|
Post by stoffe64 on Jan 6, 2017 17:37:18 GMT -5
How much was it for that one?,you remember that patty?
|
|
miuge
Veteran Member
 
Joined: March 2014
Posts: 200
|
Post by miuge on Jan 7, 2017 6:55:07 GMT -5
Hi Stephan,
Get a new HX80 or HC5A with a single scroll housing from alibaba, they're around $500 incl. shipping.
|
|
|
Post by madpatty on Jan 7, 2017 12:26:23 GMT -5
How much was it for that one?,you remember that patty? Hi. The price was same as advertised now. I got it for 300$ including shipping. Cheers.
|
|
|
Post by stoffe64 on Jan 7, 2017 15:07:24 GMT -5
Thanks for the information guys!
|
|
miuge
Veteran Member
 
Joined: March 2014
Posts: 200
|
Post by miuge on Jan 16, 2017 10:05:17 GMT -5
Hi all, I ordered a diaphragm pump and some oil burner style nozzles for experimental tests. I want to know if I could use those oil burner style nozzles (without an excessive pressure) in an annular combustor instead of syringe needles. The pump is rated 10bar max and nozzles are ~400 and ~600cc/min @5bar, pictures indicate a very fine mist. Anyway if it's not a functional idea, I can use it as water injection system in my car project 
|
|
miuge
Veteran Member
 
Joined: March 2014
Posts: 200
|
Post by miuge on Feb 14, 2017 15:14:33 GMT -5
Quick test of the pump and nozzle, didn't have a gauge or properly sealed bits yet, but that doesn't look so bad?
|
|
|
Post by Johansson on Feb 14, 2017 15:17:45 GMT -5
I think you will be better off with a set of "Racketjectors" (syringe needles with the pointy tip bent) since the spray nozzles will only give a good pattern at high pressure, at idle they will just dribble fuel into the syringes and cause very poor atomization.
Also, the spray nozzles need to be positioned very close to the evaporator inlets to get all of the fuel spray in to the evaporator, if not it will spill all over the engine internals.
|
|
miuge
Veteran Member
 
Joined: March 2014
Posts: 200
|
Post by miuge on Feb 14, 2017 16:27:44 GMT -5
That's true, precise positioning would be needed with nozzles like this and probably the evaporator inlet should be shaped differently too. I'll gather some data with different pressures and try to take some photos of the pattern with lower pressures. This combo will most likely go to my car project (as water injection system), I machined that nozzle holder and sleeve to fit on the bottom of the intake manifold. It's good to practise some welding before starting the ultimate turbine project 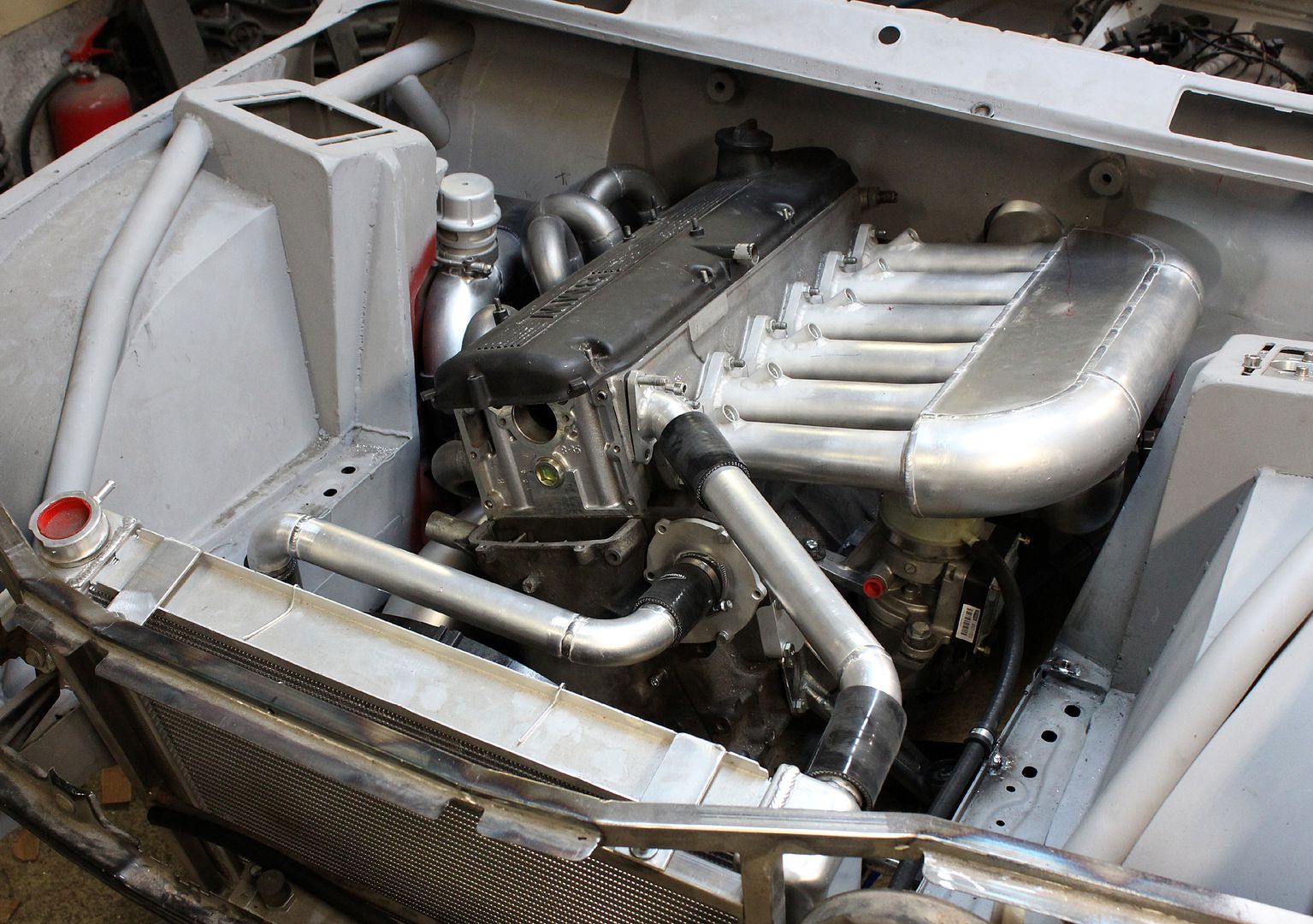
|
|
|
Post by Johansson on Feb 14, 2017 16:34:14 GMT -5
Nice car build, any reason why you will run water injection in a turbocharged BWM engine instead of a regular intercooler?
|
|
miuge
Veteran Member
 
Joined: March 2014
Posts: 200
|
Post by miuge on Feb 14, 2017 16:57:53 GMT -5
|
|
|
Post by Johansson on Feb 15, 2017 4:00:45 GMT -5
Sweet build! I see you use a water/air intercooler, they are really compact compared to the huge air/air IC´s needed for these kind of HP. Do you have a build thread for the car somewhere?
|
|
|
Post by finiteparts on Feb 15, 2017 22:24:55 GMT -5
Hi, Using simplex pressure atomizers (oil burner nozzles) for your annular chamber is a very valid approach to building a combustor. If you are suggesting that you are going to use them with a vaporizer style combustor, I would agree that a capillary tube is a better approach (either with or without the bent end). But, if you step back and look at the fundamentals, you will see that combining a simplex atomizer with a vaporizer is really unnecessary. The fundamental reason for using an atomizer is to increase the surface area between the liquid and heated air, thus increasing the evaporation rate of the fuel. Using a vaporizer, you are trying to increase the heat transfer into the larger liquid stream. But if you have the hot gas "touching" the small liquid droplets, that is better than having the hot gas transfer heat to the vaporizer tube, conduct that heat through the tube wall and them transfer that heat into the flowing liquid. So, if it was me and I was wanting to use pressure atomizers, I would build a primary zone swirler with the atomizer discharging into the recirculation zone created by the swirler. This creates a very stable primary combustor zone and is the reason that the majority of the gas turbine combustors out there use pressure atomizers over vaporizers. The challenge that you will have is sizing the injectors for the full flow range of the engine. You will need to keep the atomizer pressure drop above 40 psi or so to get sufficient atomization. The challenge with simplex pressure atomizers is that they have a very poor "turndown ratio", which is the ratio of the max flow to the min flow. Delavan has a nice document discussing the design and selection of their oil burner nozzles www.delavaninc.com/pdf/Fuel_Nozzles_for_Burners.PDFbut you should also look at the spill back style fuel nozzles. They can achieve much larger turndown ratios by using a larger flow rate to get the angular momentum necessary in the spin chamber of the nozzle, but then spilling some of that flow back to the tank so that you can have a much lower flow that would not have had enough angular momentum to effectively atomize if it was the only flow put into the spin chamber. www.delavaninc.com/pdf/variflo_catalog.pdfI used a Delavan variflo nozzle for my undergrad, senior design project combustor with excellent results. If you want to build a swirler based design and need help, get me your target flows and I will try to help you come up with a design. Good luck! Chris
|
|
|
Post by racket on Feb 15, 2017 23:12:34 GMT -5
Hi Chris Totally agree , no point going to the "trouble" of spray nozzles if spraying into a "metal tube heat exchanger" . Miuge An annular flametube would need a fair number of spray nozzle to provide effective coverage of the cross section , this then means reduced flow rates and this in turn creates problems finding very small flow nozzles that will provide good atomisation, its the reason why I've never gone to them , though the syringe needles with bent tip do produce a relatively fine mist spray at modest pressure drops postimg.cc/image/miwsy23gl/ , and in my humble opinion could be used in place of a spray nozzles. A single Variflo nozzle, installed as Chris recommended, in a "sore thumb" combustor mounted to your turbine scroll is probably the simplest and best method when constructing a turbo based engine , I've built DIY turbo based type engines using both spray nozzles as well as evaporators, I'm convinced the spray nozzle is the way to go when everything is taken into account , there might be a tad more work with providing/running higher fuel pressures , but that is more than offset by the simplicity and reliability/security compared to evaps which can and do burnout and/or break loose . My TV84 turbo based engine used a Simplex spray nozzle ( Variflo not available back then) spraying through a swirl vane set from an oilburning steam boiler combustion system , fuel pressures ranged from ~50 psi at idle to ~750 psi at full power , some problems getting the throttling mechanism right but the combustion worked perfectly from day one with very good throttle responses , it revved up an down like an IC engine . Cheers John
|
|
miuge
Veteran Member
 
Joined: March 2014
Posts: 200
|
Post by miuge on Feb 16, 2017 10:41:22 GMT -5
Johansson, you'll find my forever lasting build thread here: www.garaget.org/forum/viewtopic.php?id=269850Chris and John, fair enough, I do not want to make things too complicated  I feel "pressure atomizer fuel injection" would require too expensive bits, pressure would be the main concern. I've been looking for small hydraulic pumps, but they require lot's of power and I'm not sure do they even work with diesel fuel viscosity. We have single nozzle injection in our turboshaft bike with EFI pump (max. 9bar), it probably had poor atomization related problems at lower pressures but works great after we raised idle speed. I'm still thinking I'll make this new one a reverse annular combustor style, easy to route oil in and out, longer combustor and whatever I decide with the fuel system, it'll be external easy to maintenance too. Mist of the "Racketjectors" looks pretty fine indeed, I'm confident it'll help to fix earlier fueling problems of the "FAT BOY"
|
|
|
Post by madpatty on Feb 16, 2017 12:20:51 GMT -5
Hi, Using simplex pressure atomizers (oil burner nozzles) for your annular chamber is a very valid approach to building a combustor. If you are suggesting that you are going to use them with a vaporizer style combustor, I would agree that a capillary tube is a better approach (either with or without the bent end). But, if you step back and look at the fundamentals, you will see that combining a simplex atomizer with a vaporizer is really unnecessary. The fundamental reason for using an atomizer is to increase the surface area between the liquid and heated air, thus increasing the evaporation rate of the fuel. Using a vaporizer, you are trying to increase the heat transfer into the larger liquid stream. But if you have the hot gas "touching" the small liquid droplets, that is better than having the hot gas transfer heat to the vaporizer tube, conduct that heat through the tube wall and them transfer that heat into the flowing liquid. So, if it was me and I was wanting to use pressure atomizers, I would build a primary zone swirler with the atomizer discharging into the recirculation zone created by the swirler. This creates a very stable primary combustor zone and is the reason that the majority of the gas turbine combustors out there use pressure atomizers over vaporizers. The challenge that you will have is sizing the injectors for the full flow range of the engine. You will need to keep the atomizer pressure drop above 40 psi or so to get sufficient atomization. The challenge with simplex pressure atomizers is that they have a very poor "turndown ratio", which is the ratio of the max flow to the min flow. Delavan has a nice document discussing the design and selection of their oil burner nozzles www.delavaninc.com/pdf/Fuel_Nozzles_for_Burners.PDFbut you should also look at the spill back style fuel nozzles. They can achieve much larger turndown ratios by using a larger flow rate to get the angular momentum necessary in the spin chamber of the nozzle, but then spilling some of that flow back to the tank so that you can have a much lower flow that would not have had enough angular momentum to effectively atomize if it was the only flow put into the spin chamber. www.delavaninc.com/pdf/variflo_catalog.pdfI used a Delavan variflo nozzle for my undergrad, senior design project combustor with excellent results. If you want to build a swirler based design and need help, get me your target flows and I will try to help you come up with a design. Good luck! Chris Hi Chris, Can you share some more knowledge on swirler based fuel injection and its design. I want to learn more about it so a document or two on this topic will help. Thanks. Patty
|
|