|
Post by Johansson on Dec 26, 2015 16:11:19 GMT -5
Thanks guys! My friend Linus managed to use the 3D scanned image of the compressor wheel and turn it into a 360° blade profile, it took some effort even for him so I can say without a doubt that I couldn´t have done it in three life times... I got the profile by email last night so I made a solid part out of it in Inventor and printed it in PLA plastic today, the profile fits the compressor wheel great so I am very satisfied. 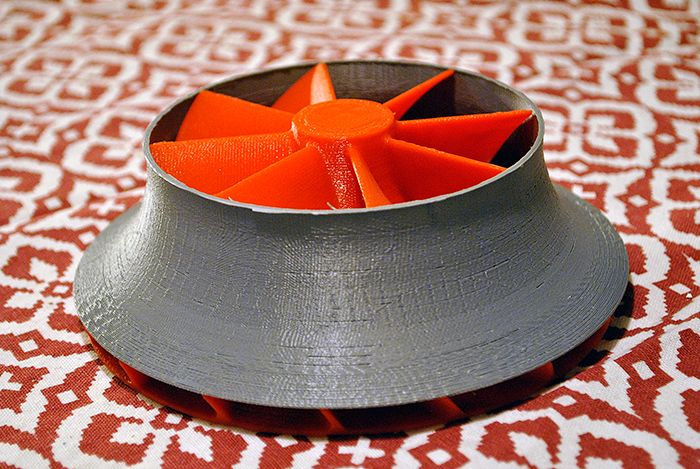 Cheers! /Anders
|
|
|
Post by racket on Dec 26, 2015 18:31:50 GMT -5
Hi Anders
LOL, if only you could print the entire from cover.
Cheers John
|
|
|
Post by Johansson on Dec 27, 2015 10:31:01 GMT -5
Actually I will in a way, I´ll print a pattern for the cover and sand cast it. I´ve been having some trouble with the print quality for a while but today I figured out that it was moisture in the PLA filament that made steam blow from the nozzle and make holes in the print, I need to keep the filament dry stored when not in use so it won´t pull moisture from the air. One fine day I can say for sure that I know the essentials about 3D printing, but I don´t know how many years from now it will be... 
|
|
|
Post by racket on Dec 27, 2015 17:57:13 GMT -5
Hi Anders
Have you been able to measure the comp profile to see if its a constant radius for machining the shroud ??
Probably need to allow ~0.35 mm radial clearance on the inducer and roughly the same axially on the exducer between blade and shroud.
Interesting that the PLA absorbs moisture .
Cheers John
|
|
|
Post by Johansson on Dec 28, 2015 0:04:47 GMT -5
Nope, no measurements yet but I can see if I can measure it in Inventor.
I did some more testing with the printer last night and it might not be steam after all, what looks and sounds like it might actually be air sucked into the nozzle when the filament is retracted (it backs in the thread a short bit when moving the print head to avoid stringing and dripping). I fiddled with the retraction settings a bit and the problems is almost gone now.
Keeping the PLA in dry storage is still a good idea though.
|
|
|
Post by Johansson on Dec 28, 2015 15:11:02 GMT -5
Today my friend Lars-E dropped by with the laser cut stainless parts for the NGV, I wisely decided I´d rather pay for having it done on the laser CNC than cutting them out of thick stainless sheet with the angle grinder.  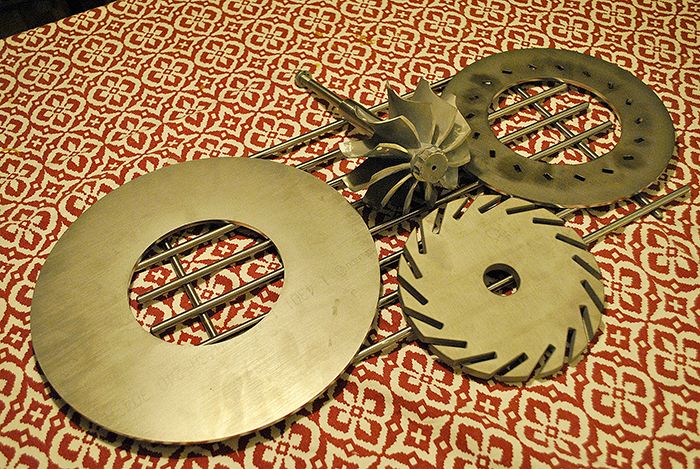 They came to use instantly, not as an NGV but as something to put the coffee pot on.  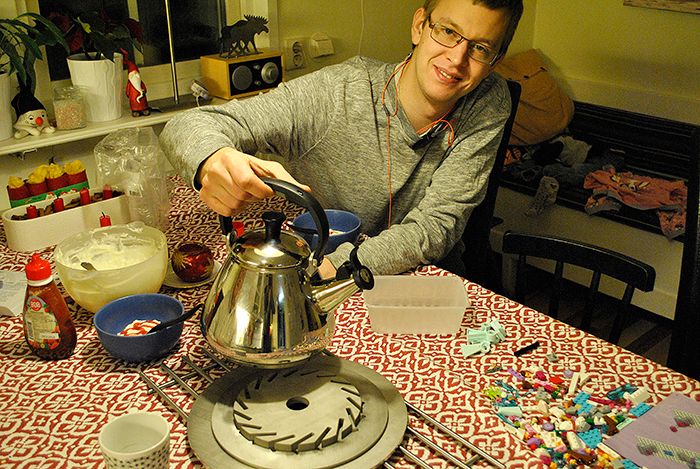 Cheers! /Anders
|
|
|
Post by racket on Dec 28, 2015 16:15:34 GMT -5
Hi Anders
Thats saved a lot of work
Cheers John
|
|
Chuks
Senior Member
 
Joined: August 2015
Posts: 498
|
Post by Chuks on Dec 29, 2015 11:04:58 GMT -5
hi Johansson.. about the compressor blade you are using for your new engine, it looked really different from the previous one. I will love to ask for the detailed information and how to get them incase I will need it..
|
|
|
Post by Johansson on Dec 29, 2015 14:03:07 GMT -5
Hi Anders Thats saved a lot of work Cheers John Heaps!  hi Johansson.. about the compressor blade you are using for your new engine, it looked really different from the previous one. I will love to ask for the detailed information and how to get them incase I will need it.. It is a KTS X846 compressor, an off the shelf part. ktsturbobilletx.com/
|
|
Chuks
Senior Member
 
Joined: August 2015
Posts: 498
|
Post by Chuks on Dec 29, 2015 14:42:11 GMT -5
thanks boss
|
|
Chuks
Senior Member
 
Joined: August 2015
Posts: 498
|
Post by Chuks on Dec 29, 2015 14:43:45 GMT -5
any tips about turbine site?
|
|
|
Post by racket on Dec 29, 2015 15:58:37 GMT -5
|
|
|
Post by Johansson on Dec 30, 2015 16:55:22 GMT -5
Today I cut the 18 nozzle guide vanes from 5mm thick SS2368, after some fine grinding in the laser cut grooves they fit lite a charm. 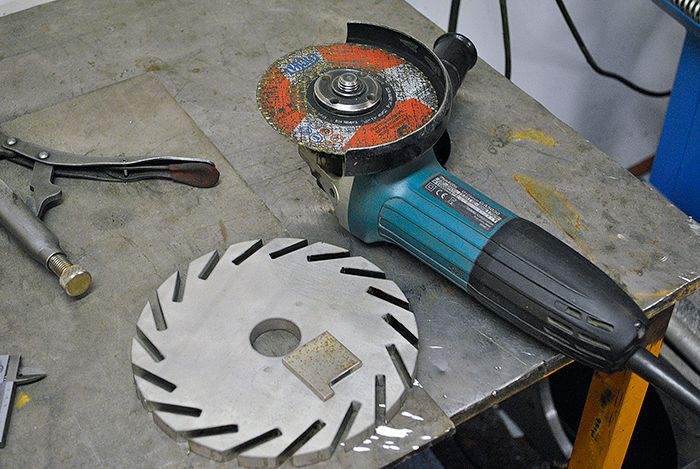 There is lots of work left before I can weld the NGV together, the bolt circle has to be drilled, shaft hole opened up, the vanes must be correctly profiled for good flow and the proper throat area etc. 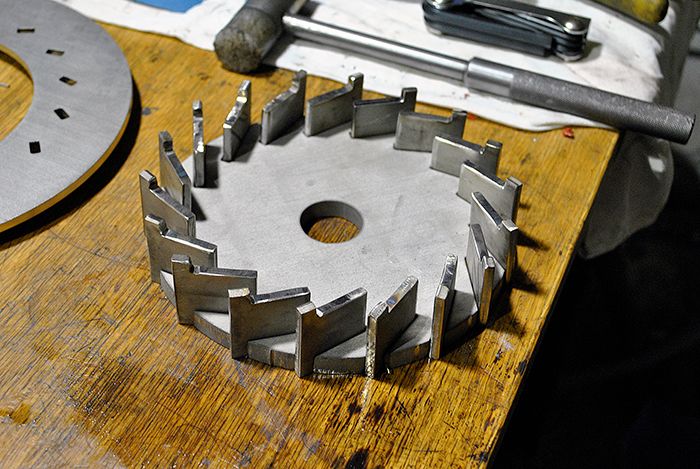 I will build the engine from the front and backwards so these parts will have to wait for their turn, still good to have come this far on the NGV. 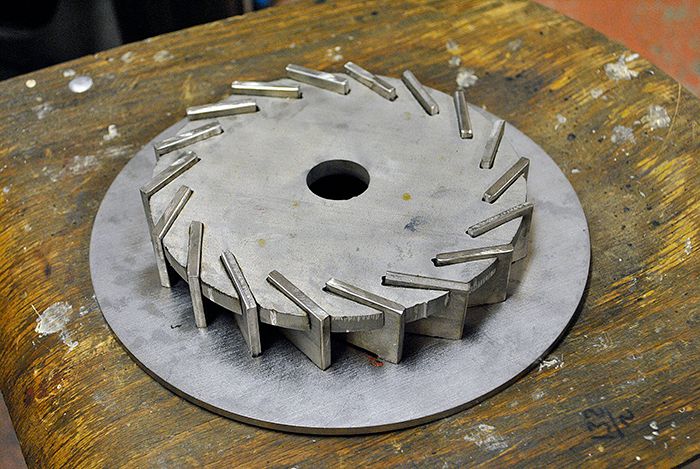 Cheers! /Anders
|
|
|
Post by racket on Dec 30, 2015 19:22:45 GMT -5
Hi Anders
Yep , the NGV assembly is one of the biggest jobs to do , but you're a long way into it :-)
Cheers John
|
|
|
Post by Johansson on Jan 2, 2016 3:55:39 GMT -5
Hi John,
My first idea was to have the whole NGV cast in stainless, but the cost and amount of pattern work needed compared to the "usual" sheet metal sandwich construction just wasn´t worth it.
I´ll do some thinking about the diffusor cover and try to get a pattern printed soon, while waiting for my fathers lathe to arrive I can at least get all of the castings done.
Cheers! /Anders
|
|