|
Post by madpatty on Dec 26, 2014 11:30:06 GMT -5
Hi Johansson, I dont think this will be much different than some old turbochargers with vaned diffuser discharging in large plenum......obviously efficiency cant be as compared to standard design.....
But what i am thinking is using a soft bend at the outermost Edge of the diffuser to bend any air still moving radially outwards 90 degrees towards the combustion chamber to further reduce any losses occuring due to air at high velocity striking the outer can....
And moreover there's always fun experimenting....
Cheers, Patty
|
|
|
Post by madpatty on Jan 9, 2015 12:03:24 GMT -5
Hi Guys, Progress made on the NGV design as of now..... Assuming TIT of 900 deg.celsius at 3.0 PR....Actual pressure ratio going into the turbine stage will be 2.85....Assuming the flow to be choked through the NGVs, the static PR at the NGV throat will be 1.54 PR at 733 degree celsius and hence density of 0.54 kg/m3....That gave me a choked nozzle throat area of about 895 sq.mm or 1.39 sq.inch.so to get the required throat area(and adding some area for compensating discharge coefficient) i designed and welded 21 vanes set at 20 degrees to the tangent....the vane height was kept equal to the turbine blade inducer tip height of 12 mm... 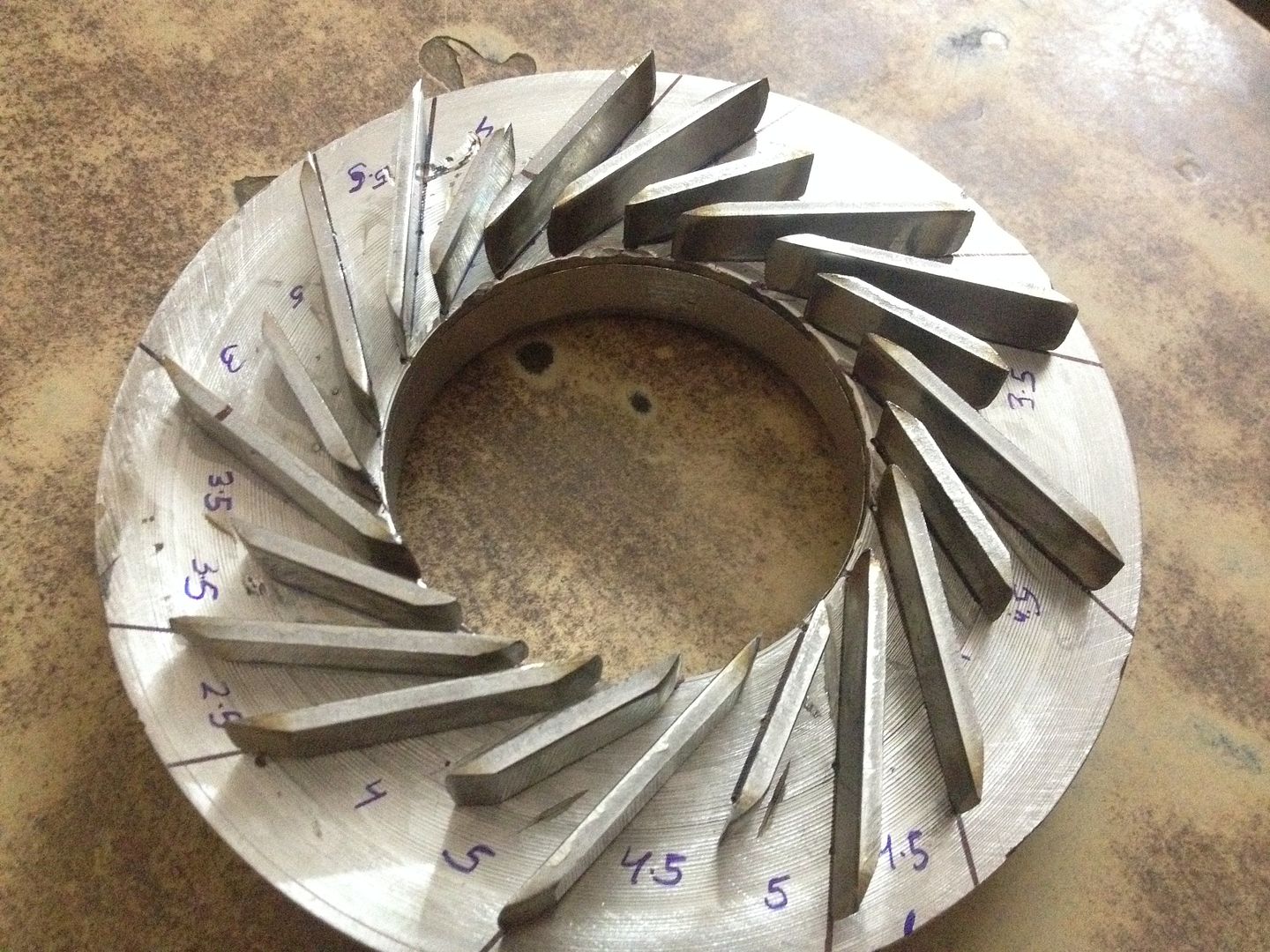 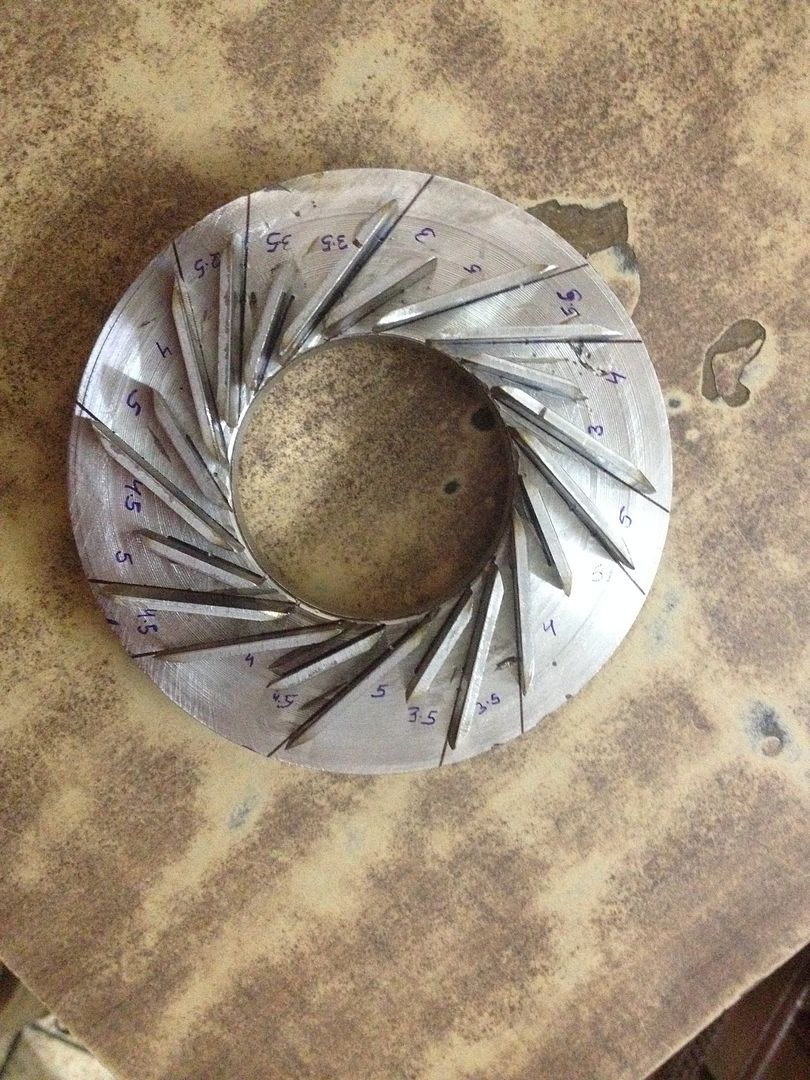 Welded and cleaned the area between the vanes with angle grinder... 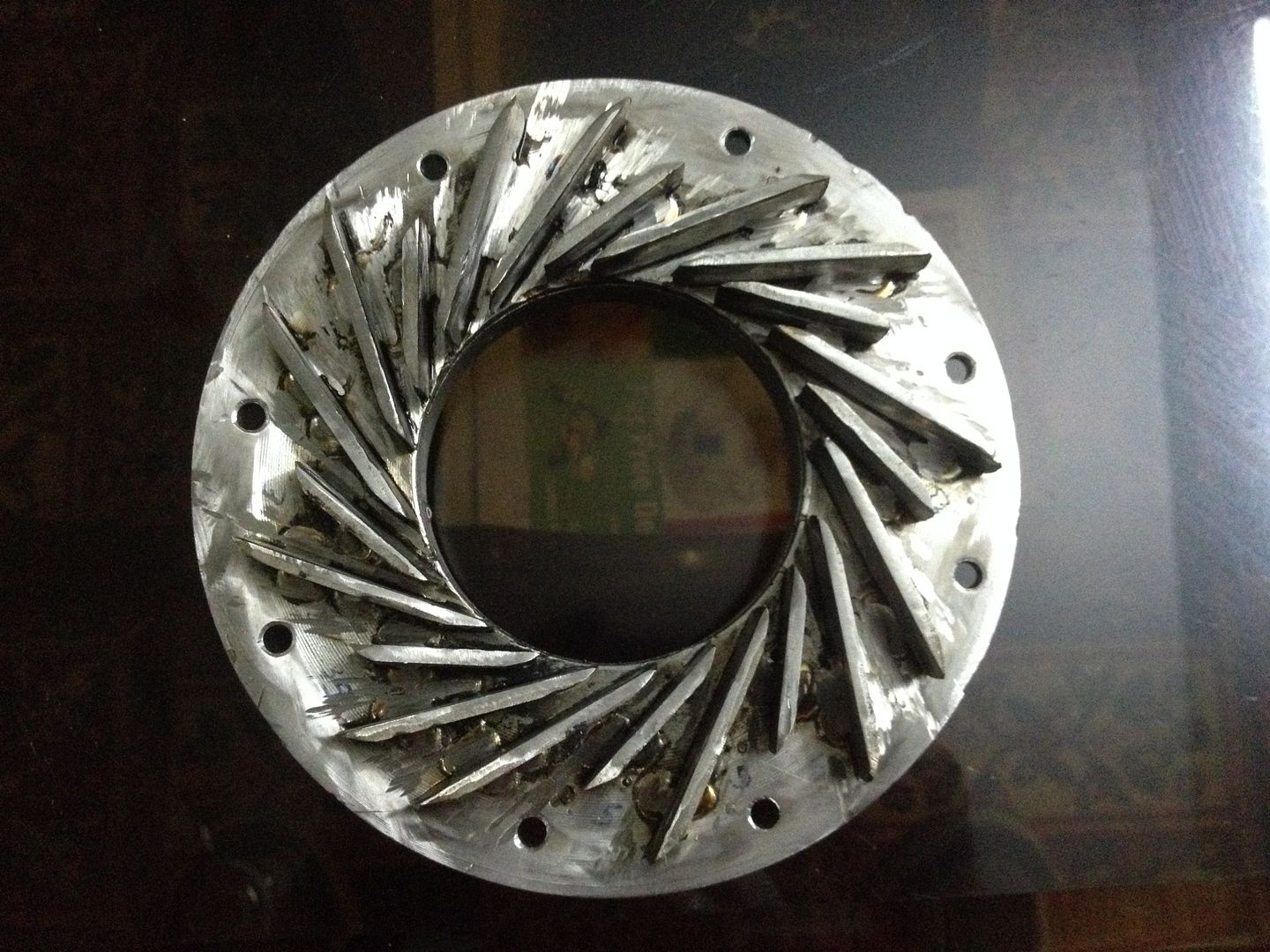 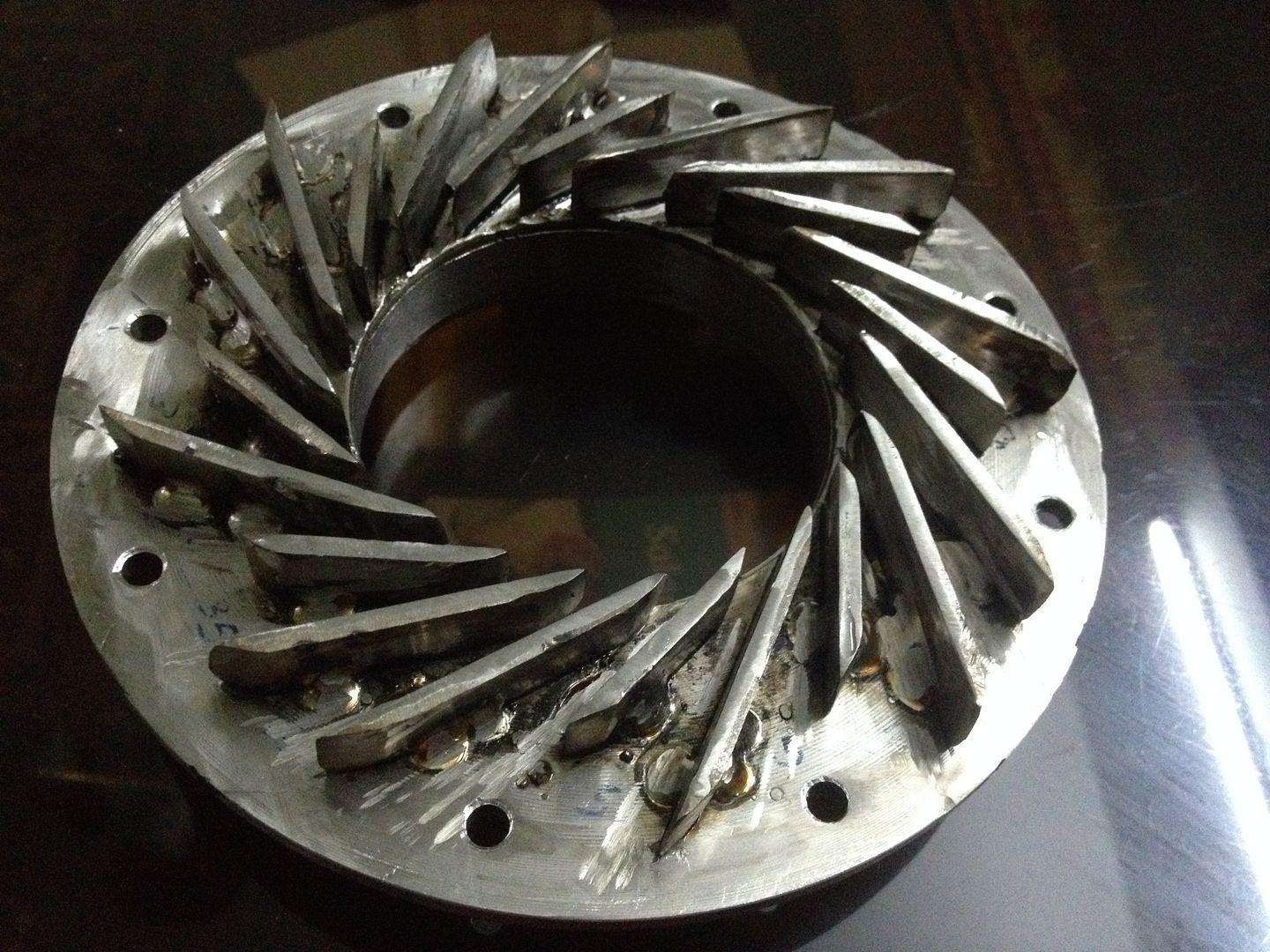 i am trying to follow modular approach as much as possible in this engine so that if at all i need to change the design of any component not working as expected later on then i can change it without any noticeable change to the rest of the fitment...The holes in the last pics are for the bolts to attach the NGV cover plate to the main NGV plate..... cheers, Patty
|
|
|
Post by madpatty on Jan 9, 2015 12:06:32 GMT -5
Fitting the completed parts together.... 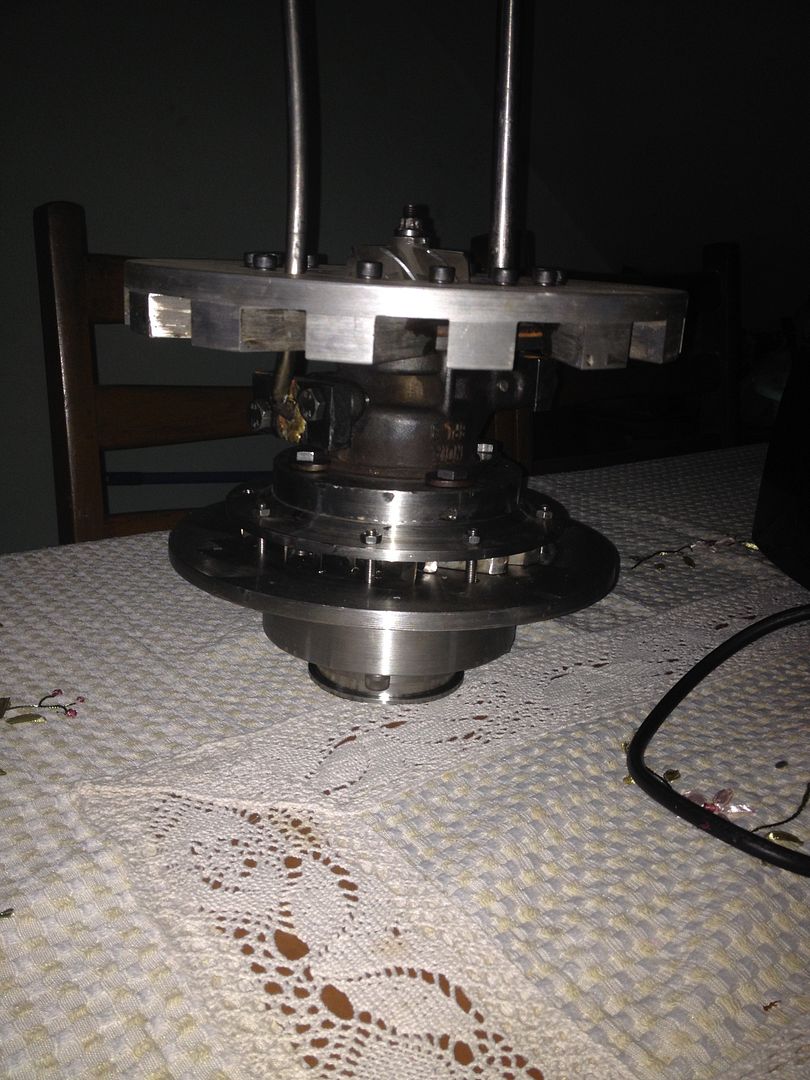 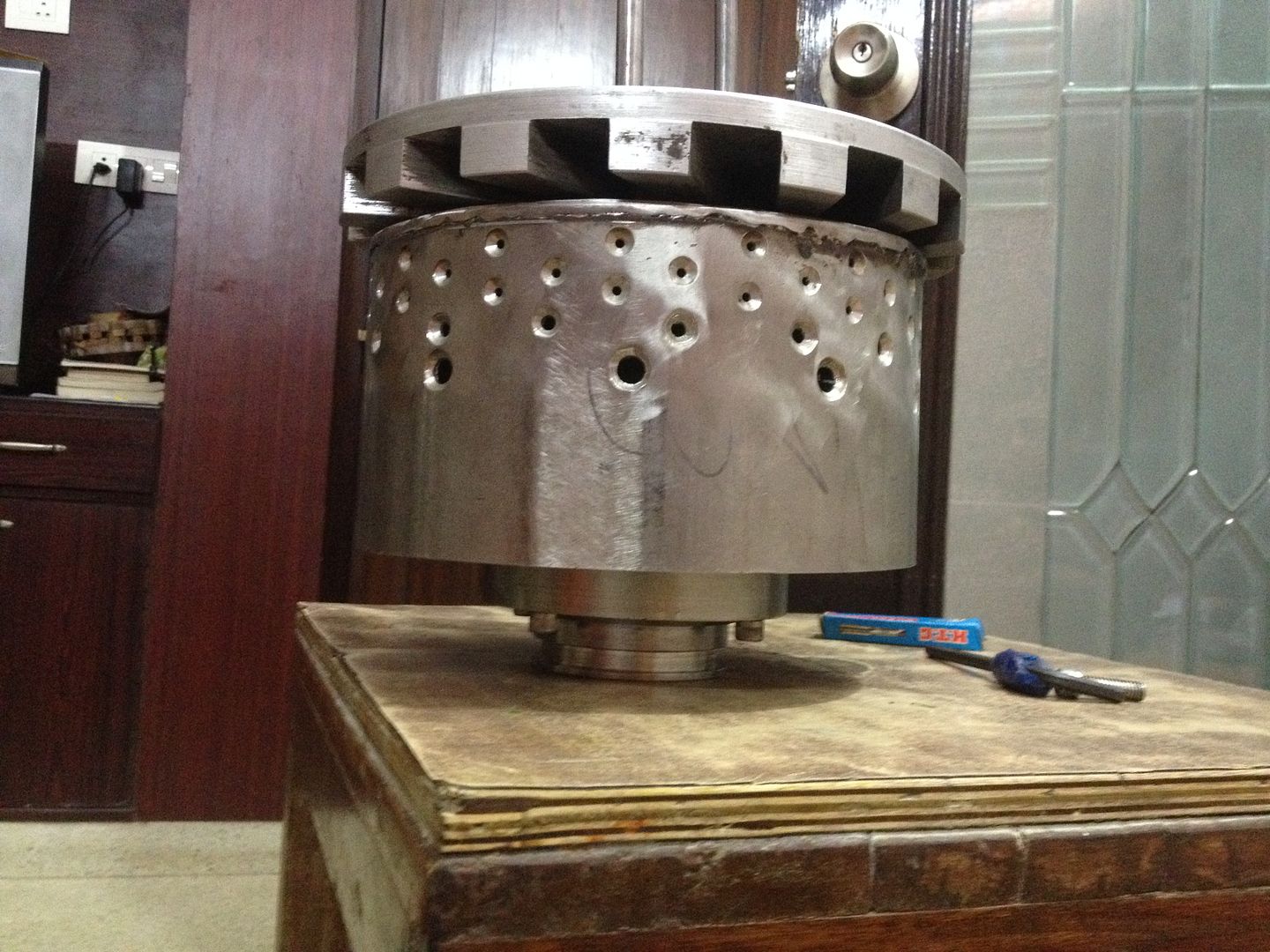 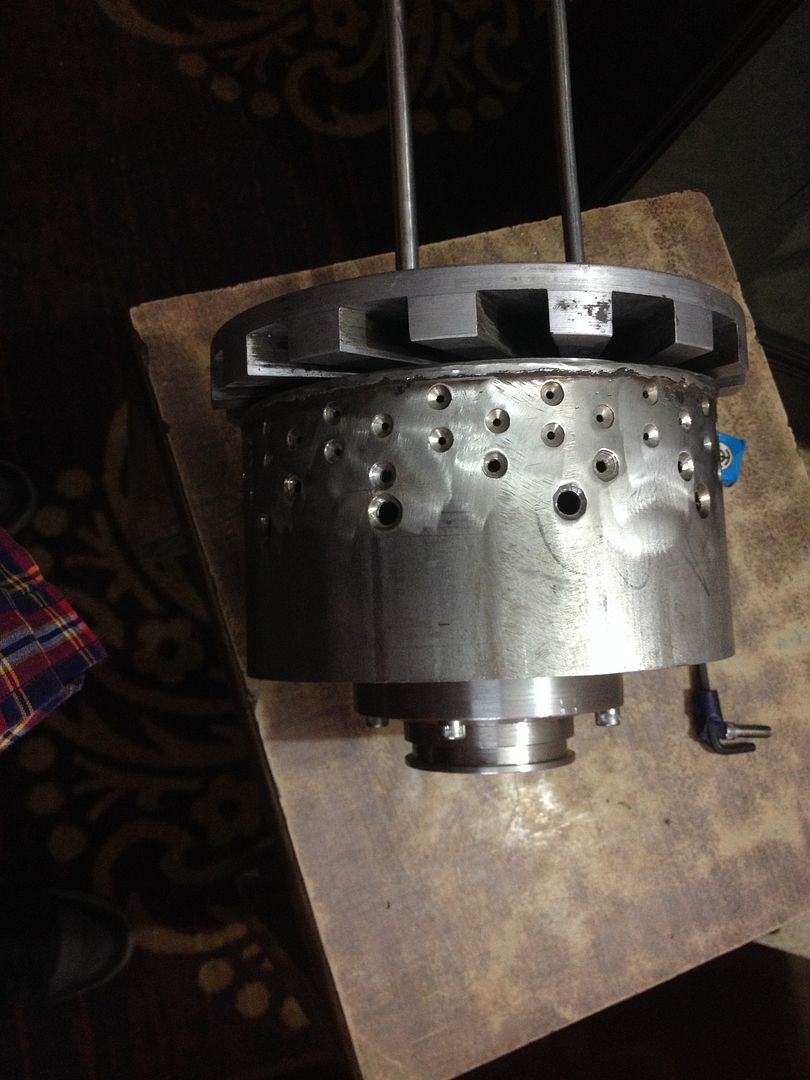 cheers, Patty
|
|
|
Post by madpatty on Jan 20, 2015 8:09:32 GMT -5
Hi Guys, The progress so far:- 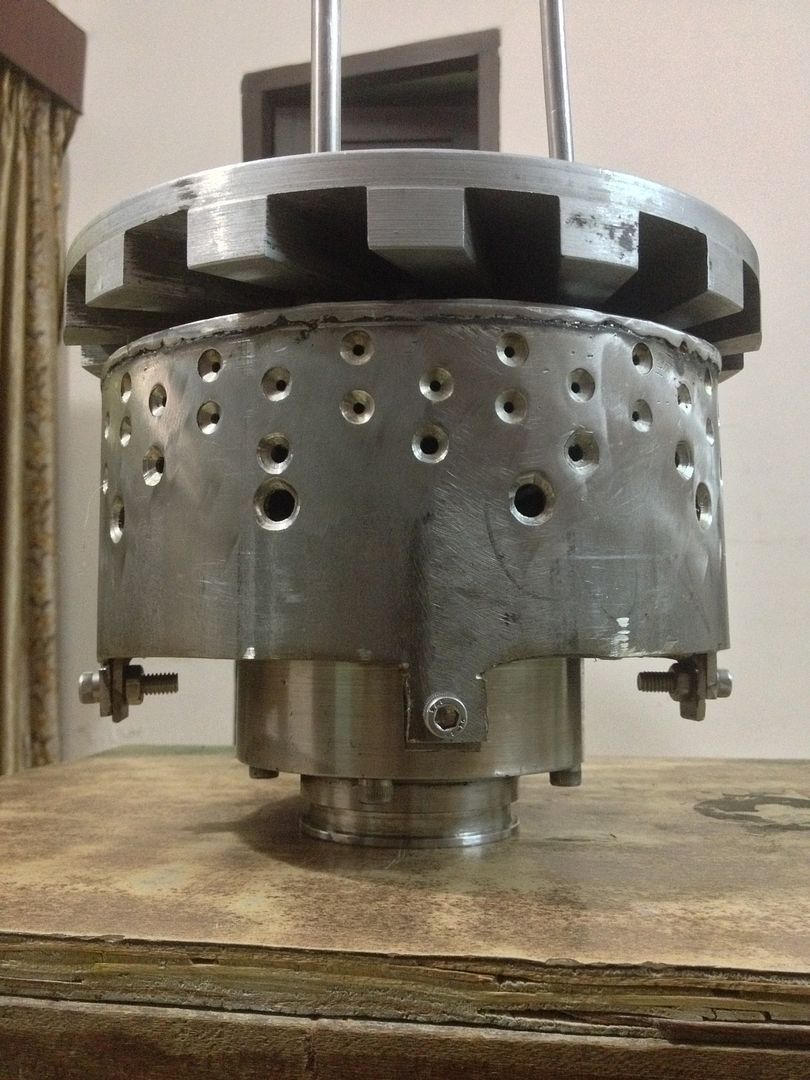  This was done in order to make the airflow smoothly transit towards the flametube..... cheers, Patty
|
|
|
Post by madpatty on Jan 20, 2015 8:20:54 GMT -5
The diffuser with corrected exit profile... 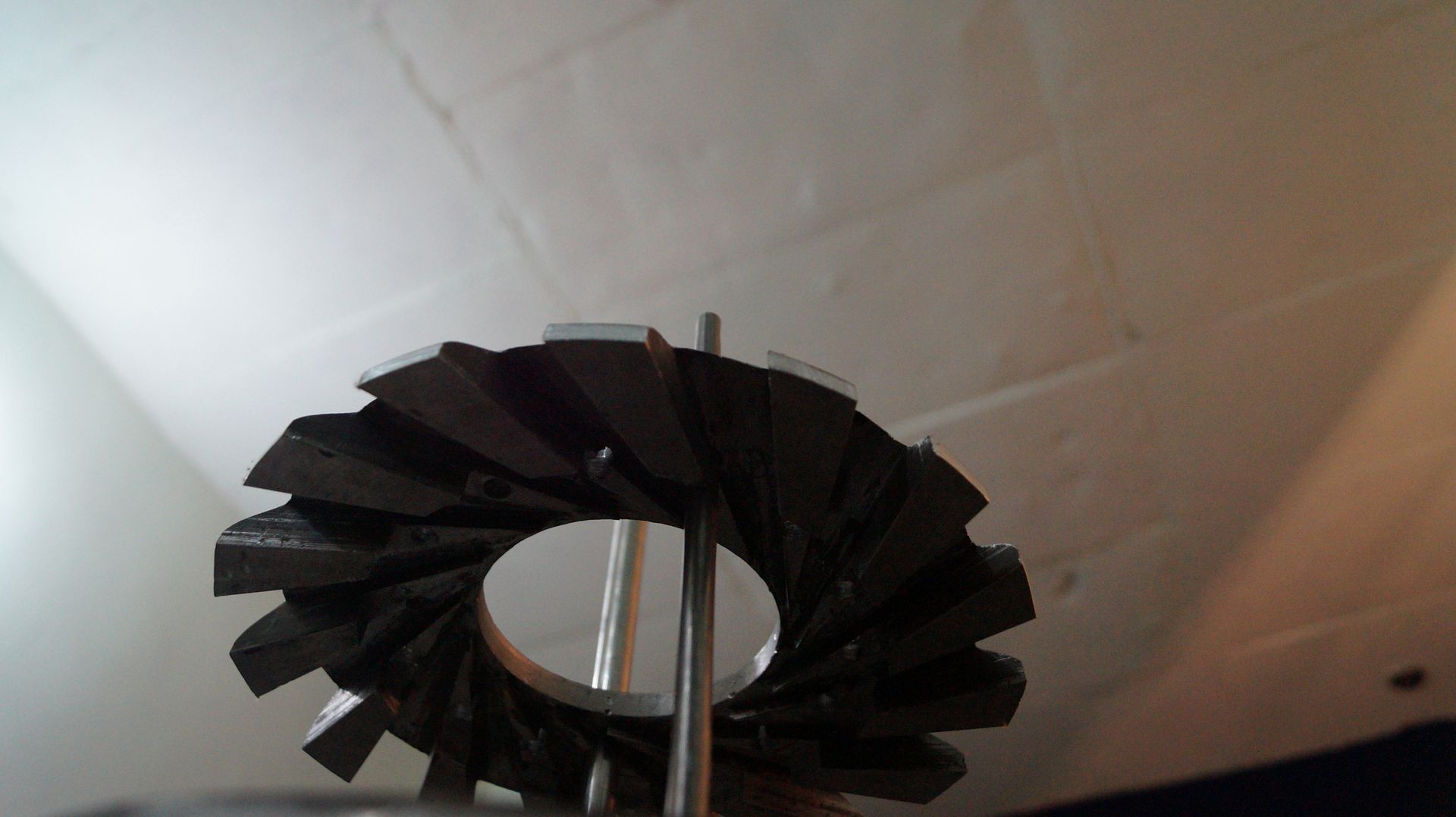
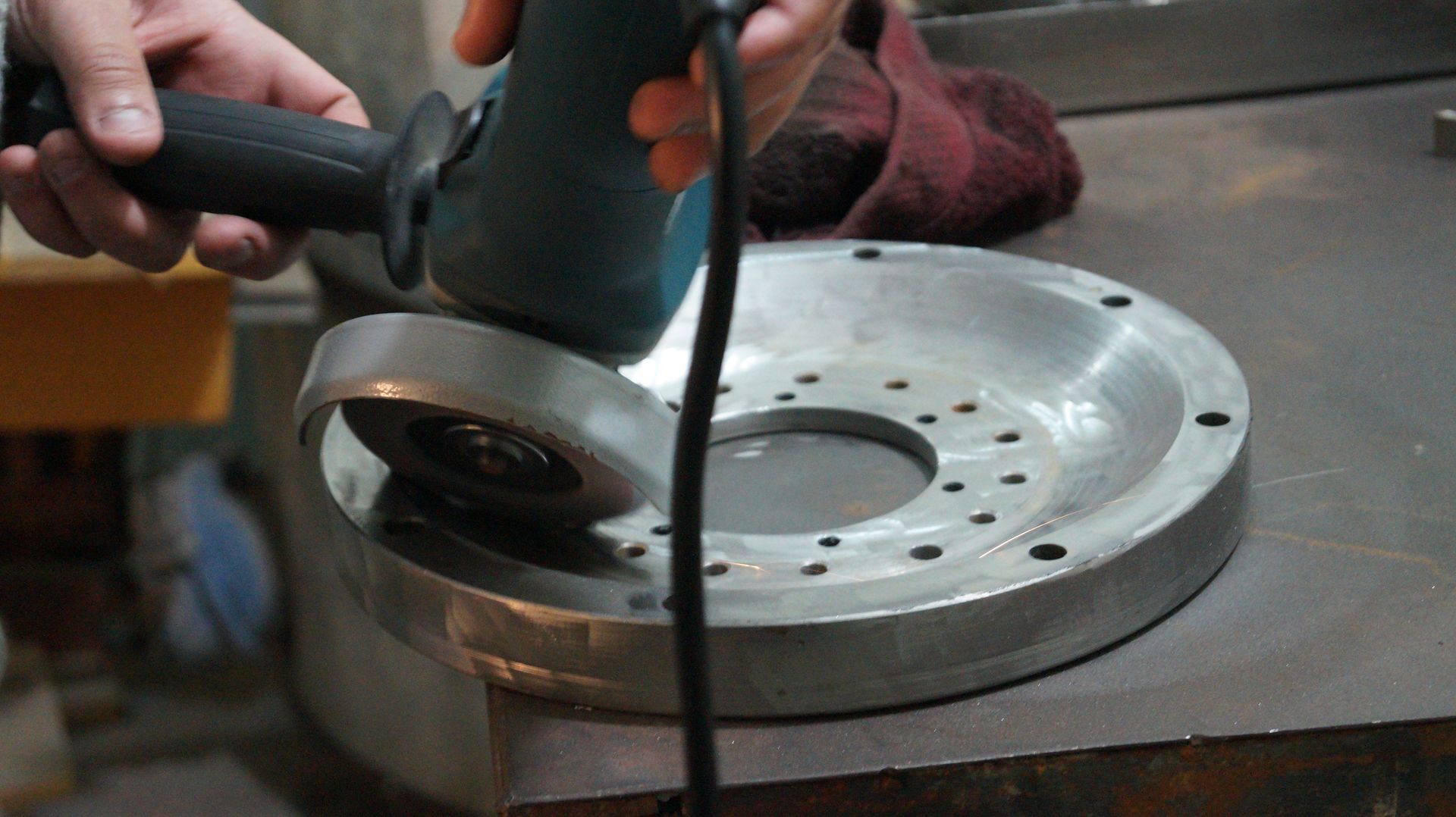 cheers, Patty
|
|
|
Post by madpatty on Jan 20, 2015 8:31:18 GMT -5
The diffuser will sit beneath this plate...  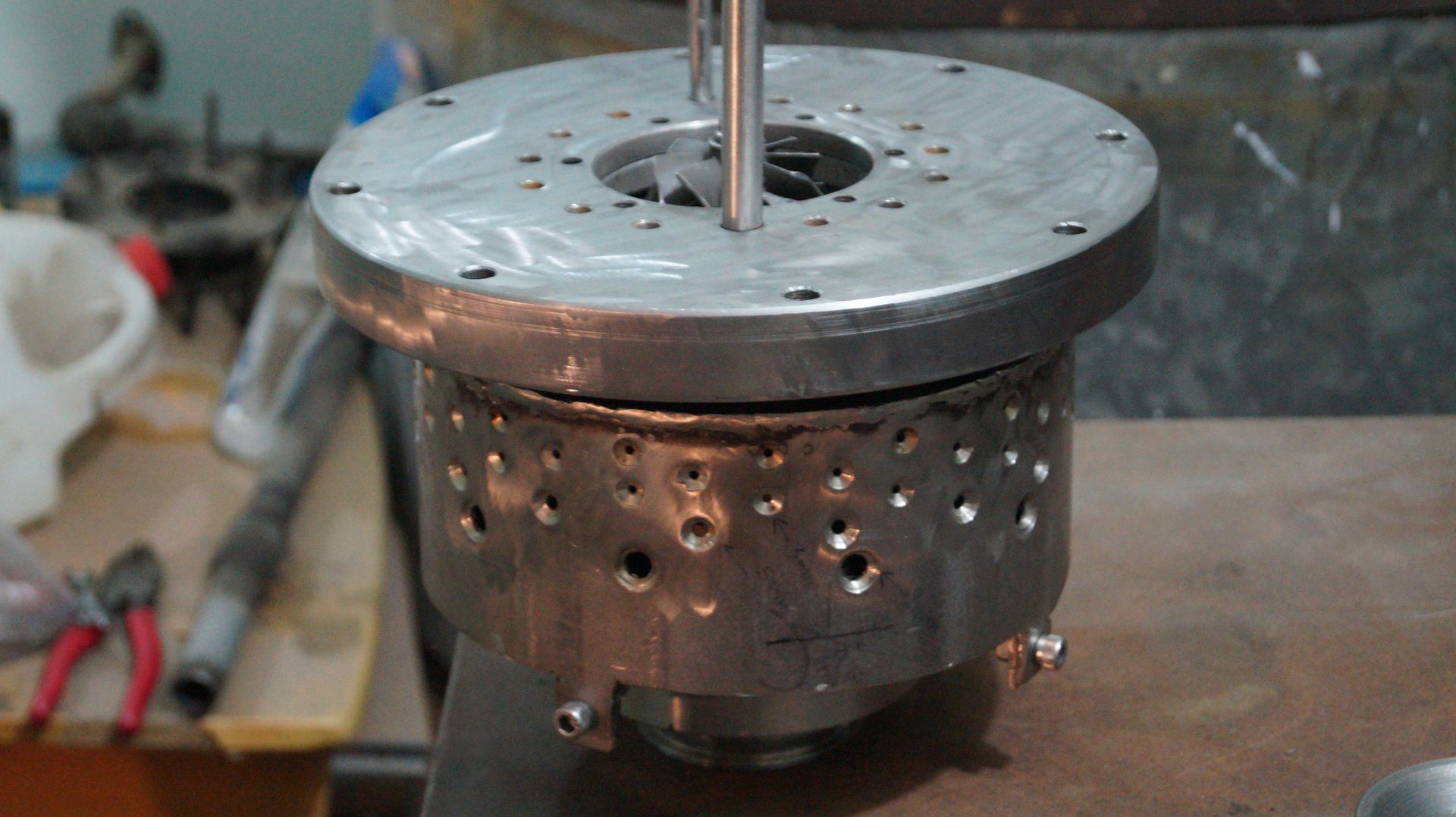 Cheers, Patty
|
|
|
Post by madpatty on Jan 20, 2015 8:33:20 GMT -5
Next job will be to make an outer casing for the engine.....
cheers, Patty
|
|
|
Post by madpatty on Jan 22, 2015 12:26:31 GMT -5
Hi Guys, Lots of things had been going with the engine in the background.....so here is the update of the build portion after where i left off in the last post..... 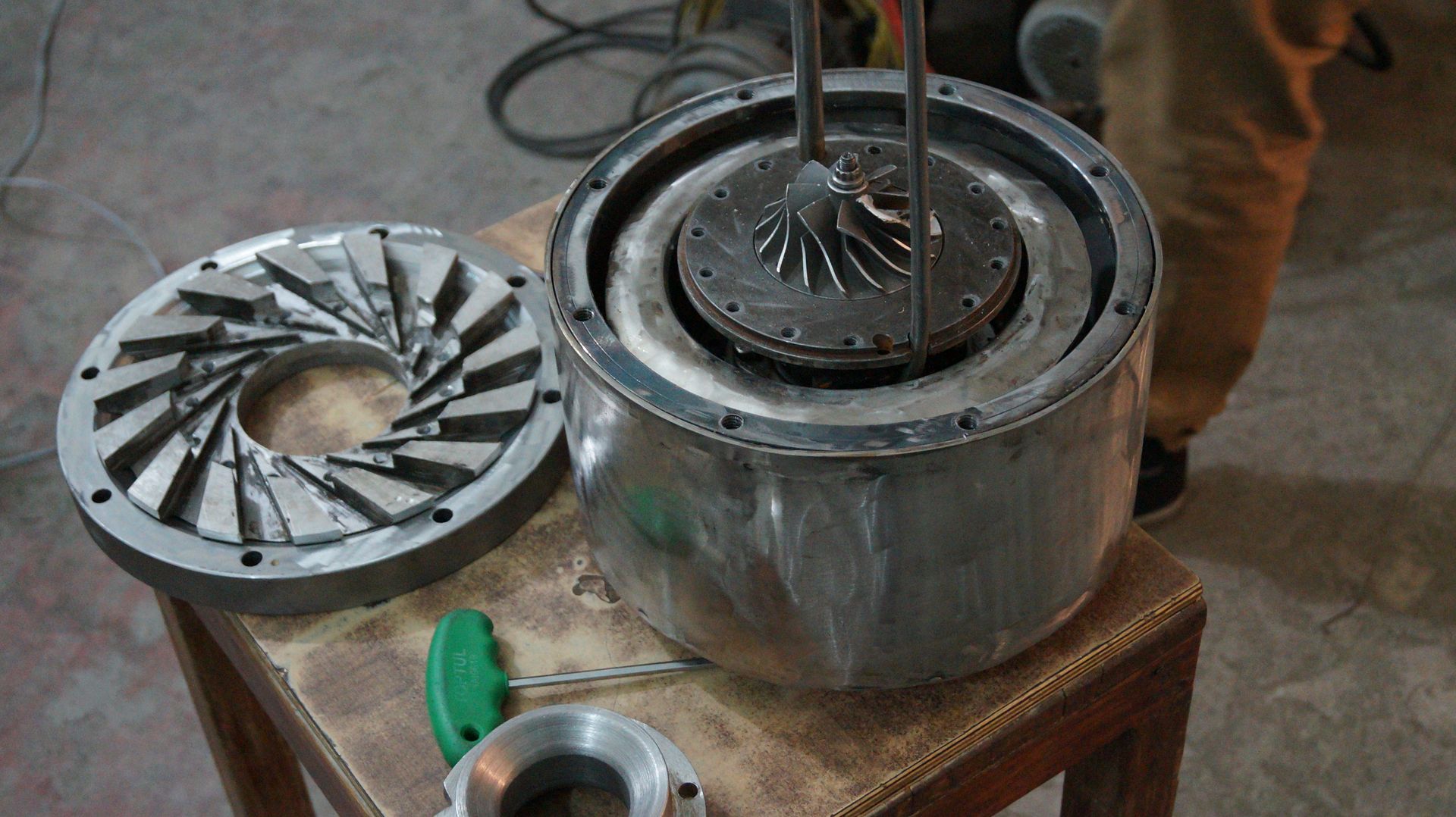 This is the outer casing of the engine....... 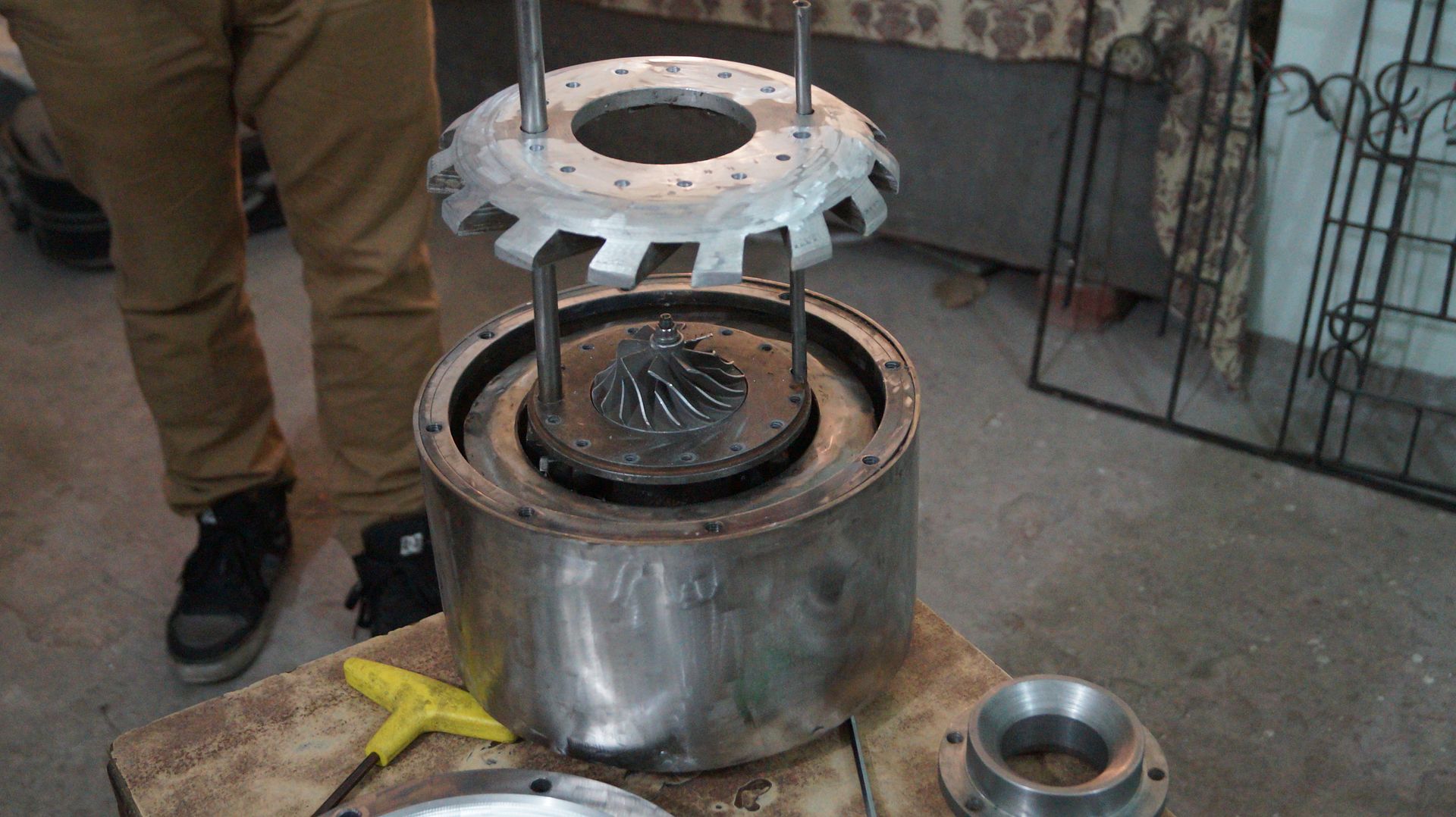 The diffuser about to be fitted.... 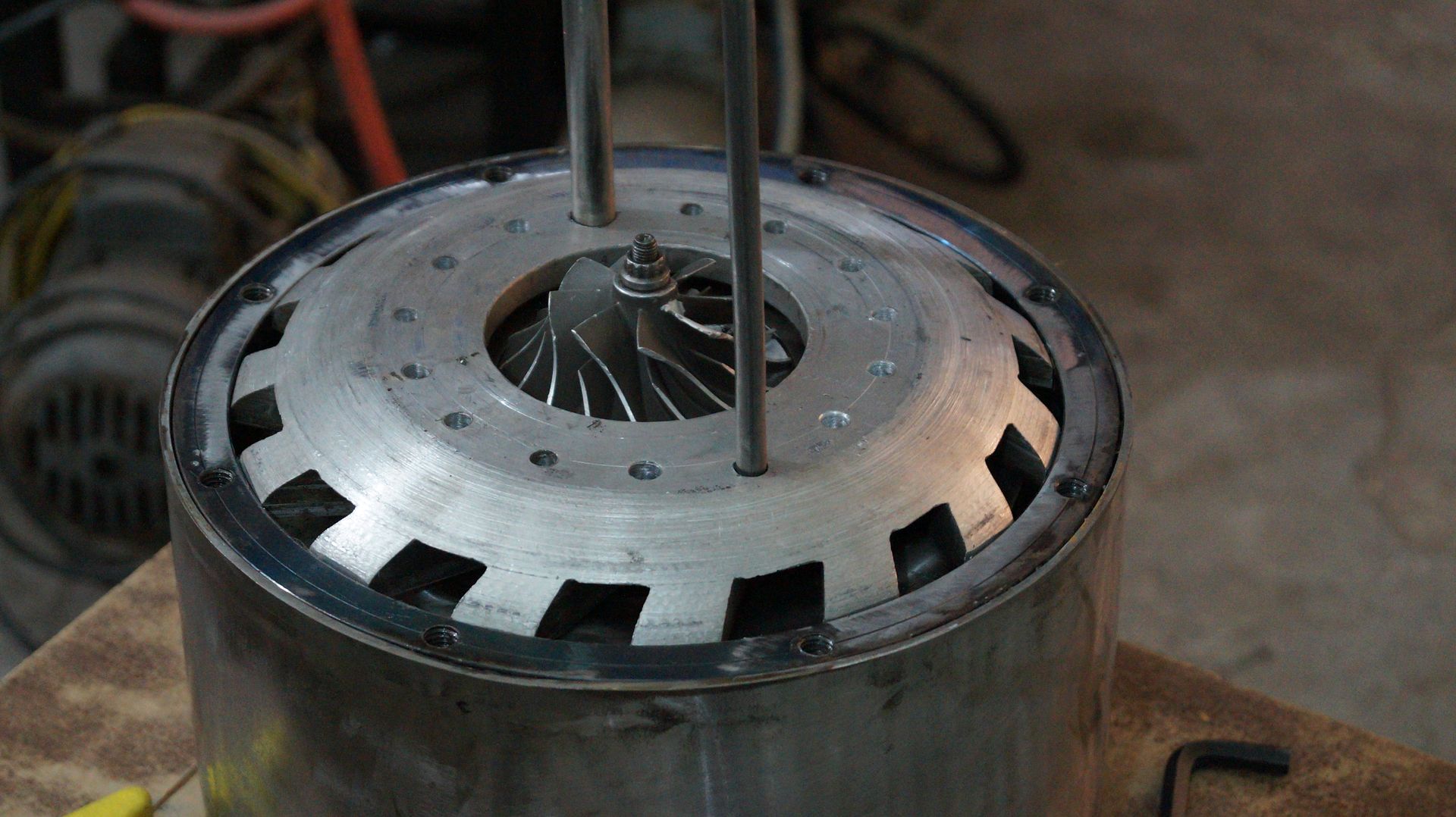 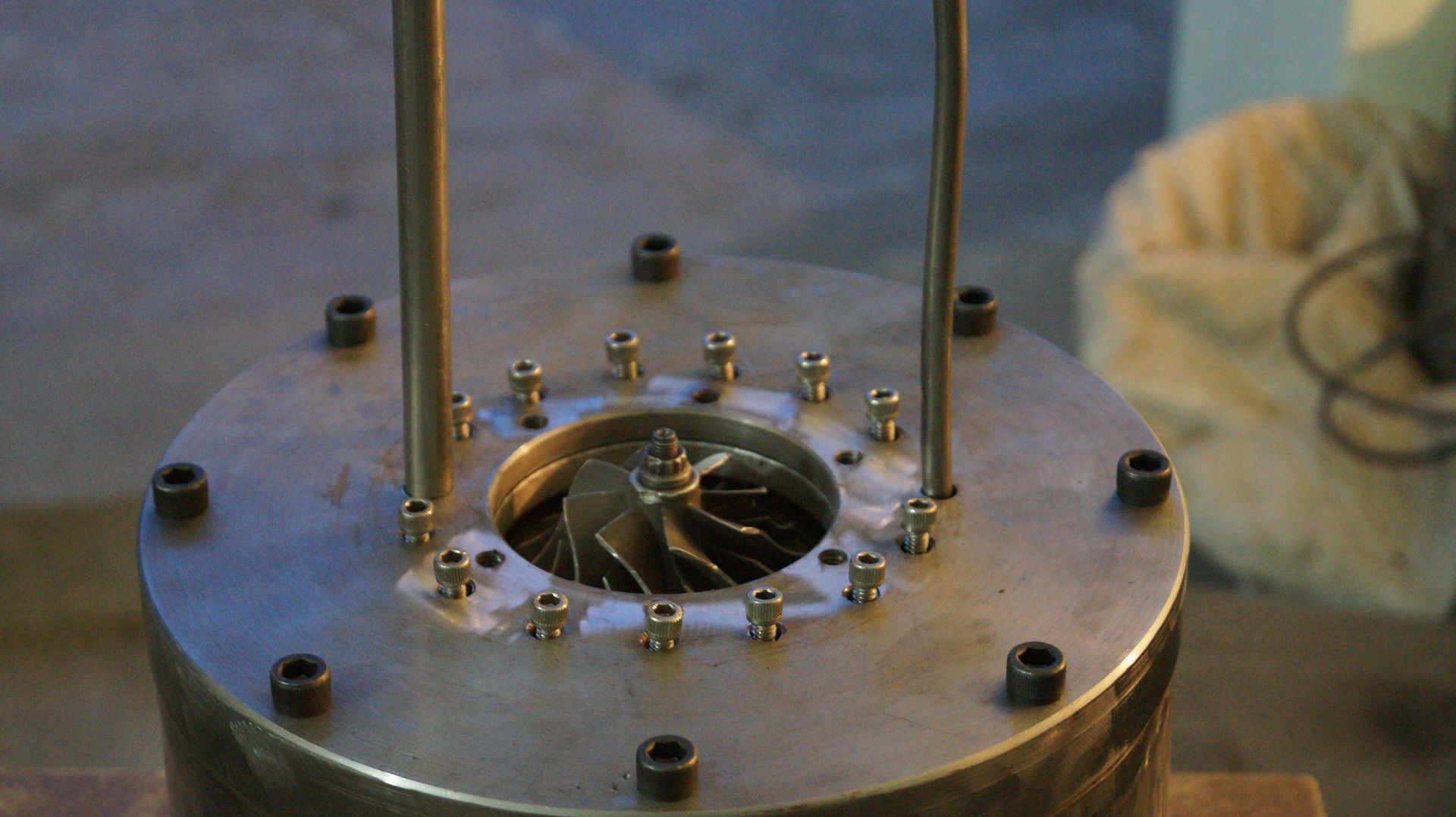 The final fitting...... 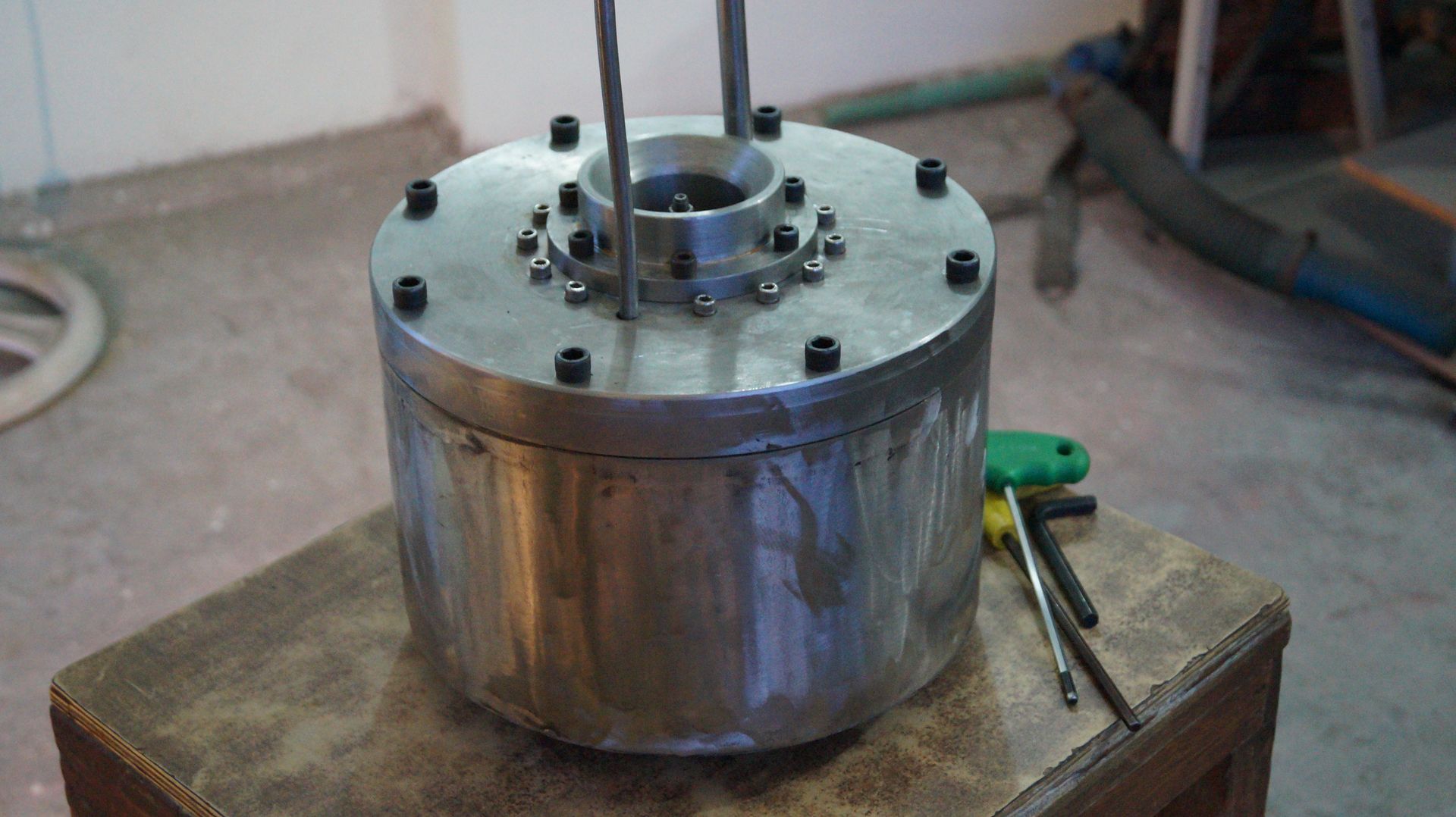 Cheers, Patty
|
|
|
Post by madpatty on Jan 22, 2015 12:28:32 GMT -5
The whole engine in parts... 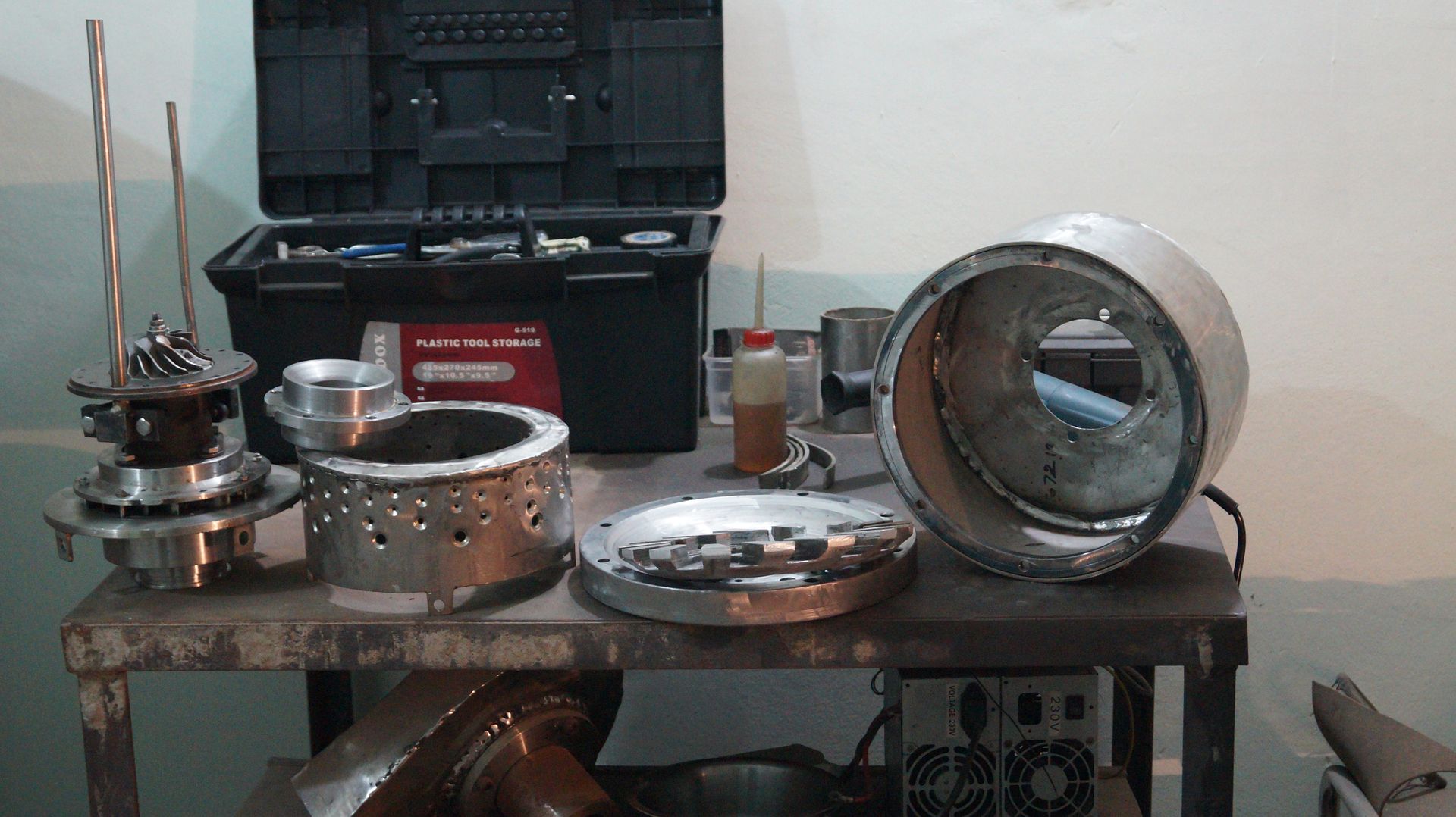 Cheers, Patty
|
|
|
Post by madpatty on Jan 22, 2015 12:34:48 GMT -5
I had already spooled this thing up successfully twice.....
The max. P2 reached was 10 psi(limited due to fuel pressure).....TOTs around 700 degrees celsius.....Oil supply pressure constant near 40 psi.....I am more satisfied because taking into consideration the massive air leakages and generous clearances i am having currently in my engine, the TOTs seem to be good enough....
Here is the video of the run 1 :-
Cheers, Patty
|
|
|
Post by madpatty on Jan 22, 2015 12:56:37 GMT -5
The video of Second Run:-
The Temperatures were almost same but camera showing turbine blade colour towards a slight darkish tone...i tried removing some leakages using a RTV silicone gasket gel but it was blown apart from even small spaces when the engine started making some P2...
cheers, Patty
|
|
sven
Veteran Member
 
Joined: February 2012
Posts: 102
|
Post by sven on Jan 22, 2015 13:14:00 GMT -5
Nice run, you should turn propane bottle upside down to get more fuel,(liquid propane). Then you dont need to boil water 
|
|
|
Post by madpatty on Jan 22, 2015 13:19:53 GMT -5
Hi Sven, It will be a bit daring task to do that atleast for me...because last time i did it i got a huge flame out of my previous engine...but i will surely try once....
Cheers, Patty
|
|
|
Post by finiteparts on Jan 22, 2015 21:03:47 GMT -5
Hey Patty,
That is looking much better! Glad to see it running well for you. Where are you getting leakage? At the oil and fuel inlet tubes/front case?
Also, where are you measuring your P2? I want to make sure you are measuring the P2 downstream of the diffuser discharge...
That's with the larger compressor wheel, right?
Congratulations again on the good runs!
Chris
|
|
rythmnbls
Veteran Member
 
Joined: August 2011
Posts: 145
|
Post by rythmnbls on Jan 22, 2015 21:15:19 GMT -5
Congratulations on the run ! glad to see you finally get it sorted out.
Regards.
Steve.
|
|