Arrrrgh! I forgot about this build thread and posted the JU-02 build updates in the landspeed bike thread instead, bugger!
Oh well, here is the interesting stuff so far:
Last night I made a pair of suitable sized flasks for the JU-02 compressor diffusor pattern and tonight I made the sand pattern.
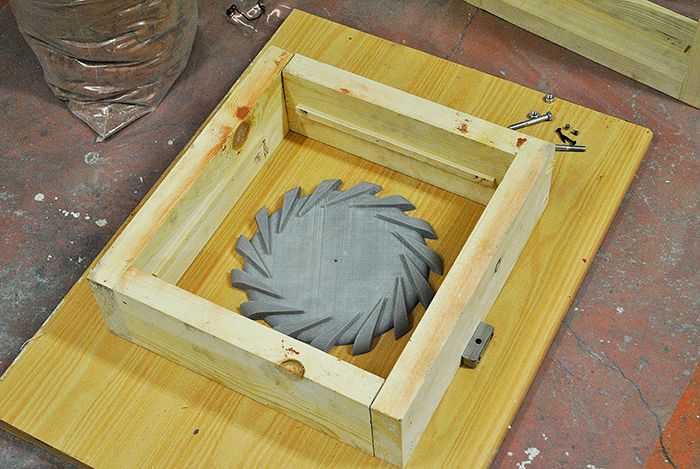
I sifted the sand closest to the pattern to get a smooth surface finish for the casting.

I used copper tubing to form the downpour and the vents, the downpour fits to the thickest part of the pattern that solidifies last.
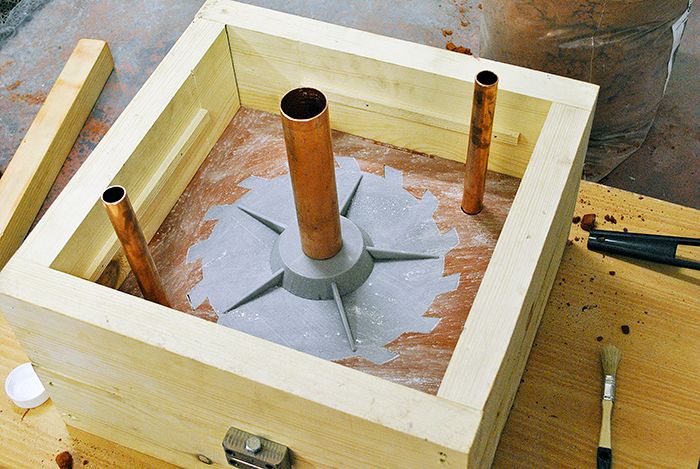
Baby powder is brushed on the surface so the sand won´t stick together when I ram the sand in the second flask.
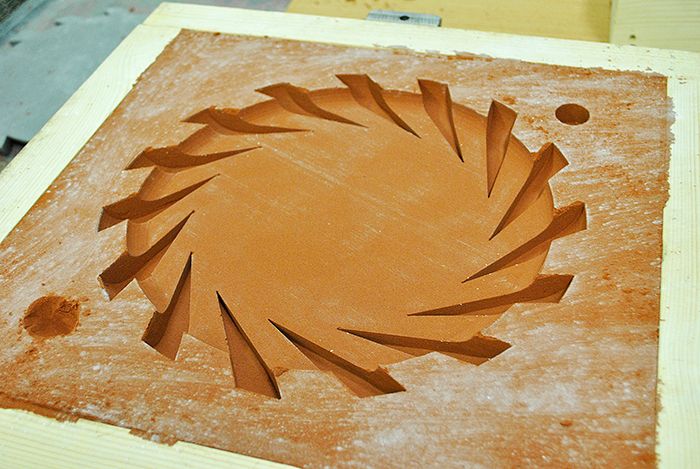
Looking really good! A couple of minor cracks on the diffusor wedges but that can easily be fixed on the cast part. Time to pull the second pattern from the sand.
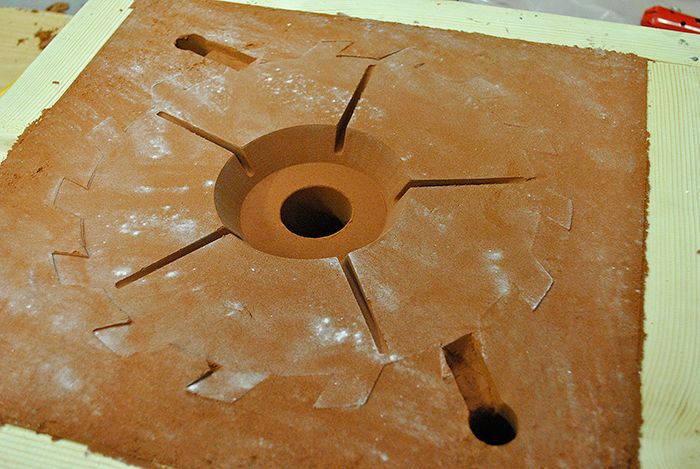
I am very pleased with how easy the 3D printed PLA patterns release the sand, I haven´t even bothered to smooth out the raw printed surface with sand paper.

The plan is to cast the part on Friday, keep your fingers crossed!

Cheers!
/Anders
-------------------
This morning I got up early to start the electric kiln, then I drank three cups of coffee and are a bunch of sausage sandwiches while it was heating up. With the crucible at 700°C I started loading it with aluminum and an hour later it looked like this:

I added flux to the melt to make it pour better and degassed it with gasseous nitrogen to pull oxygen from the melted aluminum, then I removed the dross and let the crucible heat up to 780°C before I poured it.

Exciting to say the least! I have had my share of more or less faulty casting attempts so it would be nice I could see some progress.

The result was very good, I cut the sprues off and heat treated the part in 180°C for 6 hours so it will be easier to machine later.
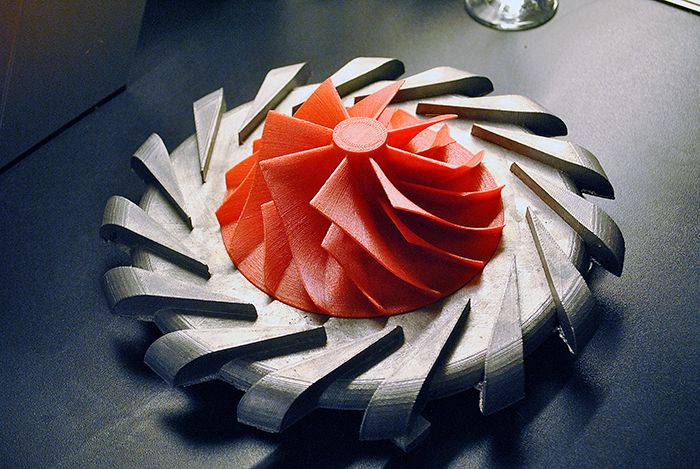
The only flaw is a small bubble on the mating surface to the bearing tunnel, but I can easily weld it up with the TIG welder so no big deal.

The 0.2mm layers from the 3D printing is clearly visible, very good details with the petrobond sand in other words.

I celebrated the success with a 31km running trip to a nearby hydro power plant and back and spent the rest of the day with my family, a Friday cannot possibly be much better than this one.


Here is the video from the casting:
Cheers!
/Anders
-------------
Why does this feel familiar? Luckily I won´t have to mill the diffusor from solid this time like I did with the last engine.

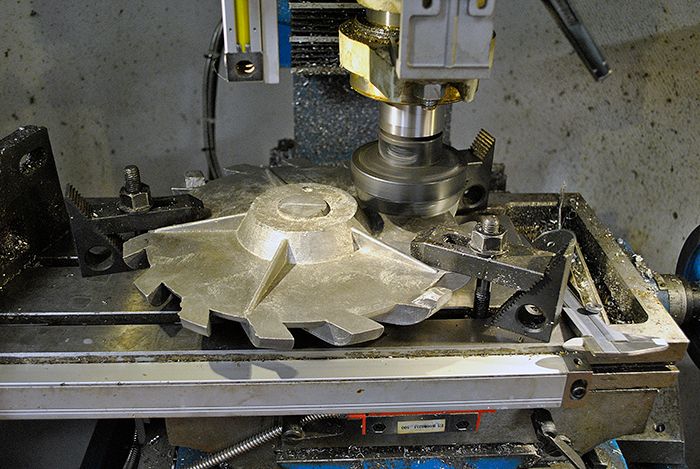
The diffuser was warped a bit bit it straightened out after I cut the support wedges that must have bent the plate during casting somehow.
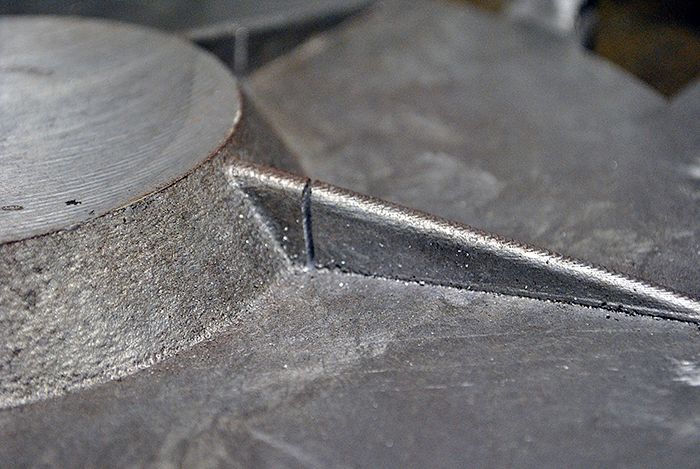
Drilling the centrum hole and the bolt circle, a digital readout for the mill is a very useful tool for things like this.
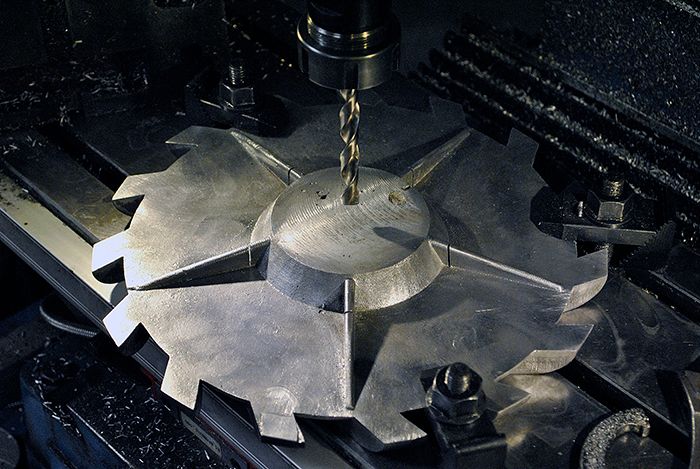
I´ll use four M10 insex 12.9 bolts to hold the engine core together.

Here I have just finished countersinking the holes for the insex bolt heads.

I had to make a jig to fit the diffuser plate to for the next job.
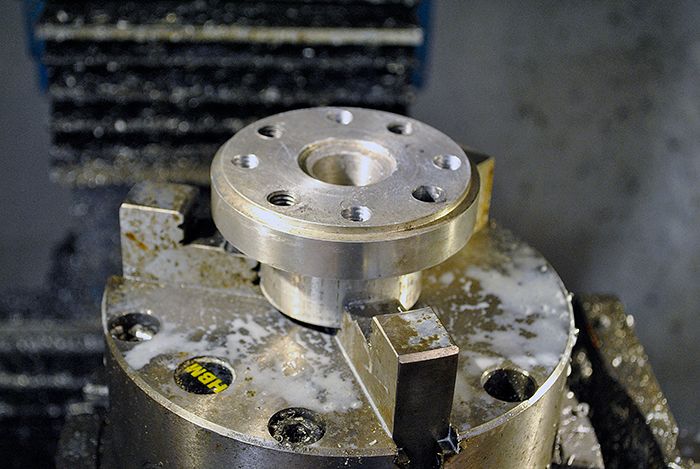
It was past midnight when I had finished the jig so I called it a night after realizing that my lathe was too small for this job.

Today I used some spare time at work to machine the compressor wheel recess, my job is as a mechanic at a local heating plant so I have a workshop set up there as well with a slightly larger lathe.

After some turning the recess was made with a bit of extra clearance for heat expansion and bearing play.

The compressor wheel looks like it was made for this.


I can´t exactly complain about the casting quality.

Cheers!
/Anders