|
Post by racket on Mar 10, 2015 15:55:57 GMT -5
Hi Ian
How do you intend coupling the freepower shaft to the gearbox input pinion shaft ??
Alignment will be critical .
My personal thoughts would be to remove the compressor wheel and try to mount the pinion gear onto the comp shaft and fit the driven gear to the housing someway , we've discussed a similar sort of setup when using a turbocharger for a freepower
Cheers John
|
|
|
Post by frankenhealey on Mar 11, 2015 8:06:26 GMT -5
Hi John,
The gearbox has a hollow input shaft and the output shaft will connect to a modified propshaft coupling. I'd be looking to modify the freepower shaft to fit the gearbox input 1" bore.
Cheers,
Ian
|
|
|
Post by racket on Mar 11, 2015 15:58:03 GMT -5
Hi Ian
Could you post a Link to the gearbox so we can check it out please .
A splined coupling will work , but the freepower rpm will need to be seriously considered when deciding the final setup .
LOL..............the hairs on my butt are starting to warn me something doesn't quite feel right , ...............more info please , pics would help greatly
Cheers John
|
|
|
Post by frankenhealey on Mar 11, 2015 17:07:17 GMT -5
|
|
|
Post by racket on Mar 11, 2015 23:07:35 GMT -5
Hi Ian
Ah , the good old Noram gearbox , I've got one of those in my shed , purchased it with a view to using it on a freepower wheel turning 32,000 rpm .
Theres a problem with this gearbox for high speed use , its a two stage reduction and the "intermediate" shaft doesn't run on ball bearings but a bushing if I remember correctly , I was contemplating using pressure lubrication to the bush .
Theres considerable work required to turn the gearbox into one suitable for a turbine engine, thats why mine is still packed away as I felt it was more work to modify than build my own .
Cheers John
|
|
|
Post by frankenhealey on Mar 12, 2015 15:46:15 GMT -5
John, Nothing new on this forum then?  I might just buy the Noram to see how easy or not it is to modify. Luckily I can use all the machinery at work. Cheers, Ian
|
|
|
Post by racket on Mar 12, 2015 20:34:43 GMT -5
Hi Ian
LOL.....occasionally ;-)
I'd really like to see your "compressor" end with the wheel removed to see how/what needs doing, to be able to contribute another 2 cents worth
Cheers John
|
|
|
Post by frankenhealey on Nov 2, 2015 17:26:09 GMT -5
And we're back in the room. Due to various external factors I've not been as active on the SpridJET as I would have liked. Catatonic is probably a better description. However hoping to move on, I think I may have found another gearbox solution and I'm currently in discussions with the manufacturer. On another note I definitely have Turbinitus 'cos I picked these two last week. The turbine twins. Tweedleboom and Tweedlewhee. 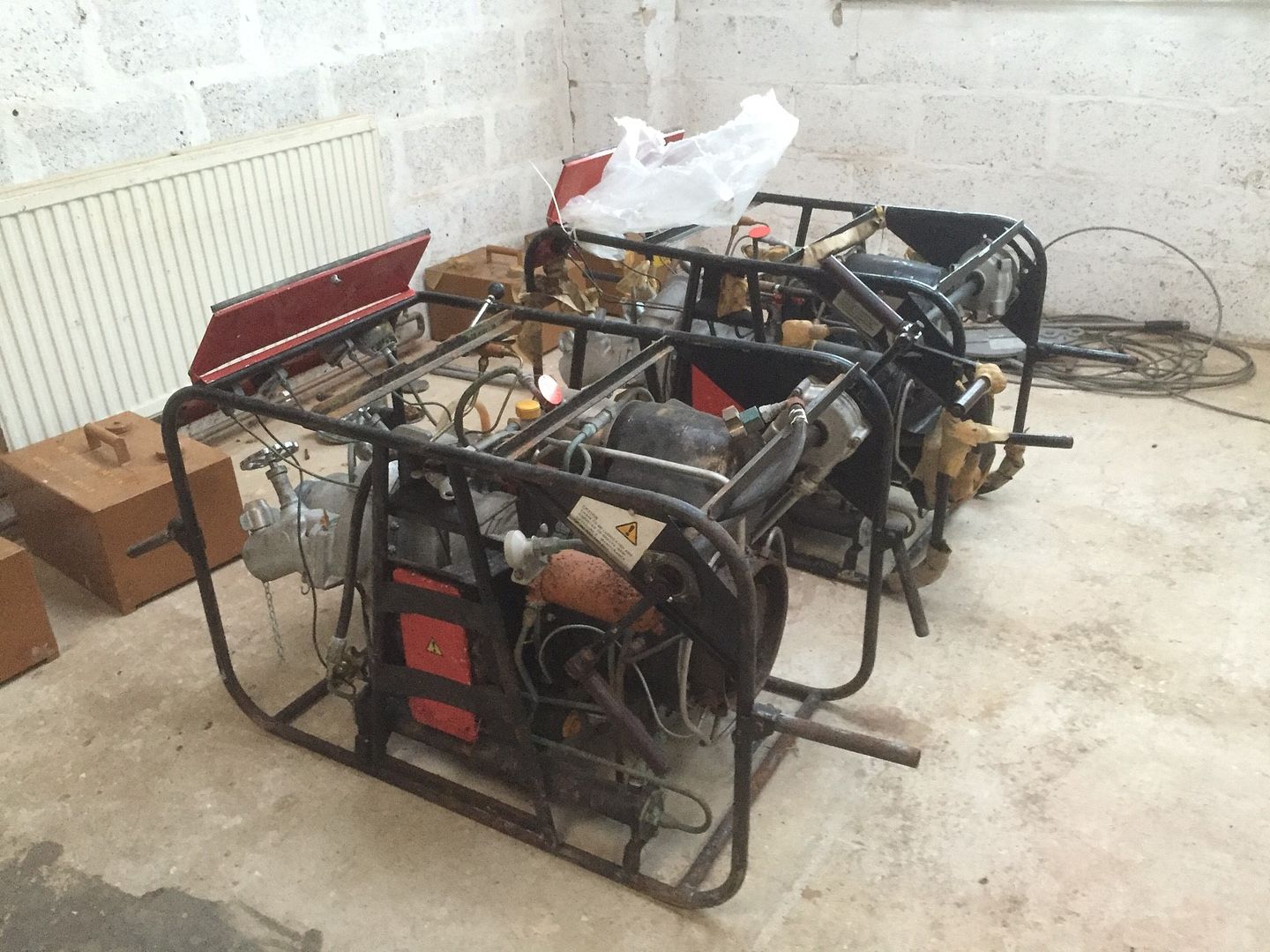 The uninhibited one. 1.45 hours on the clock since last overhaul but with no paperwork so could have been anything from 20-50 years. Note the corrosion but generally seems to be all there. 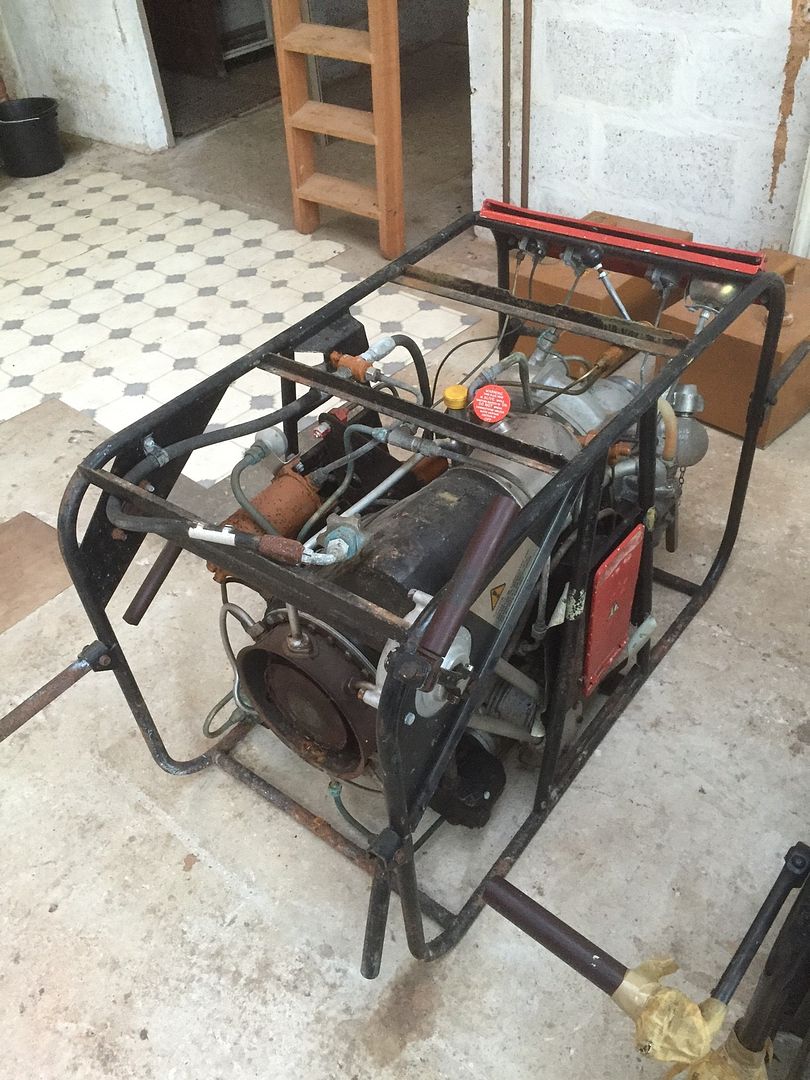 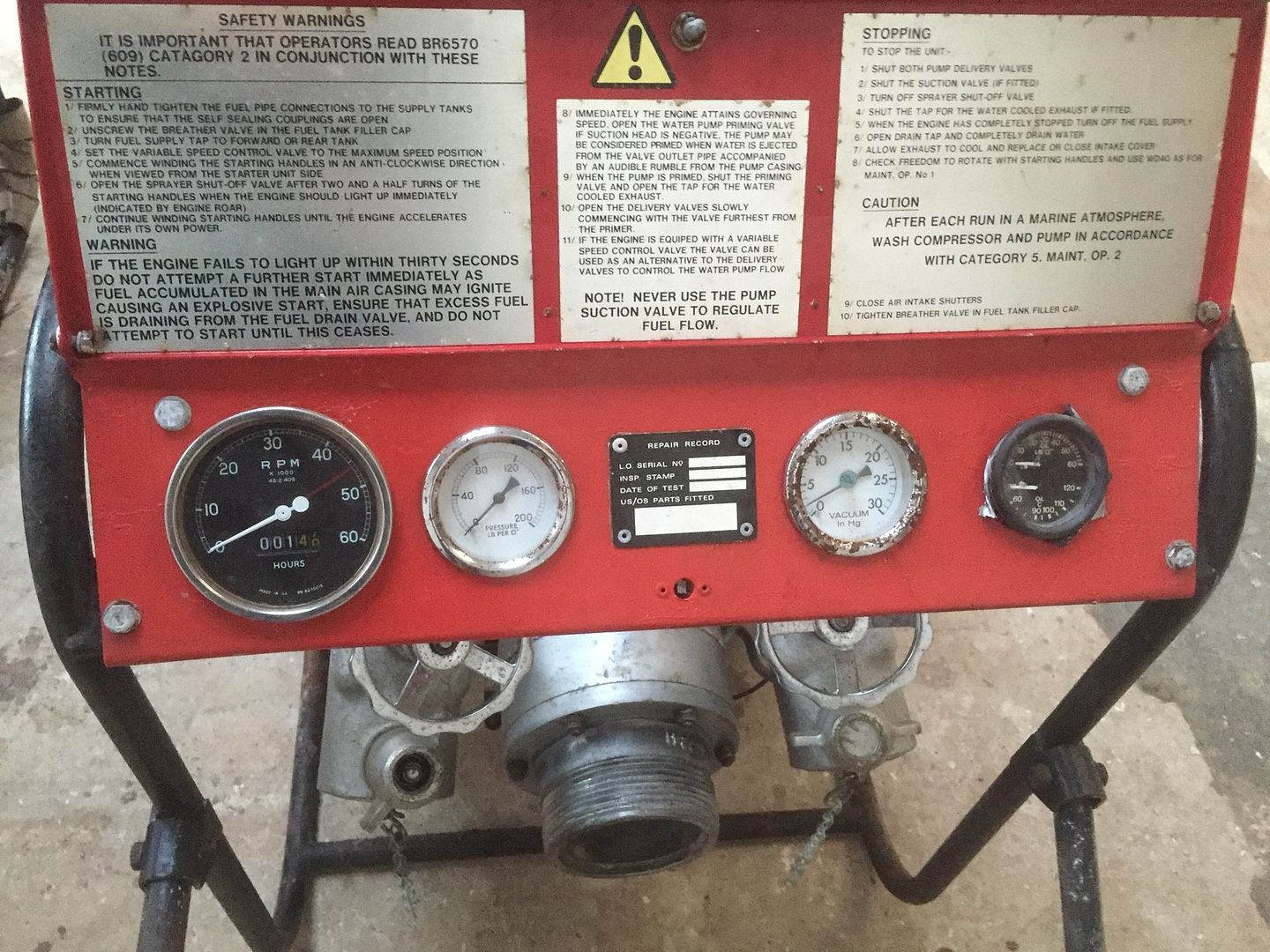 The inhibited one. Already missing the chain drive for start but I can cannibalise the other for these non-essential parts. 7.45 hours on clock from last overhaul but this one does have papers and was last in serviced in 1993. 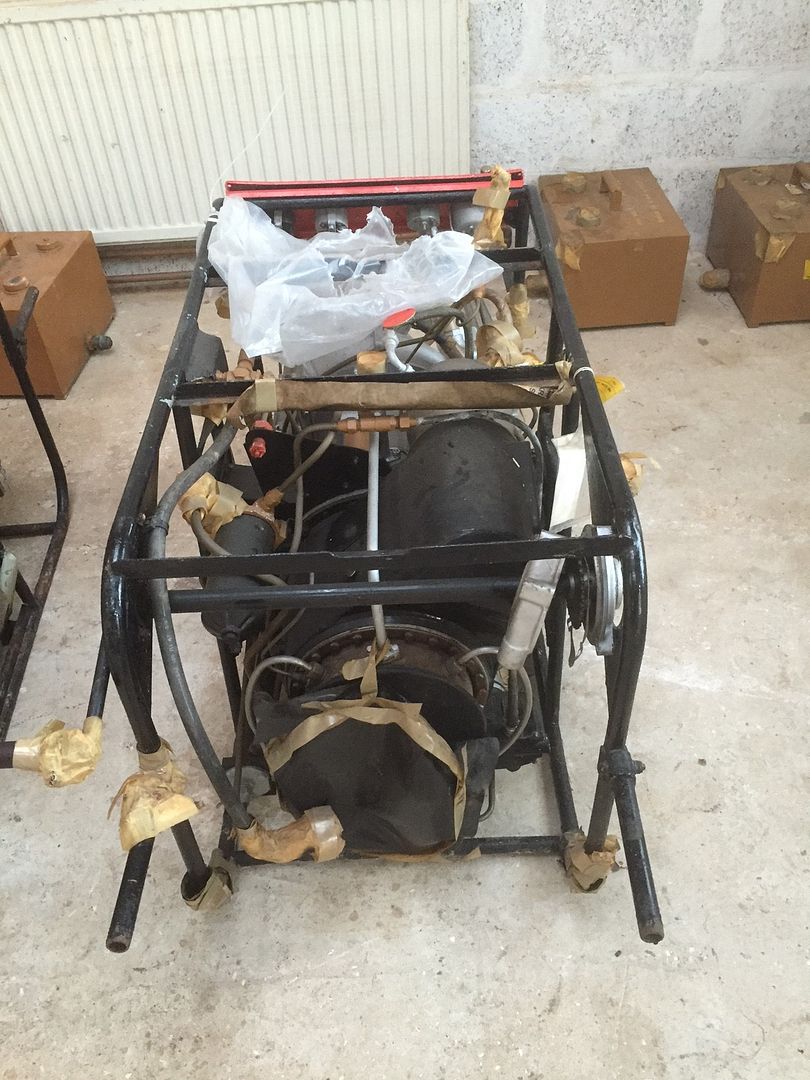 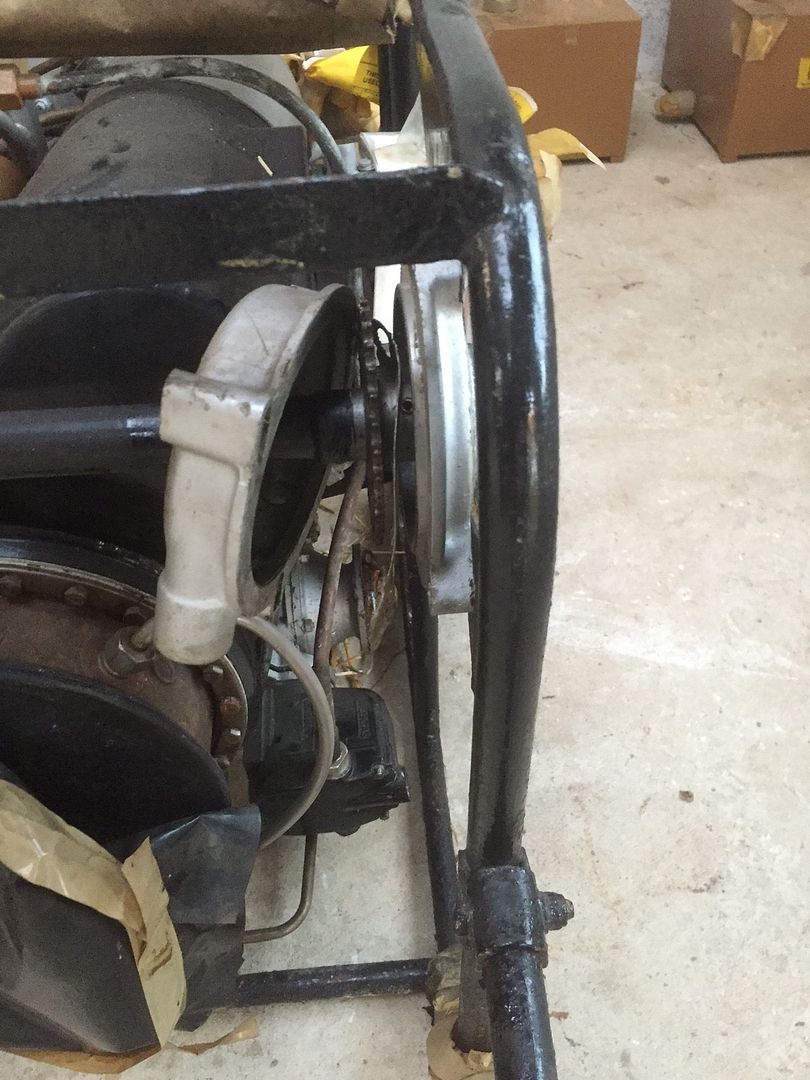 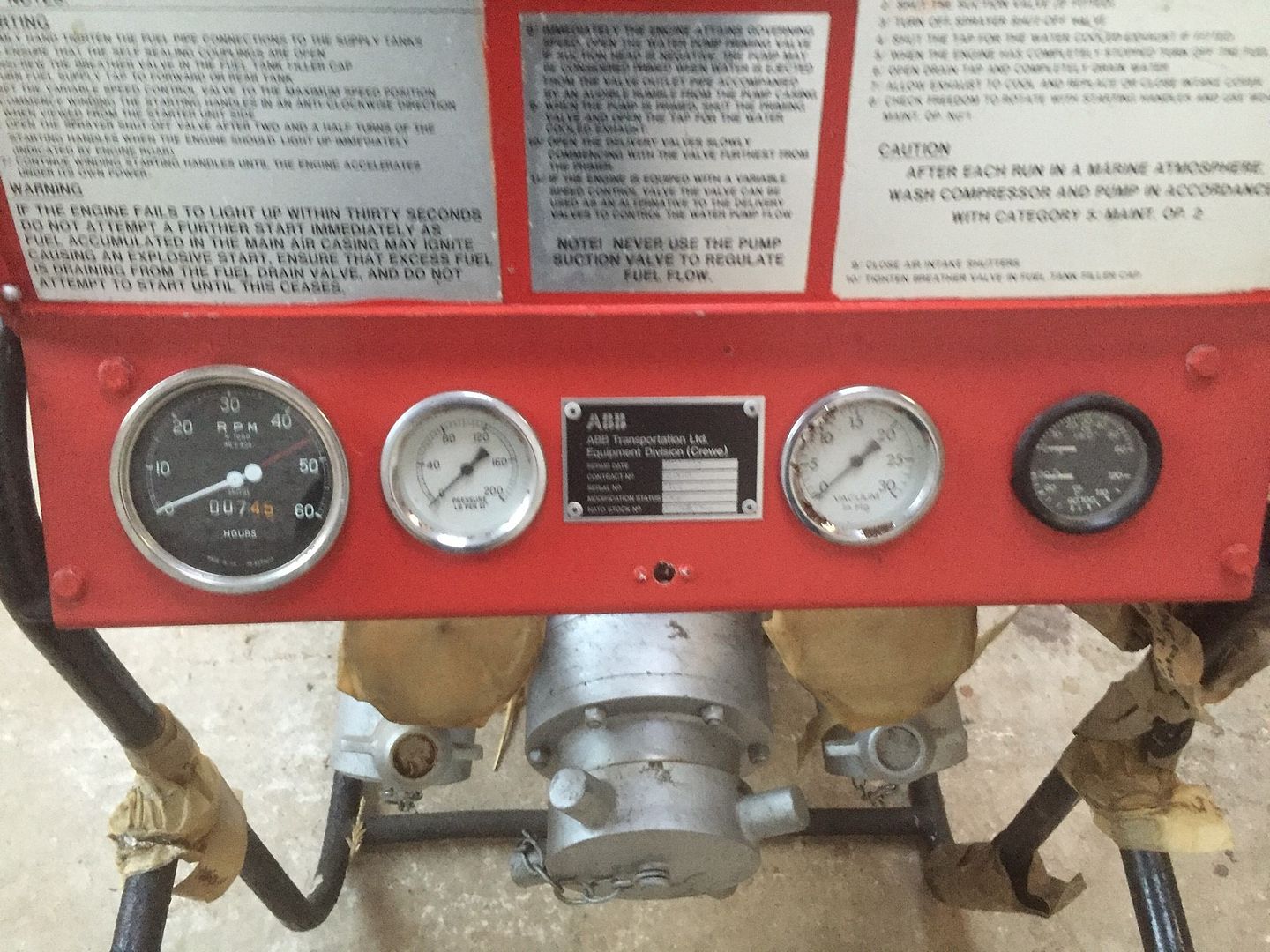
|
|
|
Post by racket on Nov 2, 2015 18:03:40 GMT -5
Nice :-)
1S/60 fire pumps ??
|
|
|
Post by frankenhealey on Nov 3, 2015 7:46:33 GMT -5
Nice :-) 1S/60 fire pumps ?? Yep, they'll give me something to play with when the bodywork of the SpridJET is being done. Plan is to restore the inhibited one to active status as I've got about 3 uses for a 400gpm turbine pump and I'd like to sling the other 1S60 in a motorbike or airboat or something.
|
|
|
Post by frankenhealey on Nov 17, 2015 16:41:17 GMT -5
This weekend I got a few hours on the Rover pumpsets and the SpridJET. The job at the moment is to strip the roller shell so it can be blasted and the rust repairs started. Today after finishing what i could on the pumpsets I got started. This is how it started.  Wiper motor and wheelboxes out, bonnet hinges removed, boot lid removed, screen removed, dash and instruments removed 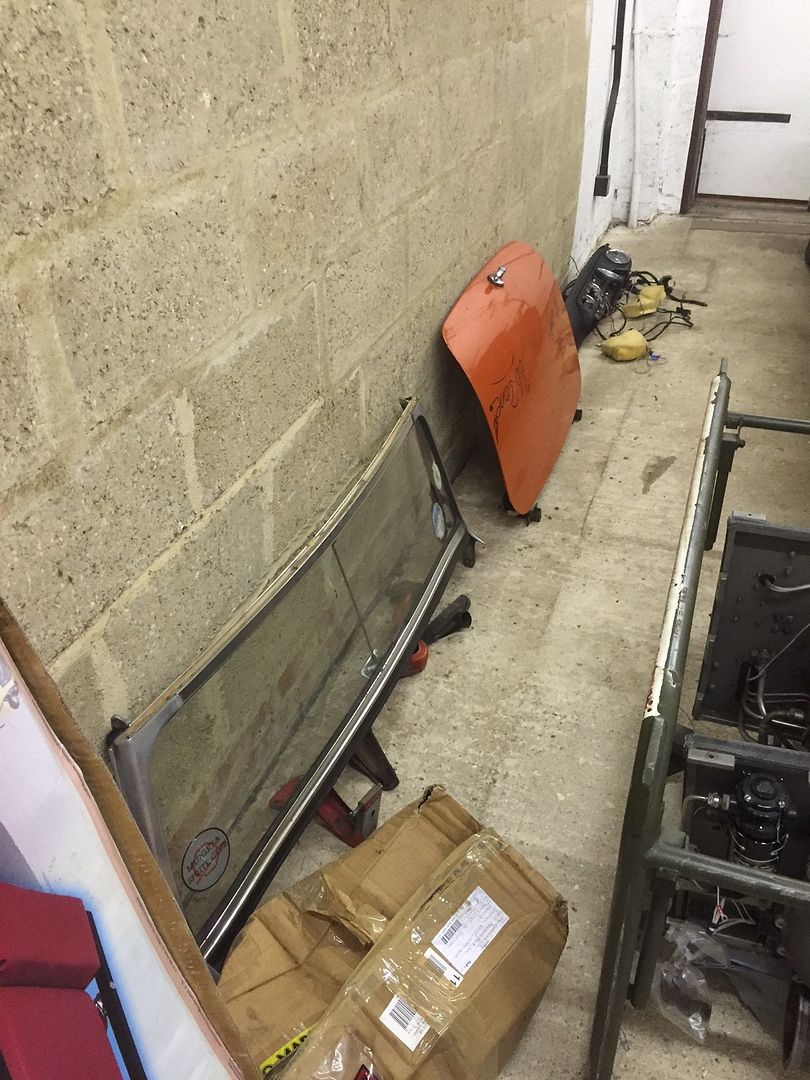 How it was left  Over the next few weeks I'll strip the rest of the shell and make a roller frame for the shell and while that's away being stripped and blasted I'll get on with renovating the running gear. Think we have a possible candidate for the reduction drive off the back of the turbine. It's an aluminium cased 5.33:1 single stage box that will get some uprated bearings with forced lubrication and probably a small oil cooler. The reduction will give 8630 rpm giving a theoretical 147mph for starters. Just waiting for the input/output shaft centres and weight to be confirmed. 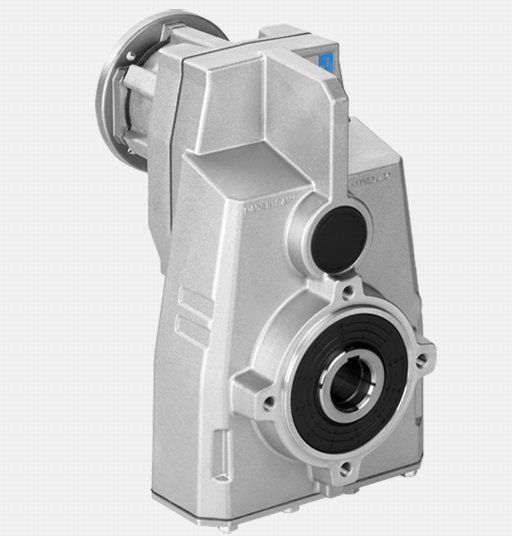
|
|
|
Post by racket on Nov 17, 2015 19:14:42 GMT -5
Hi Ian
Whats the gearbox off , more details please as suitable ratio boxes are extremely hard to find , especially lightweight ones
Cheers John
|
|
|
Post by frankenhealey on Nov 18, 2015 5:16:35 GMT -5
Hi John,
After we discussed the mower box I searched and searched and .... well you get the idea.
One of our suppliers does these shaft mounted speed reducers (http://www.chiaravalli.com/eng/worm-gears.php in a PDF about two thirdsy down the page) but they're cast-iron cased. The advantage is all the parts can be bought as spares.
Then I came across one of their competitors here (http://hydromec.com/products/compact/) and they looked a lot more what I was looking for. I got a price on the FC81 of the range and that was £700 GBP approx plus VAT so I'm currently looking at a smaller one.
Any comments gratefully received.
Cheers,
Ian
|
|
|
Post by frankenhealey on Nov 18, 2015 11:30:07 GMT -5
Small gearbox specifications  
|
|
|
Post by racket on Nov 18, 2015 22:38:18 GMT -5
Hi Ian Are they a single stage or two stage reduction ?? Does your setup need a particular rotation direction for the diff vs the freepower output ? I just found these which look interesting www.hubcityinc.com/SingleReductionParallelShaftDrives.html bit heavy in cast iron, but big HP capability :-) Shame they're in the US Cheers John
|
|