|
Post by Johansson on Oct 20, 2012 7:55:06 GMT -5
Good luck!
|
|
nersut
Veteran Member
 
Joined: September 2012
Posts: 223
|
Post by nersut on Oct 20, 2012 16:46:45 GMT -5
Update I tested the FJK-2 today & the spark ignitor worked well.  Here are the test data results: 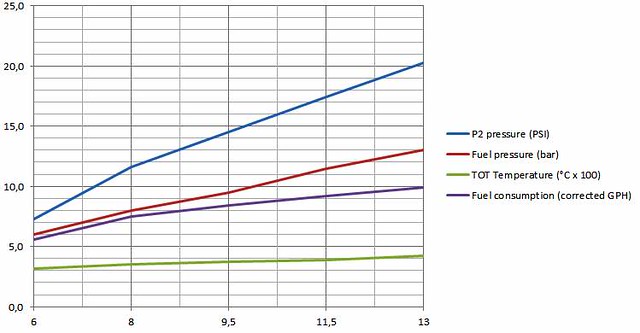 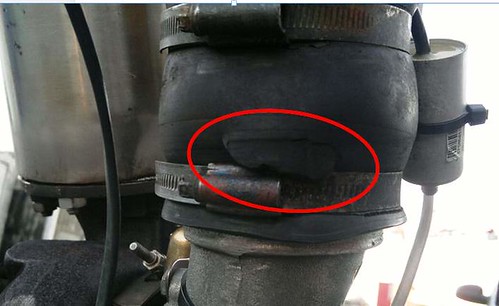 At full fuel pressure the compressor hose gave up with a loud BANG & big flames, the TOT temp spiked really fast before I shut it down.  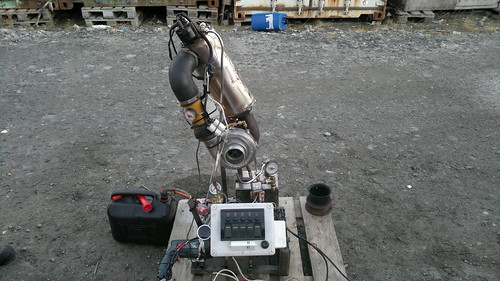 I turned the turbo/combustor up so I don't have to worry about flooding the combustor.  Rear view with a Greenlandic flag on top. ;D ;D The larger & "bend" holes near the end cap helped a lot, no more red glowing end cap.  Thanks John! ...I think I am the first & only one in my country with a DIY gas turbine  Cheers Erik
|
|
|
Post by racket on Oct 21, 2012 1:59:42 GMT -5
Hi Erik
Can't seem to get the images :-(
Congratulations on the improvements , development going well :-)
Cheers John
|
|
nersut
Veteran Member
 
Joined: September 2012
Posts: 223
|
Post by nersut on Oct 21, 2012 3:17:45 GMT -5
Hi John Okey my data graph is confusing... My bad.  The horizontal line is the fuel pressure & the vertical line is the P2, TOT & fuel consumption values. The 7.5 GPH fuel nozzle maxed out at: - 20 psi (1.4 bar) P2 pressure
- with 420 ° Celsius TOT
- at about 9.9 GPH fuel comsumption
I ordered a Digital laser tachometer with 0-99.999 rpm readout. Hopefully it will come soon so I can "safely" find the max P2 pressure with a bigger fuel nozzle.  100 % N1 should be about 92.700 rpm (calculated in JetSpecs). 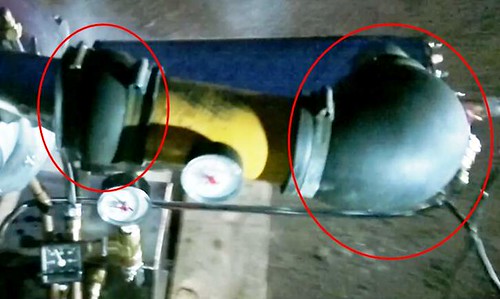 And I am going to replace the 90 degree rubber elbow with a stainless steel one, because the rubber hose expands like a balloon when I crank up the fuel pressure... Its little scary with my head next to it. ;D Cheers Erik
|
|
wolfdragon
Senior Member
 
Joined: April 2011
Posts: 287
|
Post by wolfdragon on Oct 21, 2012 8:58:18 GMT -5
I was watching that 90 degree elbow in the video and was getting a bit curious about it's reliability...
At least it was the little one that blew...
I imagine that an ebay search will help you find the reinforced silicone hoses that are meant to be used in cars to hook these guys up...
|
|
nersut
Veteran Member
 
Joined: September 2012
Posts: 223
|
Post by nersut on Oct 21, 2012 17:40:20 GMT -5
Hi wolfdragon I am not going to use rubber or silicone hose for the 90 degree elbow. Instead I am going to weld a stainless steel elbow so it should be a little safer.  I am wondering why the relative thick rubber hoses expands that much? I took those hoses from a big excavators turbo-to-inlet manifold, they should be able to cope with the pressure...  Cheers Erik
|
|
|
Post by racket on Oct 21, 2012 23:13:09 GMT -5
Hi Eric
Use metal tubing/bends where ever possible on our engines and only use flexible couplings where absolutely necessary for expansion or vibration cures.
A short length of reinforced rubber hose ( radiator type) is generally good enough if the metal to metal tubing gap is <0.5" .
The large excavator might only have run low boost .
Cheers John
|
|
|
Post by stoffe64 on Oct 22, 2012 1:31:32 GMT -5
hello!
thanks for the pics, i wonder if you have any pics from the combustor liner/flametube- turbine inlet slipjoint how you made that thing, i am working on a similar setup with a Holset HX60W turbo but i get stucked on that part! cheers stephan
|
|
|
Post by Richard OConnell on Oct 22, 2012 3:10:15 GMT -5
I hadnt noticed the expanding rubber joints in the video, but now that you point them out, they appear to be quite terrifying. I'm glad no one was injured when it finally went.
|
|
nersut
Veteran Member
 
Joined: September 2012
Posts: 223
|
Post by nersut on Oct 22, 2012 18:20:00 GMT -5
Hi stoffe64 I made a simple slip joint by welding a short piece of stainless steel tube on the turbo flange. I then "filled" the tube with welding rods to smooth the transition from the round tube to the rectangular flange. The slip joint is on the inner side of the flame holder. 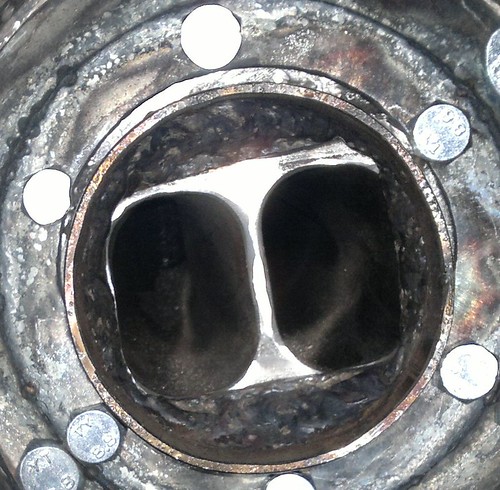 The turbo flange/slip joint 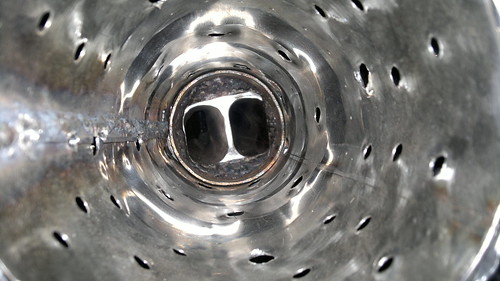 Flame holder installed, still needs to grind some metal off. The flame holder is bolted on the end cap to keep it centered. It is not elegant but it works! ;D I hope you got the idea & good luck with your build!  The Holset HX60 should be able to flow 0.95 kg/sec or 2 lbs/sec thats the twice as much as mine FJK-2. I have to get one...  ;D Cheers Erik
|
|
nersut
Veteran Member
 
Joined: September 2012
Posts: 223
|
Post by nersut on Oct 23, 2012 0:14:33 GMT -5
Update Hi I have removed the combustor to replace the rubber 90 degree elbow. I noticed that the inside of the flame holder was covered in thin black dry sod & there was a visible swirling marks from fuel burn.  Sod marks  Swirling markings 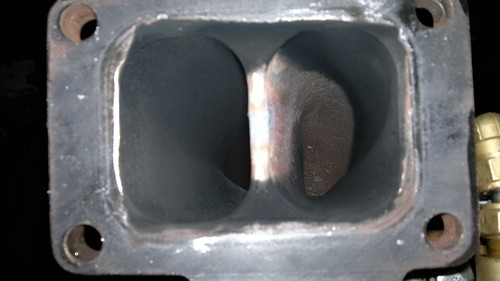 The turbine inlet is also covered in sod. After the first test runs there was no sod inside the flame holder. I believe that the fuel is not burned completely after I bored the first row of the primary holes to 10 mm... Too much cooling effect? I don't think it is bad mixing of the fuel. Maybe I should make some of the 10 mm holes smaller again. Here is a short video clip of the spark ignitor test. The ignitor is build using a regular 12 V automotive coil connected to a 220 V/50 Hz speed regulator (pulse width modulator) & 1 micro-farad capacitor. It is pretty powerful with 50 sparks a second & no trouble igniting diesel fuel. __________________________________________________ How well does your gas turbine burn the diesel fuel? Any sod? Please post pictures of your flame holder for comparison  Cheers Erik
|
|
|
Post by racket on Oct 23, 2012 0:55:23 GMT -5
Hi Erik
Does your engine exhaust black smoke ??
The small amount of black soot covering could happen during spoolup or shutdown , it also indicates that metal temperatures aren't overheating , it appears that the only place there isn't any is in the primary zone area where the combustion is occuring and the radiant heat is burning off the soot as it should .
Diesel can be a bit "smokey" at idle conditions unless your atomisation is pretty good , that generally means high fuel pressures at max power if we want >50psi at idle .
The swirl witness marks are caused by your tangential air inlet at the combustor wall , too much swirl can cause combustion problems .
Cheers John
|
|
|
Post by stoffe64 on Oct 23, 2012 5:58:56 GMT -5
hello! thank you for your pics of the turbine inlet and flametube slipjoint in fact i was not so far off then because i started something similar like you did, now i know that i wasnt so far off then and that it should work, thank you once again for your help it was worth a million(if i could pay it) THANKS!  ...I COULD ALMOST  NAH KIDDING 
|
|
nersut
Veteran Member
 
Joined: September 2012
Posts: 223
|
Post by nersut on Oct 24, 2012 1:22:58 GMT -5
Hi John The engine doesn't smoke when it runs. You mentioned that it could be from idle run. I tested the engine at idle at almost 0 bar P2 pressure several times, the sod could be from the idle tests.  ___________________________________________ Hi stoffe64 You are welcome! It is good to hear that my work is helping others too.  Post some pictures of your engine. ____________________________________________ Update Today I modified the fuel system. I have now 2 fuel injectors installed on the end cap. The first one is a small 0.5 gph nozzle for startup/preheat & the other one at the center is the main fuel nozzle & was "upgraded" from 7.5 to 9.5 gph. I installed a ball valve for the for the main nozzle.  Dual injection system 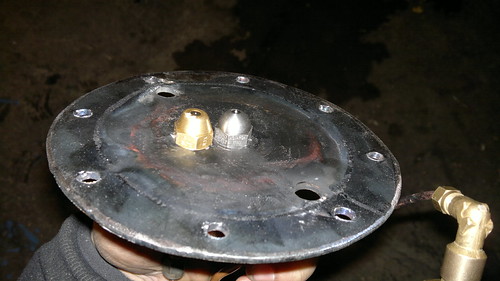 The nozzles I also removed the rubber elbow & welded a stainless steel elbow instead. 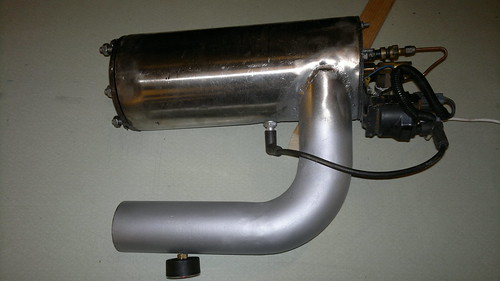 I tested my new tiny 35 Watt Ultrasonic Cleaner  I cleaned the dirty 7.5 gph fuel nozzle  Before cleaning 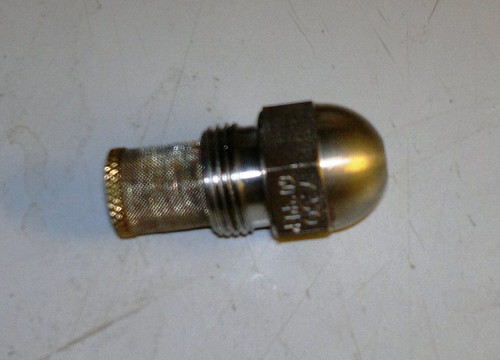 After cleaning It is amazing to see how well it performed. I will post the results after testing the new fuel system. Cheers Erik
|
|
|
Post by racket on Oct 24, 2012 3:08:30 GMT -5
Hi Eric
If the engine isn't smoking at idle, then don't worry about the bit of soot in the flametube , it doesn't take much poorly burning diesel during a spoolup to make enough soot to cover the engines insides , and if the engine isn't subsequently pushed to high temperatures it won't burn off .
Cheers John
|
|