|
Post by Johansson on Oct 1, 2017 16:21:02 GMT -5
I ran the engine again today with some assistance from my friends in Svarthålet Racing. 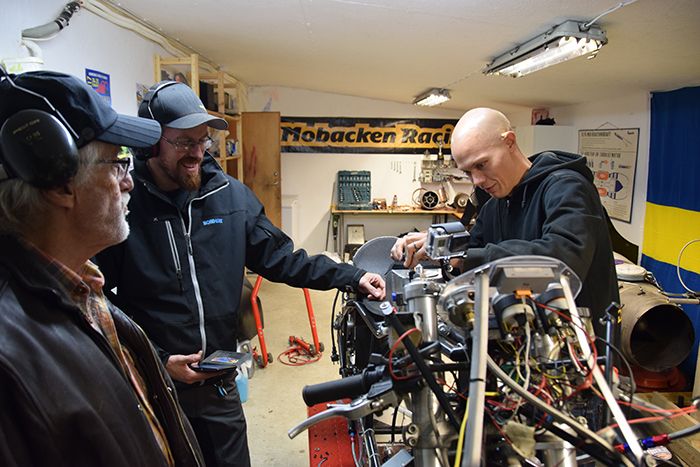 The engine started and ran perfectly until the oil pressure dropped and tripped the pressure switch. Whatta?!?! 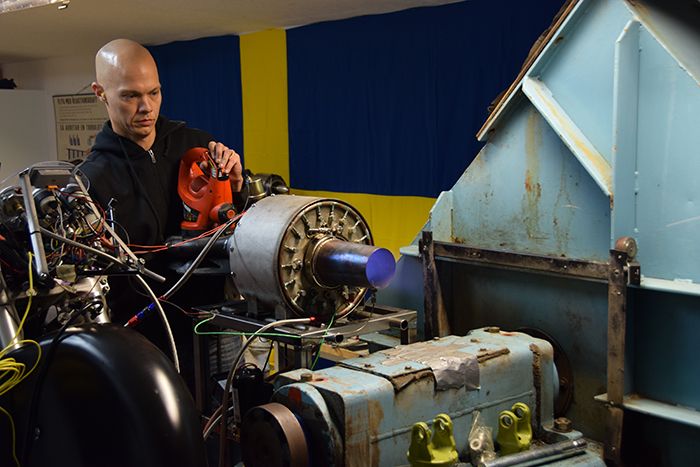 My friends had brought a whole bag of tools so they measured the amperage draw over the battery while I ran the engine, turned out that the combined draw was close to 45A! No wonder that the engine shuts down as soon as the fuel pump starts to run hard around 2 bar P2... 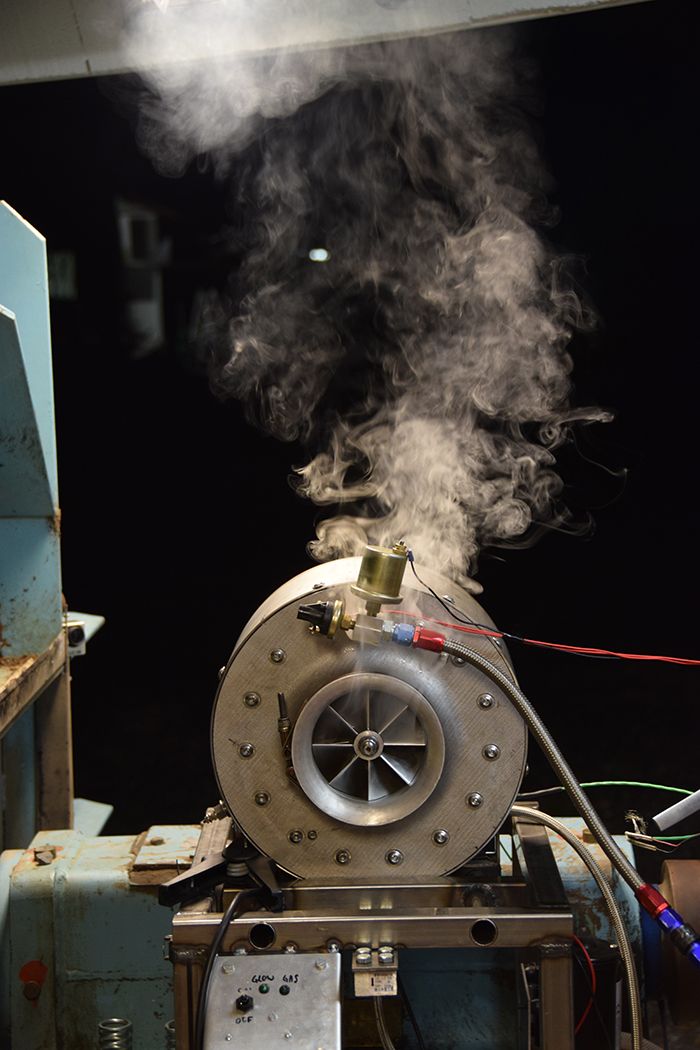 I am thrilled to have found this problem at last, it has haunted me for several years so now I should be able to fix it by rewiring the bike and get me a better battery. Except for this the engine runs incredibly smooth, in this pic the engine is running at 1bar P2 and not a sign of color in the jetpipe! 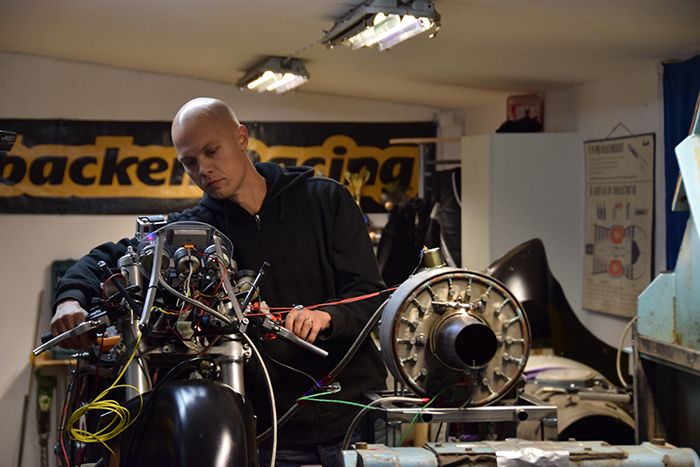 During the last test run the return pump suddenly failed and caused a spray of burning oil out of the exhaust, no harm done except that my workshop rug won´t ever smell the same again...  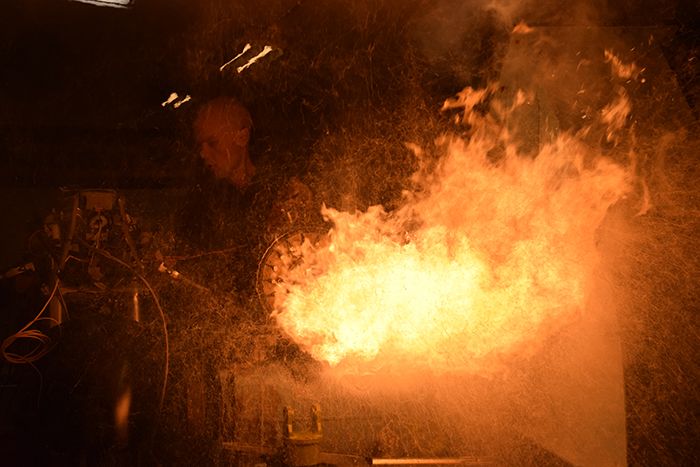 Ooops, I almost forgot the video. Cheers! /Anders
|
|
|
Post by Johansson on Oct 1, 2017 0:37:11 GMT -5
Hi Anders Yep , we'll keep the wheel as standard for as long as we can , I'm thinking further down the track when I know you'll be wanting MORE :-) I understand Chris' concerns about changing the vibration characteristics of the wheel , but you'll be only needing a wheel life of less than 1 hour , not 10,000 hours , so some tradeoffs needed for the extra performance possibilities . Ideally we'll squeeze every last horsepower out of the engine whilst running "standard" , but then we'll need to think "performance" , and as with every engine thats needs to produce extra power , either temps and/or rpm are going to have to increase................heh heh , or you simply add another JU-02 gas producer and fit a 3rd stage Garrett TPE331 freepower wheel to handle the 500+HP Cheers John Hi John, What, do you think I will ever want more power??  Building a twin engine crossed my mind before the idea of the JU-02 was born, but fitting a pair of round engines will be difficult because of their shape so I had in mind to make a twin rotor engine with a common engine casing. The twin engine kick sled worked just fine so I can´t see why a more compact twin wouldn´t work. Cheers! /Anders
|
|
|
Post by Johansson on Sept 30, 2017 15:11:16 GMT -5
Hi Anders LOL.................you're doing all the hard work , the rest of us can only throw in our 2 cents worth here and there to feel we're part of the build process :-) Cheers John I did a quick test this afternoon and got 2 bar oil pressure when circulating the oil back to the tank through the long pressure line, feels like quite a lot so I am moving the pressure transmitter up to the oil entry port on the engine to get a more accurate reading. I should get it done tomorrow and it might even be possible to do a test run tomorrow evening if everything goes as planned.
|
|
|
Post by Johansson on Sept 30, 2017 15:07:30 GMT -5
Thanks a lot Chris for the insight in how the C20 wheel is fastened, I can´t say that I understood it perfectly but you make a very valid point in that I should copy the way it was originally mounted.
I still have the inner wall that needs to be fitted somehow but the main problem will be the outer rim and how to make an air tight but still flexible coupling to the interstage duct and exhaust pipe.
|
|
|
Post by Johansson on Sept 30, 2017 14:59:33 GMT -5
Sorry to hear that you´ve not been feeling well, can´t get much use out of the head when down with a flu...  I would really like to keep the C20 4th stage wheel in its original shape as long as possible, we should still be able to extract some serious power out of it so it feels like something to consider once everything else on the bike is tuned to perfection. I don´t think it would be possible to fit a 2 stage freepower without extending the bike frame, the interstage duct is short as it is with a single freepower turbine. Good to hear that it won´t be needed.  Cheers! /Anders
|
|
|
Post by Johansson on Sept 30, 2017 14:04:28 GMT -5
Really nice work, I love home cast stuff!
|
|
|
Post by Johansson on Sept 29, 2017 14:40:20 GMT -5
We´ll figure something out guys. Have a nice weekend! 
|
|
|
Post by Johansson on Sept 29, 2017 14:34:45 GMT -5
Hi Anders What sort of pressure was required to get that flow ?? The flow rate is certainly more than adequate at 8 lpm ..............what grade of oil are you using ?? My concern is that if you need too much pressure to get an adequate flow from an open ended delivery line , that there won't be much pressure left to "force" oil through those small thrust bearing holes with adequate flow to keep it from failing at the higher air loads on the back of the comp wheel .............LOL, I'm probably only being over cautious as usual :-( Cheers John Hi John, I didn´t have the presence to check the pressure gauge during the flow test, but I´ll do the test again and check it. Judging from the sound of the pump it couldn´t have been very high. Keep the hints and advice coming, I´d rather double check things like this than wreck something out of ignorance.  Cheers! /Anders
|
|
|
Post by Johansson on Sept 28, 2017 14:06:15 GMT -5
That theory sounds perfectly plausible John, the heat makes the vanes expand and close the gap even further and when they cool off they return to this state. That might be why the engine idles at ok temps and after a short while the temp increases.
I have learned from this that I need to design the JU-02 interstage duct so that no stress is transferred into the NGV module.
One thought is that I will mount both the gearbox and gas producer rigidly in the frame and make a sliding coupling where the freepower NGV is. This way the interstage duct can grow and shrink as it wants to during the heat cycles and there won´t be any forces acting on the NGV.
Cheers! /Anders
|
|
|
Post by Johansson on Sept 28, 2017 12:40:43 GMT -5
I test flowed the oil system through the long pressure oil line to see if it would restrict the flow somehow, it took only 7.5s to fill up a liter of 10°C oil so it should work just fine.
|
|
|
Post by Johansson on Sept 27, 2017 16:22:55 GMT -5
I think I got the setup right just now, it was the scaling of the mV signal that was wrong. With a sling over the jetpipe exit it measures pretty accurately up to 35kg which is the max rating for my luggage scale. The 0.23 reading means 23kg, I haven´t figured out how to remove the comma yet but I can live with that. 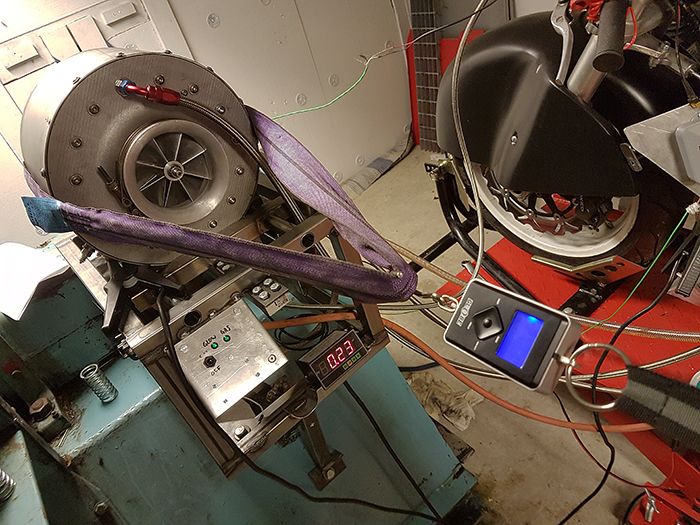 Thanks for the offer Lars-E, later I would really like some help to calibrate the load cell properly so I can trust the numbers. For these initial runs I´ll settle with ball park figures since I don´t know how accurate my cheap luggage scale is that I compared the load cell against. Cheers! /Anders
|
|
|
Post by Johansson on Sept 26, 2017 23:21:35 GMT -5
|
|
|
Post by Johansson on Sept 26, 2017 16:01:56 GMT -5
Compare this to a pic I found from after the first One Mile race, the vanes are much straighter then: 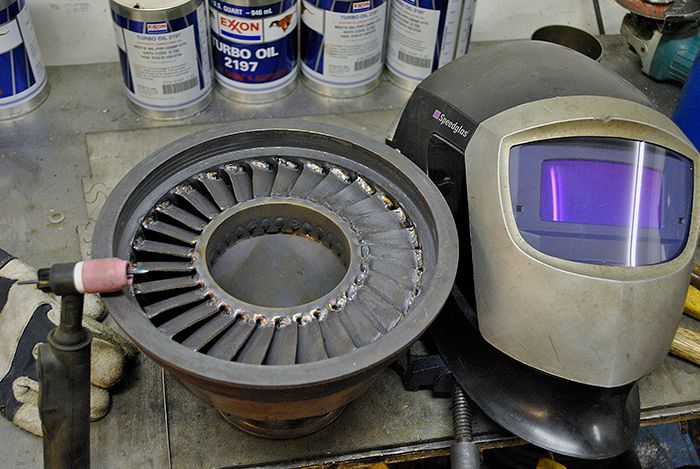
|
|
|
Post by Johansson on Sept 26, 2017 15:44:13 GMT -5
Thanks Chris for your thoughts on this, I´ll take some pics of the wear marks and post them here for further discussion. Anyway, I think I might have found a reason for the high temps. The freepower guide vanes have distorted from the heat and narrowed the bypass area quite a bit. It was difficult to measure but the total NGV bypass area I got was 6090mm2 with a 9240mm2 area on the turbine wheel. 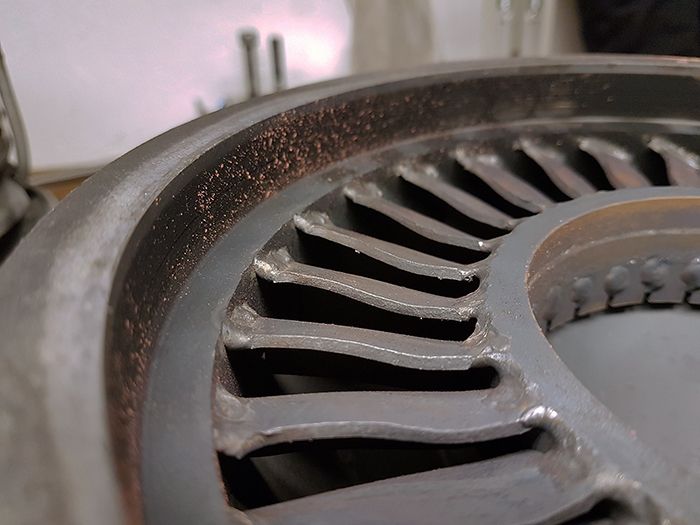 I haven´t dug deep enough into the build thread to find what the original NGV area was, I know I posted it some time during the construction so the numbers are around here somewhere. Cheers! /Anders
|
|
|
Post by Johansson on Sept 26, 2017 15:35:34 GMT -5
Tonight I shortened the oil pressure line as much as possible to get a true pressure reading from the sensor, I also fitted a spark plug boss to the jet pipe so that I won´t need a torch to light off the preheat. 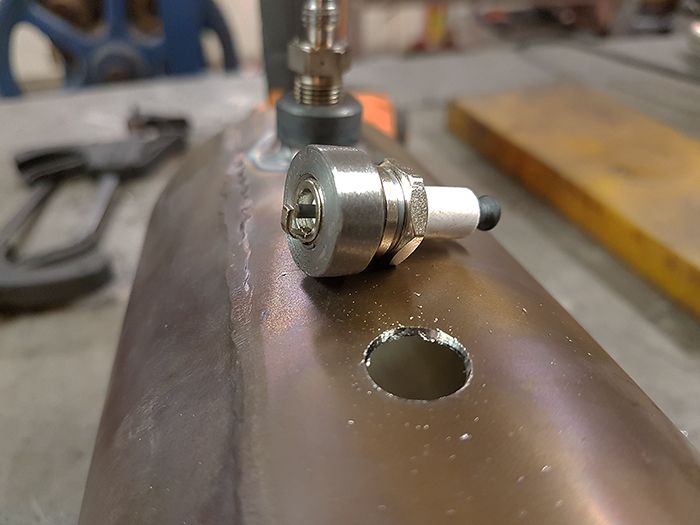 Here it is installed, a few years ago I bought a couple of really small spark plugs from Ebay and one of those fitted perfectly. 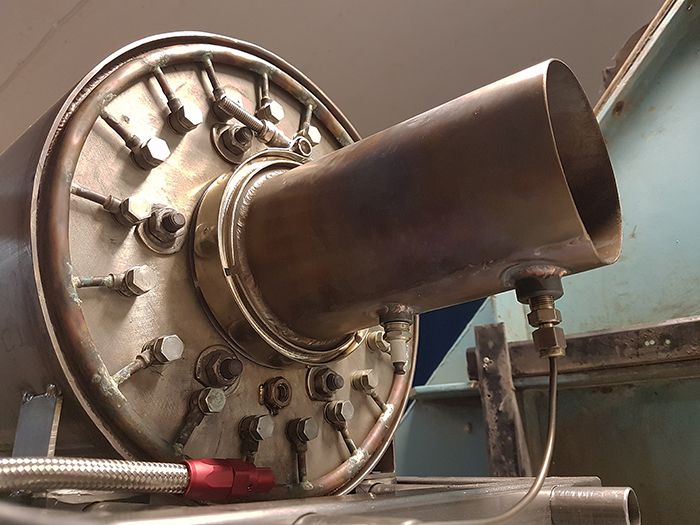 Besides that I connected the P2 gauge and tested the preheat with oil pressure and the leaf blower at full speed, so now the engine is ready for a new test run! I´ll try go fit a strip of reflective tape on the compressor hub so that I can measure RPM with the handheld tacho at different P2 settings, I´ll also give the load cell calibration another try because it would be very valuable to know how much thrust the engine is putting out at different P2´s. Cheers! /Anders
|
|