|
Post by Johansson on Sept 26, 2017 5:05:08 GMT -5
Hi Anders Nice bespoke funnel for the starter, that'll make life easier :-) Just one thing..........with the lubrication pipework being so long now , there could be considerable pressure loss before the lube gets into the engine , and once she's running at a 5:1 PR the poor old thrust bearing is going to need every bit of pressure you can supply it , ............are you measuring your pressure at the pump or at the engine's lube inlet ?? I'll be looking forward to the development programme , and those "numbers" starting to roll in , it'll be interesting to see how well the measured thrust matches the theoretical :-) Cheers John That is a very good question John, I didn´t consider the length of the oil line. The pressure sensor is sitting inside the bike so there is roughly a meter of AN6 hose between it and the engine. Now if I could only get the darn load cell configurated, the manual is poorly translated from chinese I think so I can´t get my head around it. I´ll see if Olov can drop by some day and help me out. /Anders
|
|
|
Post by Johansson on Sept 25, 2017 15:19:55 GMT -5
I have been busy with other stuff lately but now it feels like the JU-02 project has priority again, during the last week or so I have been hooking up the bike to the test stand so now I am very close to having everything ready for a test start. I just have to fit the spark plug to the jet pipe to ignite the preheat propane. (a better location than in the combustor for several reasons IMO) 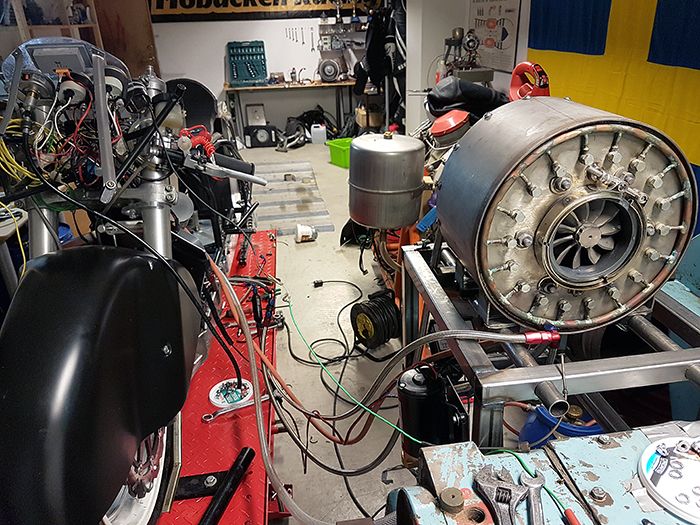 The 3D printer made itself useful again when I printed an exhaust cone for the leaf blower that fits snugly up against the compressor intake. 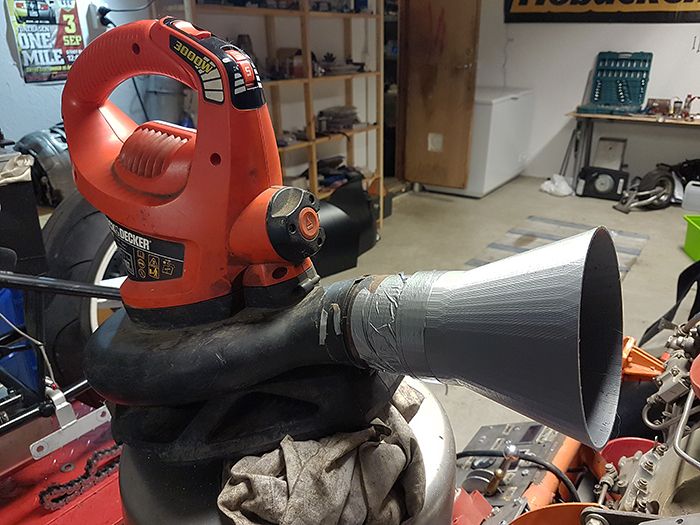 Cheers! /Anders
|
|
|
Post by Johansson on Sept 21, 2017 12:24:58 GMT -5
Hi John,
One thing that talks against the oil/fuel leakage theory is that there is no smoke whatsoever from the exhaust, not at idle and not while running (as far as I can tell from the videos).
No signs of local burning inside the interstage, if by that you mean spots of blued/blackened metal. It all looks the same to me. No cracked and bent interstage vanes either that had blocked off parts of the NGV flow area.
It might perhaps be that the combustor is unable to burn all of the fuel so that streaks of fuel is sent downstream the turbine at high revs?
Cheers! /Anders
|
|
|
Post by Johansson on Sept 19, 2017 8:25:28 GMT -5
Hi John, With JU-01 taken out of the bike I have all the time in the world to investigate the issue while continuing to develop the JU-02 engine, so if you guide me through it and tell me what to measure it is a go.  How much can we rely on the temp readings I´ve been getting when doing performace calculations? I mean, with 1000+C interstage temps the engine would have melted long ago, and despite changing both temp sensors and their locations I have always been getting strange temp readings. I´ll measure the flow areas of the C20 wheel and NGV and get back to you with the numbers. Cheers! /Anders
|
|
|
Post by Johansson on Sept 18, 2017 15:39:47 GMT -5
Hi Anders, I do indeed have a C20B 4th stage wheel at home...it's in pretty good condition too....Also have two 3rd stage wheels, one is the newer split outer ring type...the other is an earlier solid outer ring type, both in good condition....all just cycle expired for aircraft use. I'll bring it into work over the next couple of days and take some pics for you....should be fine for your use. Then we'll organize to get it to you..! Cheers, Smithy. Wohoo! No hurry at all, I´ll be bench running JU-02 all winter so I won´t be needing a spare wheel before next summer if all goes as planned. Well, I hope I won´t ever be needing it but you get my point.  /Anders
|
|
|
Post by Johansson on Sept 18, 2017 14:11:24 GMT -5
Here are some more detailed pics of the freepower NGV, it was difficult to take good pictures but I managed to Photoshop the pics so they sort of represent the truth. 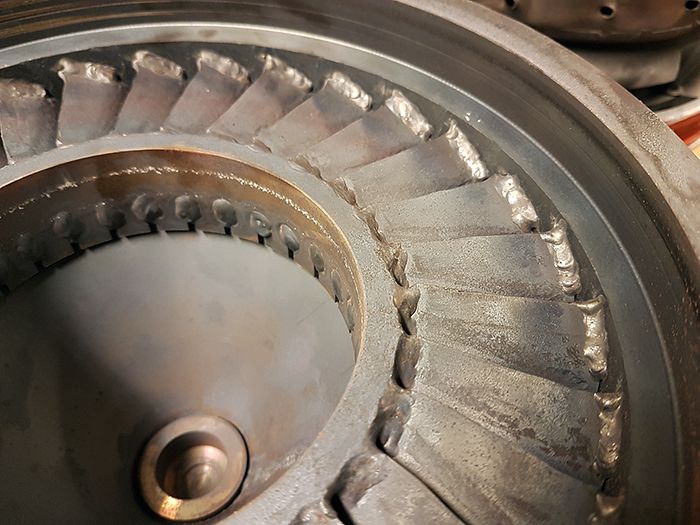 The stainless guide vanes show signs of having been really hot but that isn´t very surprising given how they glowed during the last run. The leading edges aren´t melted and the pittings in the first pics are from the air grinder when I opened up the flow area a couple of years ago. 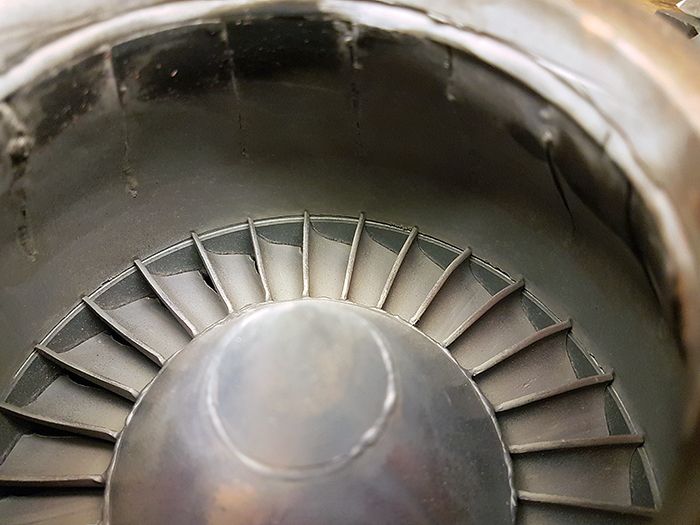 Cheers! /Anders
|
|
|
Post by Johansson on Sept 18, 2017 10:08:35 GMT -5
Hi Anders I have a 3rd stage turbine wheel up for sale on eBay (262946065895), but you can have it for free if you could pay for the shipping Cheers Erik Thanks a lot for the kind offer Erik, but a 3rd stage wheel is no good for my purposes. I need a 4th stage.
|
|
|
Post by Johansson on Sept 18, 2017 4:54:27 GMT -5
Hi Anders Gas producer turbine looks "normal" , so we can be reasonably confident it wasn't being subjected to 1250 C for the T I Ts , so your interstage "reheat" is looking a likely culprit , but is it fuel , oil , or a combination . You mentioned before that you're only able to get a ~2.4 Bar P2 before running out of fuel pressure , do you have any flow measurements for your system to check if its fuel pump or that a proportion of the fuel isn't being burnt in the flametube but possibly downstream . As the gas velocity into, through and out of the wheel is too high for combustion to take place , it would need a "quiet spot" to provide a "flame holder" , this could be where the gases detach from the ID of the interstage outer duct work due to the relatively steep expansion angle required to go from exducer dia to freepower diameter over a short axial distance , if the thermocouple was positioned near such a spot it could account for the high temps ...............are there any witness marks inside the interstage duct that might indicate something like this happening ?? If we assume your gas producer is running at normal temps and you have a TOT of say 700 C then theres going to be a need for a fair bit of "fuel??" to get those temps up to the ~1,100 C being measured, we'd be needing roughly half as much as whats going into the flametube to get our normal operating temps ...............we'd be looking at possibly 1 lpm of "fuel" .............how is the "fuel level" in your oil tank?? LOL, yep , the freepower laby seal looks a tad worse for wear , they "crack" the seal in several places during manufacture on some wheels to relieve those stresses..............Andrew had similar experience with the 3rd stage wheel in the TV84 bike ..................it mightn't hurt to think about slitting the laby seal on your replacement, possibly every 5 or 6 blades to provide stress relief whilst still maintaining rigidity for the blades . Cheers John Hi John, I will do a closer check of the interstage section tonight and take some pics of the internals, I won´t do any more thorough investigations though since the engine is bound for retirement and I want to get busy on JU-02 as soon as possible. One thing that I will improve before I fit JU-02 to the bike is to make the oil return line much larger in area, it might be causing back pressure for the scavenge pump and wear it out. Hmm, cutting the turbine wheel feels like risky business although I understand the idea behind it. I hope that the new one will survive anyway if the temps are kept in check. Anders, I'm pretty sure have C20B 3rd & 4th stage wheels at home...let me check at home first before I commit to sending you one..! And yes, the very first 3rd stage wheels were split at the factory to help avoid cracking issues, then about mid-way through the engine's life they made them solid but had hub cracking issues, now they are all split again...but in a different way, the 4th stage wheels never were split, although there's a new revision 4th stage wheel being released very soon, so we'll soon find out. If split at the factory, the 3rd stage wheels must be split on the outer labby seal all the way through the outer ring between the blades and not overlapping to the end of a blade, if not the result can be a bit ordinary..! Also, there's an N2 rpm range where Rolls-Royce warn against as it will produce harmonic vibrations possibly causing hub and blade fatigue cracking etc...Do you know rpm you are running your N2 system Anders?? Rolls-Royce have a CEB (Commercial Engine Bulletin #1400) which states, (depending on the 3rd & 4th wheel part numbers), the "N2 RPM Avoidance Range" of 71%-88% N2 where 33,290rpm is 100%...so steady state rpm's from 23,636 to 29,040 should essentially be avoided, transitions through this rpm range should be as short as practical. Basically the wheels have less chance of issues if run at their maximum designed rpm of ~33k rpm. Smithy. Hi Smithy, I´m very interested in purchasing a wheel in case you have one for sale! With the bike geared for 340km/h I have been running in that RPM zone for almost half a mile, I have deliberately geared the bike tall to keep the gearbox revs down but perhaps it is better to just have a 10km/h margin to the expected top speed? I´ll gain some HP as well if I increase the freepower RPM so all for the better as long as the gearbox can cope with it.
|
|
|
Post by Johansson on Sept 17, 2017 16:16:33 GMT -5
I wonder if the heat downstream the JU-01 could have been caused by a scavenge pump failure? This would explain why the gas producer turbine looks ok while the power turbine wheel was running while glowing hot.
It has happened to me once before, the old scavenge pump started losing power for some reason and this caused oil to start coming out through the turbine shaft seal and slowly filling up the engine. The soot marks indicate that there has been oil leaking from the turbine seal, and if this oil caught fire in the interstage duct while running it would have heated up the C20 wheel really fast.
/Anders
|
|
|
Post by Johansson on Sept 17, 2017 15:50:48 GMT -5
Tonight I undressed the bike to remove the engine and check it for wear. 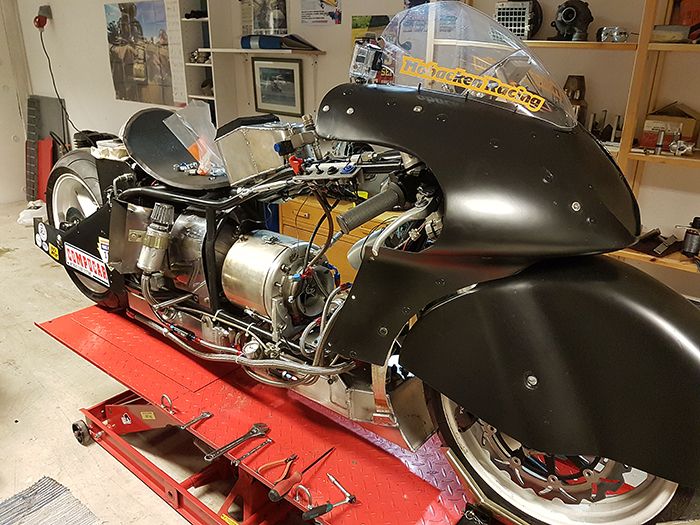 I assumed the gas producer turbine would look like the Fukushima reactor core but to my surprise I couldn´t find any evidence of overheating, mostly it was soot that seems to have come from oil leaking past the rear seal. 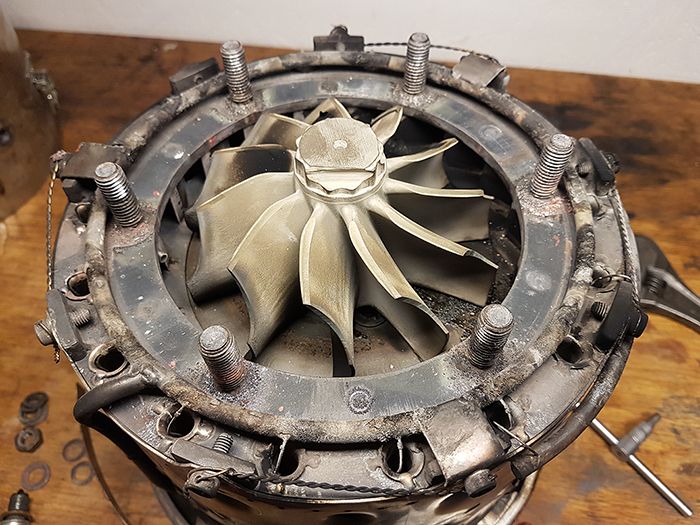 Sharp turbine inducer tips, not what I expected to find!  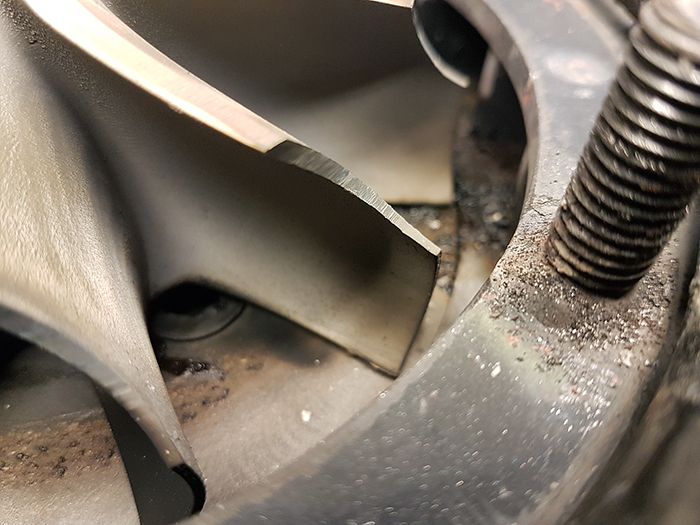 The C20 power turbine was in a sorrier state though, one large crack and a couple of hairline cracks through the outer rim. Wear marks on the radial seals tells me that this must have happened while the bike was running and not while cooling down after the last run. No signs of cracks in the hub section which is a relief, lets just say that the turbine wheel stress relieved itself at 25.000rpm...  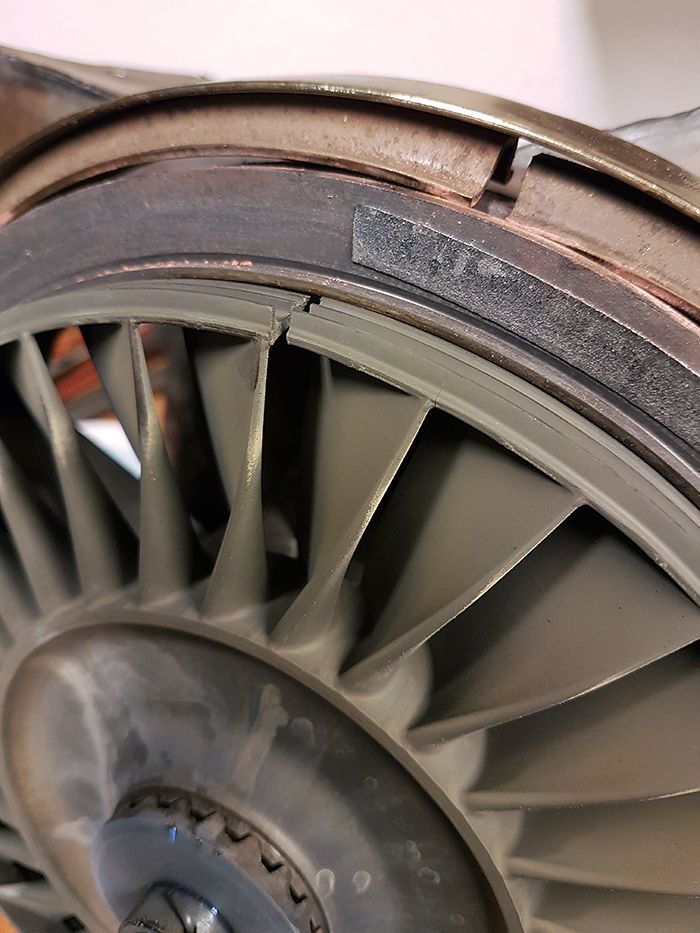 This is a good reminder to keep the temps in check, the new engine seems to be running at much more reasonable temperatures so I´ll just decide to not let the interstage temps go much past 750°C and this shouldn´t happen again. 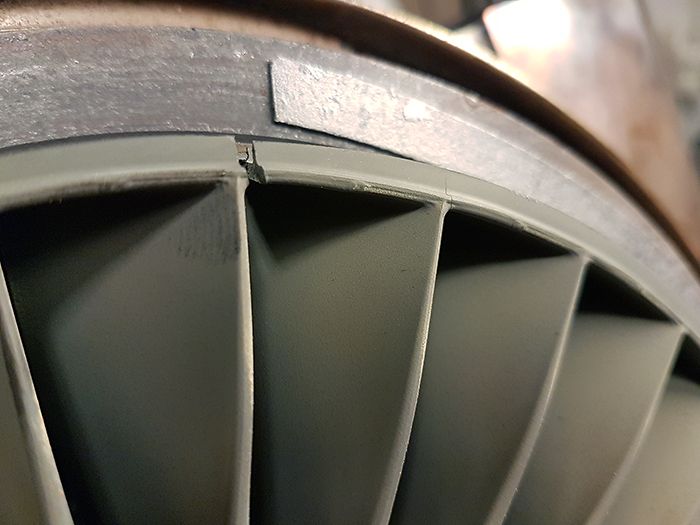 I have a fresh 4th stage wheel on the shelf but am in need of a spare one so in case anyone has one they want to part with I am interested as long as the price is right. Cheers! /Anders
|
|
|
Post by Johansson on Sept 17, 2017 15:40:36 GMT -5
Hi Tony, Not really, I just ordered the largest spray nozzle I could find for reasonable money. 
|
|
|
Post by Johansson on Sept 17, 2017 12:16:46 GMT -5
Congratulations!!!
|
|
|
Post by Johansson on Sept 7, 2017 1:54:10 GMT -5
Hi Anders Yep , start with a fully open NGV and see how the temps are , then slowly close off openings to raise the temps to the desired level of ~750-800C for the interstage ......LOL, we'll keep the needle on the gauge ;-) The static gas pressure in the interstage will keep the NGV forced against its seating so it'll only need a minimal amount of fixings to have it sitting in position and free to "move around" as the temps and expansion dictate , any minor leakage won't affect power output by more than a horsepower at most. Cheers John Hi John, That is the plan, first I'd like to see moderate running temps and later I can start blocking off the freepower NGV until I get the best "safe" performance out of the bike. I could make some kind of sliding fit for the C20 NGV and use it as the expansion point for the engine, the I can mount the JU-02 firmly in the chassis. The track gets quite bumpy at speed so it is probably a good thing to have the gas producer secured so it won't jump around and possibly damage the interstage duct. Cheers! /Anders
|
|
|
Post by Johansson on Sept 7, 2017 1:46:47 GMT -5
Hi Anders, In your prior post you mentioned there was some kind of an instability at low RPM when you injected the water/meth. What are your thoughts on how it worked (or didn't work) like it did? Can you describe how it was set up compared to the PDF in your boosting gas turbines thread? Water/meth injection is a subject I will definitely test in my build. jetandturbineowners.proboards.com/thread/889/boosting-gas-turbines-bill-gunstonThanks, Tony Hi Tony, I don't know if the low boost fluttering I had was caused by the water or something else, the engine "hickuped" a few times during each run for some reason. The setup is a large capacity spray nozzle aiming into the compressor inlet. You can see it in the riding video, I held the throttle pinned throughout the run but the P2 dipped down towards 2 bar a few times. I will have to check if I have a problem with voltage drop when all pumps are working hard, it shouldn't behave like this. Another thing I will try is to change from 5w30 oil to 10w60 and see if the oil pressure stays more constant when the oil starts to heat up, if not I might have to add a separate oil pump for the gearbox lubrication instead of sharing pump with the gas producer.
|
|
|
Post by Johansson on Sept 6, 2017 12:03:31 GMT -5
Hi Anders Another reason for the bypass, even if you don't have excessive idling temps, is that it'll keep both turbine wheels "cooler" until you start your run resulting in a bit more time for things to heat up, it'll provide a bit more "safety" buffer as our max design temps are going to be on their limits . I'd be opting for a "clamped" fit for the freepower NGV , loose enough so that it can expand/contract quicker than the surrounding interstage material, also there might be a need for blocking off some of the passageways in the NGV if we find its too "open" .............it'll depend on gas temps/densities/mass flow etc etc .............so easy removal for mods would be desirable . Cheers John Hi John, I think I will settle with a running temperature that is more "daily driver", I don't like the idea of running on the outmost edge where the turbine wheel is almost at melting temps when I pass the finish line. Clamped it is then, another benefit is that I can get me a spare one that can be easily fitted in case I need to at race day. Cheers! /Anders
|
|