasing its blowoff pressure , whilst the first pump would be helping to "drive" the second pump ..............maybe , don't know ...........I'll be interested in your excellent test result numbers as usual :-)
Cheers John
|
|