nersut
Veteran Member
 
Joined: September 2012
Posts: 223
|
Post by nersut on Oct 25, 2012 1:56:23 GMT -5
Update Hi, today I was busy modifying the FJK-2 I made a stationary starter system with a regular vacuum cleaner motor, some plastic tubing & a one-way valve. Ugly but works fine! ;D 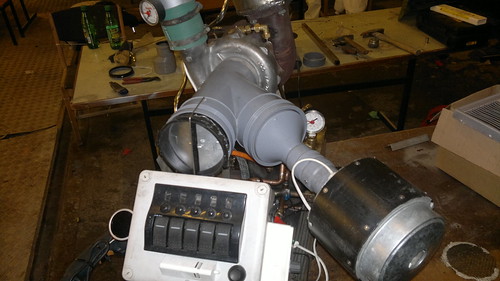  When I start up the vacuum motor the one-way valve closes & forces air through the gas turbine. When the gas turbine starts & spools up the one-way valve gradually opens automatically. I used the same system on the FJK-1 with no problems.  I will make the system more compact later. I installed a new reinforced silicone hose on the compressor outlet. 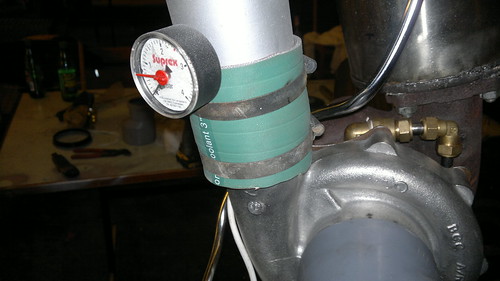 I also installed a jet nozzle but I haven't made it taper yet. Later I will find the correct size according to TOT temperature. 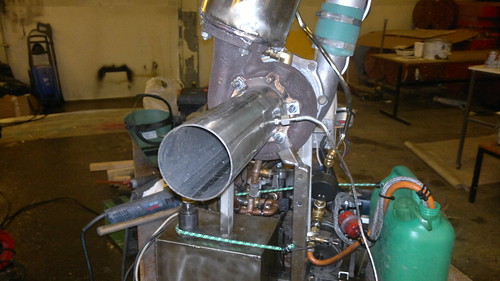 Overview 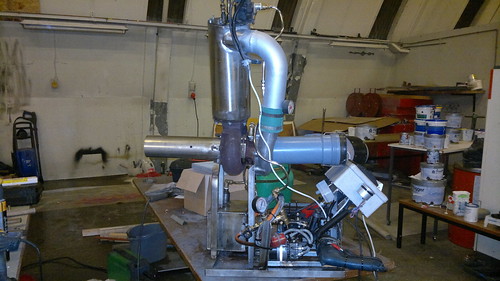 I did a short (indoor) ;D test with the small preheat/start-up fuel nozzle. It was raining outside, hehe! Starts fine and burns with no smoke with the starter motor running, TOT about 320° Celsius (can't self-sustain, way too small fuel nozzle) Tomorrow I will test the big fuel nozzle  Cheers Erik
|
|
|
Post by Johansson on Oct 25, 2012 2:30:04 GMT -5
Very neat starting system, I wish my JU-01 was that easy to get up to starting revs... 
|
|
|
Post by racket on Oct 25, 2012 3:10:06 GMT -5
Hi Eric
Please make sure theres absolutely no way anything can be sucked into the compressor wheel during disengagement , our engines are the vacuum cleaners from hell when it comes to suction and ingesting anything and everything possible given half a chance .
What did you use for the one way valve , it looks very nice :-)
Cheers John
|
|
|
Post by racket on Oct 25, 2012 3:16:38 GMT -5
Hi Anders
Yeh , those TV94 rotors take some spinning in brass bushes :-(
One thing I'm going to try making is a "super leafblower" using a Toyota starter , minus gearbox, same as I used for the 10/98 engine , and have it mounted into a standard leafblower where the ~26cc IC engine normally fits and driving the impellor , the normal leafblower rpm is ~9,000 , but the Toyota starter will go >20,000 on 24 volts and should pump a fair bit of air at a modest pressure .
Cheers John
|
|
nersut
Veteran Member
 
Joined: September 2012
Posts: 223
|
Post by nersut on Oct 26, 2012 0:24:21 GMT -5
Hi John The starter system is stationary/permanently mounted. The one-way valve is from a cooker hood and is spring loaded with a tiny spring. I only have to control the speed of the vacuum motor, that's all  __________________________________________ I tested the FJK-2 today, and it ran fine.  I have to install more bolts to hold the end cap sealed, because it was leaking air/smoking  And I have to find some electric fans for the oil cooler, currently I am using a small 12 watts PC/Server fan (not enough air flow). Max TOT temperature was 580° Celsius at full fuel pressure. Fuel flow must have been about 13-14 GPH at full fuel pressure. 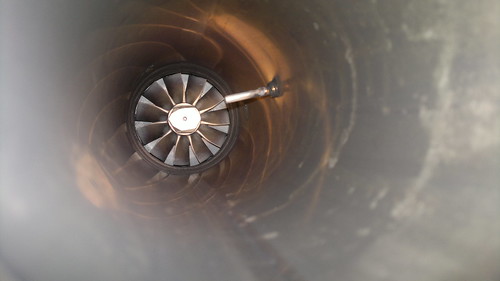 The turbine wheel & the jet nozzle is very clean & shiny after the test run. 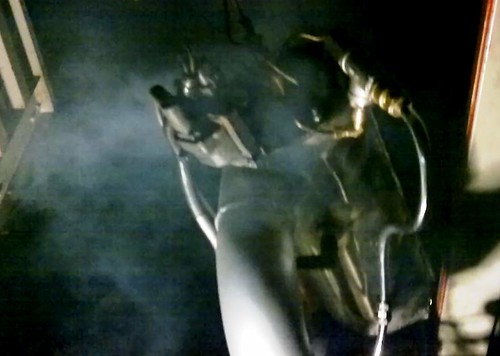 End cap leaking air. Here is my start-up procedure: - Oil pump, ON
- Adjust oil pressure to about 2 bar.
- Check the ball valve for the main fuel nozzle is in closed position.
- Fuel pump, ON
- Adjust fuel pressure to max, about 14+ bar.
- Spark ignitor, ON
- Fuel solenoid, ON... wait for the gentle poof. (Ignition)
- Starter motor, ON... adjust to 1/4 speed.
- Spark ignitor, OFF
- Wait for a couple of minutes to heat up the oil/engine (TOT temperature about 350° Celsius)
- Adjust oil pressure to 3-4 bar
- Adjust fuel pressure to about 7 bar.
- Starter motor full speed.
- Slowly open the ball valve for the main fuel nozzle... Gets very loud!
- The engine spools up & the one-way valve opens automatically.
- Starter motor, OFF
- Check oil pressure & adjust if needed.
- The engine is self-sustaining!

I will test the engine again tomorrow and take some pics/video & data. Cheers Erik
|
|
nersut
Veteran Member
 
Joined: September 2012
Posts: 223
|
Post by nersut on Oct 26, 2012 3:04:48 GMT -5
Hi Anders How much airflow does your JU-01 need for start up? Some vacuum motors flow over 150 CFM or 4.250 liters/min.  Maybe big enough for start-up ?? Cheers Erik
|
|
|
Post by racket on Oct 26, 2012 4:14:48 GMT -5
Hi Eric The TV94 comp has a 98mm inducer and needs a lotta air for starting , they flow ~1,000 CFM at idle , I used the TV94 rotor in my 9/94 engine www.youtube.com/watch?v=8Y8jpaDTkEY it was equipped with ball bearings on the rotor so that it spun very smoothly but the leafblower was struggling to provide sufficient air to get it to spoolup . When we fit the TV94 rotor in standard turbo brass bush bearings and thrust bearing the rotor becomes very hard to turn , requiring ~0.5 ft/lbs of torque to move it , a leafblower won't even get it spinning , I used an automotive starter motor to get my 10/98 engine to fire up www.youtube.com/watch?v=NR0rsTbkOS4I did use a 4 horsepower industrial sized leafblower with a 0.5 lbs/sec airflow rate that was barely sufficient to spoolup my GT60 kart (106mm inducer) www.youtube.com/watch?v=ScZ0u5ob6aU as its bearing design has a "balanced" thrust bearing that doesn't produce a lot of drag , my mate Smithy has since fitted an electric start www.youtube.com/watch?v=qi47QKtXKk8&NR=1&feature=endscreenLotsa options :-) Cheers John
|
|
nersut
Veteran Member
 
Joined: September 2012
Posts: 223
|
Post by nersut on Oct 26, 2012 4:44:29 GMT -5
Hi John Okey... Your engines need a lot more air/rpm/power for start-up than I thought .  I tried with electric starter for the FJK-1, I used a angle grinder, removed the reduction gear & welded a 10 mm socket on the shaft. = 40.000 rpm electric starter.  Starts fine, many start-ups... UNTIL the starter literally "exploded" in my hand when the engine spooled up. That really hurts!  The copper winding's & the epoxy resin exploded into hundreds of high speed shrapnel's inside & thankfully the casing contained most of the fragments. That's why I am using the vacuum cleaner motor now.  Cheers Erik
|
|
|
Post by racket on Oct 26, 2012 23:33:10 GMT -5
Hi Erik
You were fortunate that your fragmenting angle grinder starter didn't send material into the engine , thats the problem with having something "in front" , the pneumatic method is a lot safer .
On larger engines its hard to get the combination of enough airflow ,with some pressure for forcing the air through the engine so that it starts to power up the turbine wheel to help with spoolup, vacuum cleaners are ideal for smaller engines as they're generally pretty powerful and produce a good pressure compared to the average leafblower , its that combination of flow with pressure thats important and is the reason I will be trying to make my own "super blower"
Cheers John
|
|
nersut
Veteran Member
 
Joined: September 2012
Posts: 223
|
Post by nersut on Oct 28, 2012 2:31:53 GMT -5
Hi John Your idea with 20.000 rpm! "leaf-blower" sounds interesting.  Lets hope the impeller doesn't blow apart by the centrifugal force.  _________________________________________________ I ran in to another problem during a test run yesterday... Oil pressure. I set the oil pressure to 4 bar before starting the engine... But as soon as I crank up the engine to over 1-1.5 bar P2 pressure then my oil pressure drops to a dangerously low pressure of 2 bar or less... EMERGENCY SHUTDOWN!  I tried to increase the rpm of the drill/oil pump to max speed, about 1.000 rpm with no positive effect... Hmm  The oil I am using now is 10W-30 & was not even getting to it's optimal temperature. I think my power steering pump has a built-in pressure regulator/relief valve? Or the pump is not flowing enough oil to keep the pressure when the turbo it gets up in speed? Or both... The power steering pump is from a Hyundai Sonata from about 2005-2008. My oil system is routed: Oil tank->Oil pump->Oil pressure regulator->Oil cooler->Turbo->Return to oil tank. The end cap is still leaking air/smoke, Not enough bolts.  I will fix this later by adding twice as many bolts, & maybe use a thicker end cap. Here is a short video-clip from the test run in not so good conditions, night & rain. Cheers Erik
|
|
|
Post by racket on Oct 28, 2012 3:54:40 GMT -5
Hi Eric
LOL...if the "plastic" leafblower impellor fails , I'll make one out of metal , but as most leafblowers have impellors that can be used for vacuuming leaves as well , they're built pretty tough , I'll probably have to make some sort of metal mounting plate/flange for the motor shaft that I can bolt the impellor to, it'll be fun to experiment ,............. the Toyota starter I used ran up to ~12,000rpm on 12 Volts but on 24 volts I had to get to ~22,000 rpm for the 10/98 engine to selfsustain , I'll be more worried about the starter motor exploding :-)
Power steering pumps require their internals to be modified , restrictive passageways opened up , it can be done , and they then make good lube pumps .
Cheers John
|
|
nersut
Veteran Member
 
Joined: September 2012
Posts: 223
|
Post by nersut on Nov 1, 2012 15:22:48 GMT -5
Hi John I have now removed the power steering pump from the frame. When I removed the oil outlet connector then I could see some sort of a regulator on top of the pump. I removed the regulator part. It was a spring loaded pressure relief valve/piston. The spring was not particular hard, I could compress it with just two fingers. 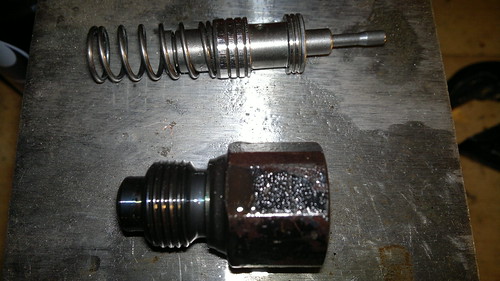 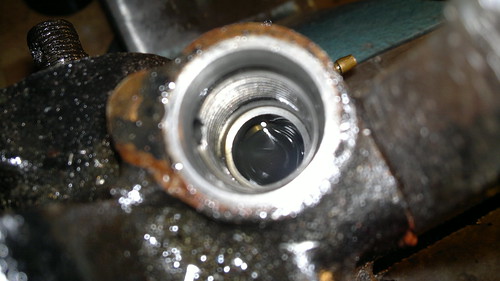 A slot/hole from the pressure side to the inlet gets visible when I depress the piston/spring. I will put a piece of metal bar underneath the valve/piston to stop the pressure dumping. And I will drill some of the holes larger in the pump which is pretty small. Cheers Erik
|
|
|
Post by ernie wrenn on Nov 1, 2012 16:07:03 GMT -5
Put shims under the spring to raise the pressure(or use heavier spring) pop off but leave it in place. If you dead head the pump you could blow a line or burn up your drive motor. You can be surprised with the amount of fluid they can move with a split hose.
ernie
|
|
nersut
Veteran Member
 
Joined: September 2012
Posts: 223
|
Post by nersut on Nov 2, 2012 1:57:03 GMT -5
Hi Ernie I already modified the pump before I read your post. I put a piece of metal bar under the piston & put the spring on the other side of the piston. I did this because the piston was sucked up & blocked some of the oil flow. And I drilled a bigger hole on the pressure side. The pump is now running much better & produces 1 bar at the lowest setting & pumps happily over 4 bar.  I can regulate the oil pressure with a bleed valve. ___________________________________________________ Update I packed up & drove to a remote area to test the FJK-2 for the 2nd time. It was at night/dark & cold, minus 5° Celsius. The FJK-2 was running great, easy start & spool up. - P2 pressure: 1.5 bar
- Fuel pressure: 12 bar
- TOT Temperature 590° Celsius
- Fuel flow:˜13 GPH
- Oil pressure: 3.5 bar
Here is a short video of the test run. BUT, right before (2-5 sec.) I shut the engine down it made some weird noises...  I found out that the compressor wheel had rubbed the housing & made some marks. 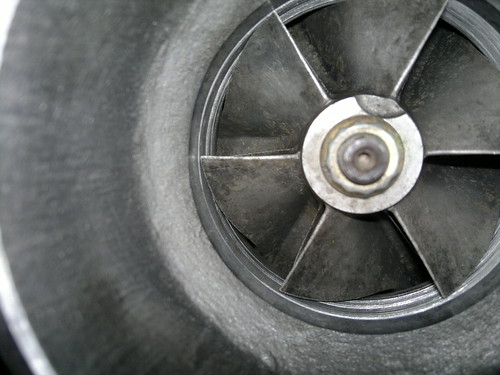 I think that the bearings in the turbo has taken some damage from the previous test run when the oil pressure drop to under 2 bar under full load...  The shaft has now side-to-side movement... You can hear the metal-to-metal rubbing/rattling noises at the end of the video. Will a set of rebuild/service kit "cure" the turbo?  I found a Garrett service kit no. 468132-0000 for the turbo. Cheers Erik
|
|
|
Post by racket on Nov 2, 2012 2:22:13 GMT -5
Hi Eric
Side to side movement is "normal" with turbos as there a fairly large clearances on both ID and OD of the "brass bushes" , the shaft and bushes are designed to "float" on thick layers of lube .
The critical point is .............has the axial clearance ( in and out) increased beyond just the very smallest movement ( a few thou) .
Your TOT of 590 C was rather high for an engine without a jetnozzle running at only a 1.5 bar P2.
Fuel flow was also rather high .................somethings not adding up here :-(
Cheers John
|
|