|
Post by Johansson on Feb 5, 2011 17:05:00 GMT -5
I must admit that the mood was far from good sometimes, but after a meal and a good nights sleep I was always eager to continue the struggle.  Great paper there John, it sure explains why the ball bearings had problems surviving in my old gas turbine. ;D One thing I´ve been thinking about regarding the scavange pump, you say that we need four times the oil flow to remove the air bleeding in through the piston seals but I just can´t get my head around that statement. Assume that the scavange pump handles the oil pump flow with some margin, the air that leaks through the shaft seals makes the shaft tunnel pressurised by the P2 number. That in turn makes the pressure drop over the bearings less but with a strong enough oil pump that won´t be a problem. As I see it we don´t really need to suck any air from the shaft tunnel, the oil pools up in the bottom where the suction line is located so even if the scavange pump isn´t strong enough to remove the positive pressure inside the shaft tunnel it should still be just as capable of removing the oil under pressure as it is while bench testing it without the engine running. Please enlighten me if I am wrong.
|
|
|
Post by racket on Feb 5, 2011 18:09:24 GMT -5
Hi Anders Yeh the oil froths up pretty bad with air'gas leakage into a larger volume , and yes the air/gas leakage thru the seals will tend to pressurise the oil cavity and help force the oil out of it , but if theres more "pressure" towards the front from air leakage past the comp seal then the oil could bank up at the turb seal and perhaps force past it , lotsa unknowns  thats why we need an "oversized" scavenge pump so as to create a bit of a "vacuum" in the cavity, to in a sense, suck air/gas thru the seals to keep oil well away from them . On one of the Rover car gas turbine engines they used P2 bleed air to pressurise the bearing cavity to force oil back to the sump rather than just rely on gravity . With the 10/98 I was using a small 12 V air comp to feed air into the lube cavity near the turb seal for oil scavange , on the 9/94 engine I used P2 air with only a restrictor to limit the flow of bleed air to near the turb seal , this wasn't as good because at higher P2 pressures too much air was supplied whilst at idle barely enough , probably needed to supply P2 to a low pressure regulator and restrictor , maybe something that only produces low "inches of water" pressure to the cavity rather than psi pressure . I've found that oil is bypassing the turb seal ( none at the comp seal) on both the 9/94 and 10/98 on shutdown , resulting in jetpipe fires from the oil catching fire as it contacts the hot turb blades/NGV  ....... a scavange pump would hopefully stop this from happening. The fact that there isn't leakage at the comp seal , which is adjacent to the lube drainage point sorta suggest the oil is backing up at the turb seal but free to drain near the comp seal . When feeding oil thru a non running engine the oil comes out of the engine looking much the same as it goes in , but once that rotor is spinning the oil soon froths up , have a look at the vid I sent you of the 10/98 oil drain line , its got a frothy mess draining thru it , thats what any scavange pump has to handle , the quantity of oil flow thru the engine will also increase several fold once the oil and motor are hot and running compared to when the engine is cold and stationary , you'll probably find that a cold engine is only flowing a couple of litres/minute at most. Ideally , to save the complication of having a scavange pump , sump pressurisation and perhaps some sort of "air seal" at the turb seal to enhance its effectiveness might be the way to go . Lotsa unknowns with a new engine  Cheers John
|
|
|
Post by Johansson on Feb 6, 2011 15:15:44 GMT -5
I guess that the only way to find out if the scavange pump works is to test it, if not I have the option to fit a second suction line to the oil gallery to double the flow area. I am reconsidering the choice of fork and wheels for the bike frame, my first idea was to use the ones from my old turbo bike (a GSX750 -84) but since the brakes on that bike was totally worthless it feels stupid to build the frame around parts that I will need to change sooner or later. Now I am thinking about lightening the purse a bit and get me a set of Yamaha R6 wheels along with the fork from -04 or newer, they look really sweet as well.  
|
|
|
Post by racket on Feb 6, 2011 17:05:49 GMT -5
Hi Anders
Yeh , it'll soon be obvious if you need to increase scavange capacity , she'll be smokin' :-(
Good brakes are essential with a turbine engined bike , we can't rely on engine braking , it doesn't exist , if anything there's a tendency to have a faster idle when we back off from high power settings due to the heat buildup in the parts supplying heat above what the "idling" combustion is supplying ...........................those crap brakes on my first bike were a real worry , the ones on the frame Andrew is using for this latest build are "nice " :-)
Cheers John
|
|
|
Post by Johansson on Feb 8, 2011 16:20:11 GMT -5
|
|
|
Post by racket on Feb 8, 2011 18:44:55 GMT -5
Hi Anders
She's starting to look like an engine now :-))
Thats a fine looking can .......... whats the wall thickness ?? ...............is it "tapered" or straight walled ??...................whats the ID of the can at the comp cover ?? Andrew and I searched everywhere for a decent can for the 9/94 engine and couldn't get anything as good as that . .................lucky bastard :-)
Are you going to fit an exterior support ring around the exhaust stub to support the can and stop it from bulging out between bolts ??
Cheers John
|
|
|
Post by Johansson on Feb 9, 2011 1:22:26 GMT -5
Yup, a jetpipe and no one can tell that it is anything but finished even though it is missing a combustor...  1.5 or 2mm, will have to check that one along with the exact inner diameter. 240mm give or take a couple of mm´s. It is very rigid and rings like a bell when struck. Straight sides and a slight bulge at the top where the holes are cut. I´ve thought about making such a ring, there is no visible bulging at all when I torque the nuts down (that could perhaps have another meaning in english... ;D) but I might make one anyway just to get a better sealing. I don´t think that I will fit any mounting bolts in the comp diffusor cover, I am afraid that once torqued they will distort the cover and make the O-ring leak air. Now it is also free to expand a little from the heat differances, it can vary from -15C to perhaps >100C so I assume there will be some movement. Cheers!
|
|
|
Post by Johansson on Feb 9, 2011 14:38:31 GMT -5
I got not one but two Allison turbine wheels by mail today free of charge!  The guy who sent them to me told me that the retail price for one wheel is 11.968 USD so I am glad that I didn´t have to buy a pair of new ones... ;D 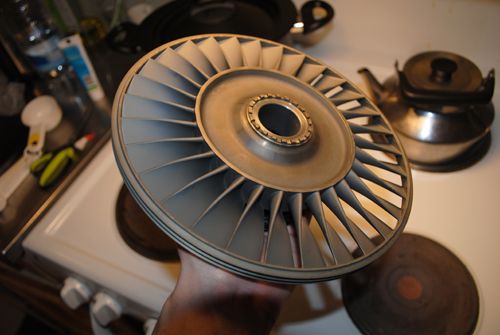
|
|
turborico
Member

Joined: December 2010
Posts: 24
|
Post by turborico on Feb 9, 2011 15:03:02 GMT -5
Most impressive!
|
|
|
Post by racket on Feb 9, 2011 17:04:10 GMT -5
Hi Anders
Heh heh , did your Christmas presents come a bit late this year ;-)
They're a couple of fine lookin' wheels , you'll have fun spinning them around .
I'll be interested to hear about the can dimensions , it looks the perfect thing for the job , but will probably need that exhaust stub ring to seal things completely once you start running the engine up to >40psi of P2 , it'll only need to be in 5mm thick material .
Yeh, the alloy comp cover expands into the stainless outer can until it seals tight then the stainless will receive heat and relieve the tight fit until the heat transfer drops and things stabalise at a reasonably sealed fit , at full T2of ~160-180 deg C theres nearly a 1mm increase in a 250 mm dia alloy disc , it seals tight :-)
Excellent wheels, a good find ...........they'll make the horsepower you want.
Cheers John
|
|
|
Post by Johansson on Feb 14, 2011 15:38:50 GMT -5
I think I just got 50 years worth of christmas presents in one box.  They are really sweet looking, now I just have to figure out how to make the claw coupling on each side of the wheel that locks it in place on the shaft. Although I shouldn´t worry about this before I have the gas turbine running as a pure jet, will I need cheramic bearings for the power turbine shaft or would home converted full complement steel bearings work? The shaft needs to be 1" at the gearbox end so I guess that is the inner race diameter as well unless I make a two piece shaft or fit sleeves of some sort at the ends of the shaft. Hehe, 40 psi. Just thinking about it gives me goose bumps. 
|
|
|
Post by racket on Feb 14, 2011 18:48:03 GMT -5
Hi Anders
I found I needed a 1.005" shaft for my pinion if I want a tight sliding fit as its got a "nominal" 1" bore .
The curvic coupling isn't a problem , we don't mount against it but the surface inboard of it , and only have loose fitting "teeth" fitted into the curvic which they don't need to touch .
I've designed for a 30mm bore C3 bearing at the pinion end where thrust loads are and a lighter weight 25mm bore at the turb end with a wave washer preload against it
Standard C3 bearings should be good enough if plenty of pressure fed lube is supplied to cool them during the limited run times we'll be using .
We need a spacer between pinion and bearing because of the gearbox arrangement , I've got my early drawing already done so can send you a copy if you like :-)
I need to finalise actual turbine wheel rotational direction before doing the final drawing , and as I'm not certain of the freepower assembly mounting position I can't say which way it'll need to be mounted on the shaft and the thrust load direction , currently the helical gear thrust and gas pressure thrusts are in the same direction , not so good :-((
Cheers John
|
|
|
Post by Johansson on Feb 15, 2011 12:59:44 GMT -5
I would be interested in seeing your shaft design, haven´t given it any thought yet but an idea or two about the bearing configuration would be nice.  Do I need to have a teeth coupling on both side of the wheel or would it be enough to have it on the side closest to the bearings? Your wheel will by the way be fitted the other way around compated to mine, my gas producer will push the wheel onto the shaft while yours will struggle to tear it loose. Cheers!
|
|
|
Post by racket on Feb 15, 2011 17:55:04 GMT -5
Hi Anders
We only need "teeth" into one curvic , they're only there to provide a positive grip on the wheel in case the shaft nut doesn't provide sufficient "friction" to hold the wheel in place , they're "insurance" , .....I cut the threaded protrusion off leaving only a small length( ~2mm) protruding above the mounting flat , I have my shaft nut with a flange that can be lock punched into a shallow recess in that 2mm protrusion , the threaded portion also has a smaller bore than the actual wheel , so best to remove it so that the wheel can be more easily mounted by having a sleeve between the 25mm shaft and ~30mm wheel bore .
LOL , you may need to check the thrust directions , as I don't think it makes much difference which way you orientate the wheel as it appears the gear helix direction dictates that both thrusts will always be in the same direction . ..................duh , I think ;-)
I'll see how I go emailing you a copy of my drawing and then we can workout whats best for your "straight through " setup .
Cheers John
|
|
|
Post by racket on Feb 15, 2011 18:00:17 GMT -5
Hi Anders
Bugger , it doesn't scan very well , pencil lines are too faint :-((
Will do another drawing for your application
Cheers John
|
|