Feathers
Veteran Member
 
Joined: August 2010
Posts: 169
|
Post by Feathers on Mar 25, 2017 17:30:52 GMT -5
I haven't included a good, well-lit video of the starting and running of the engine so far, here's a post with one! We've also been troubleshooting a little issue with our oil tank. There's so much oil mist and vapor in the CHRA discharge to the tank, that there is a significant quantity leaving the vent and making a mess. We bought one of these, but it just filled up after 10 minutes of run time: 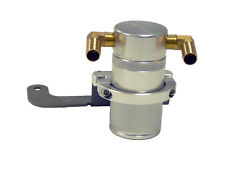 We put some tank foam in the oil tank, beneath the vent outlet, and it fixed the problem. Barely a dribble now. Cheers, - Feathers
|
|
Feathers
Veteran Member
 
Joined: August 2010
Posts: 169
|
Post by Feathers on Apr 3, 2017 0:59:44 GMT -5
Last night our team finished the mounting the power turbine. We're using the rail-clamp method of producing pillars that hold a plate to which we can mount the turbine. A 1"-thick aluminum pillar in the front and back clamp to the frame and support a 3/4"-thick aluminum plate on top. Another plate is required to slide under the bearing tunnel such that it can be retained securely. 16 large stainless fasteners, in all, hold the whole thing together: 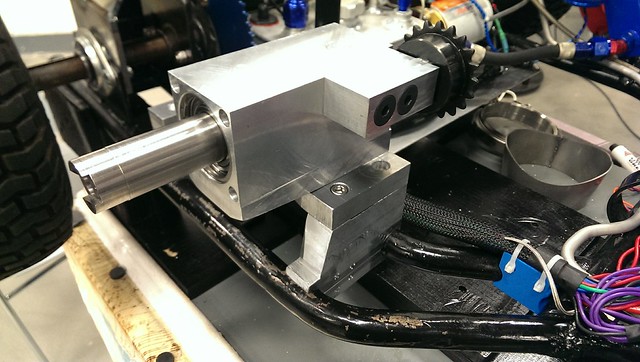 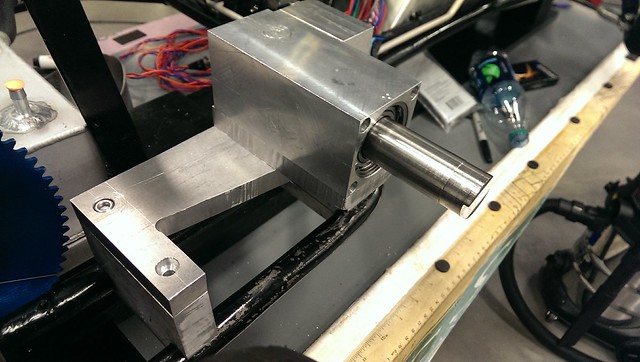 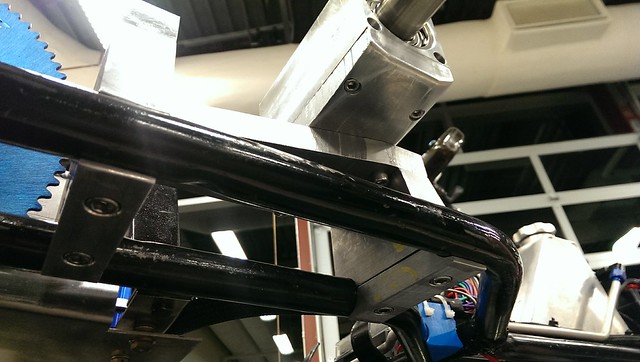 We're just happy that everything ended up fitting! Here we install the shroud and plenum to the front of the bearing tunnel:  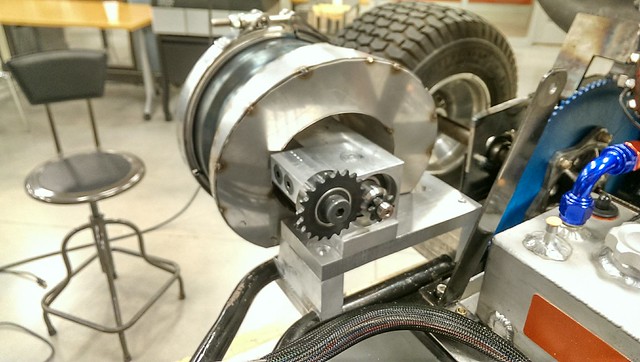 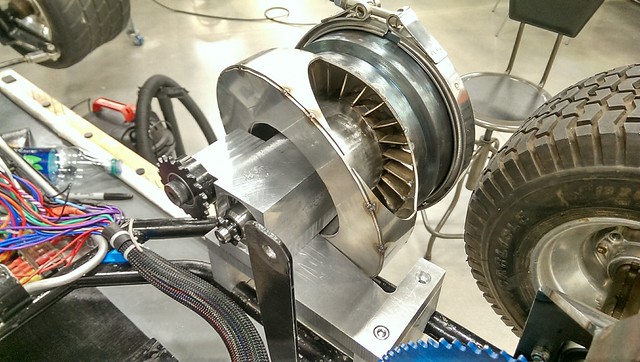 We test-fitted the chain and spun the turbine with a leaf blower. Even with ~1/2 horsepower of gas energy, there was significant torque to the rear wheels. Enough to move the kart! We've also got lots of smaller bits finished that I need to show you, but we've been moving so quickly that I've forgotten to take pictures. Cheers! - Feathers
|
|
|
Post by racket on Apr 3, 2017 1:25:48 GMT -5
Hi Feathers
Nice :-)
Things are certainly moving fast , a bit of interstage ducting and you'll be itching to fire her up and start turning those wheels in anger .
Cheers John
|
|
|
Post by Johansson on Apr 3, 2017 5:12:37 GMT -5
Awesome build quality Feathers!
|
|
Feathers
Veteran Member
 
Joined: August 2010
Posts: 169
|
Post by Feathers on Apr 9, 2017 16:39:38 GMT -5
Thanks guys. We ordered a corrugated stainless bellows expansion joint for the interstage duct. That's on it's way along with some 5" stainless tube to hack up. We're very close to as John put it, spinning some wheels in anger We have the interstage adapter tack welded onto the power turbine plenum now, along with the v-band flange that goes with it. For final welding, we'll need to purge the assembly to keep sugaring to a minimum: 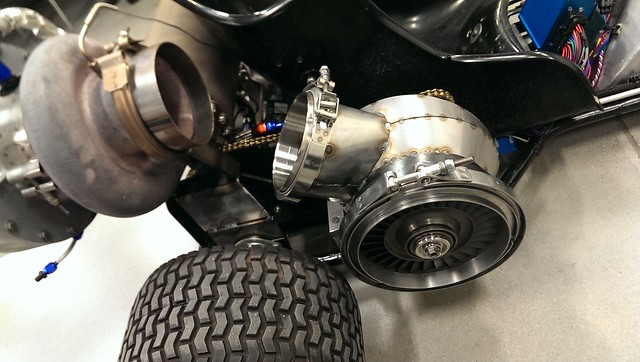 Some of the bits we've been adding and working on in the meantime: We wanted all of the external stuff to plug into the same spot on the back of the kart. Some of our newer members have been 3D modeling and printing or fabricating mounts for everything. We bought a sealed male US-120 volt socket to receive an extension cord for the tank heaters, and to the left is the starting fuel quick-disconnect. The 3D printed part also accommodates another female quick-disconnect fitting. This one will stay with the kart, and will plug the start fuel connection to prevent dirt and grit from contaminating the solenoid seals. 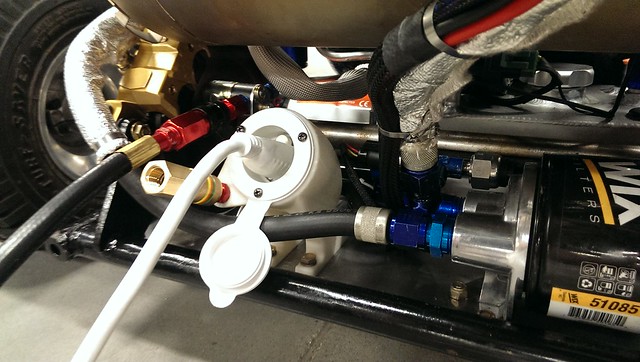 Then when we want to run the kart, we just use the fitting to "plug" the connection and off you go. 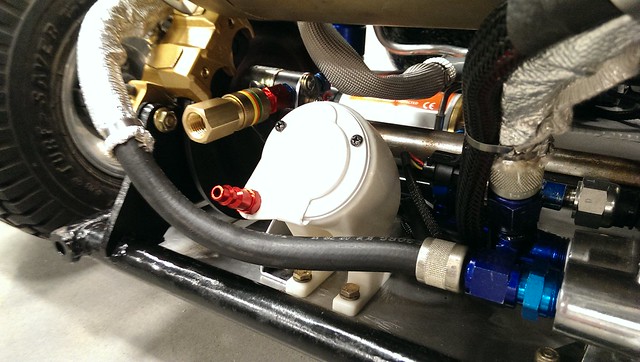 We installed an oil-air separator to our oil tank vent line before piping it into the low-pressure exhaust. This should keep things nice and clean. It doesn't collect much anyway. Mounting this stuff is getting more and more tricky... 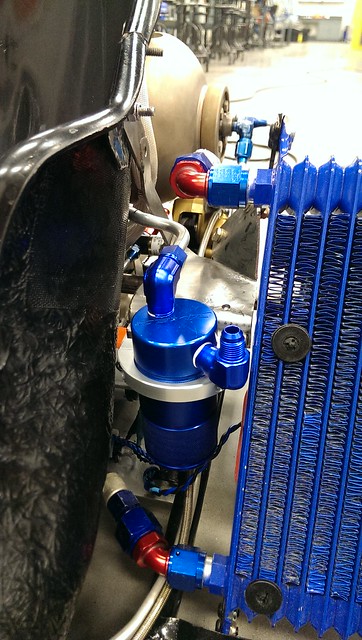 The group's president Madeline is currently working on FEA analysis of the power turbine in her classes, to determine a theoretical maximum operating and burst speed for the power turbine. Its really cool, and I don't understand any of it... By the way, how fast do these wheels spin in the C-20 engine? Does anyone know off the top of their head? 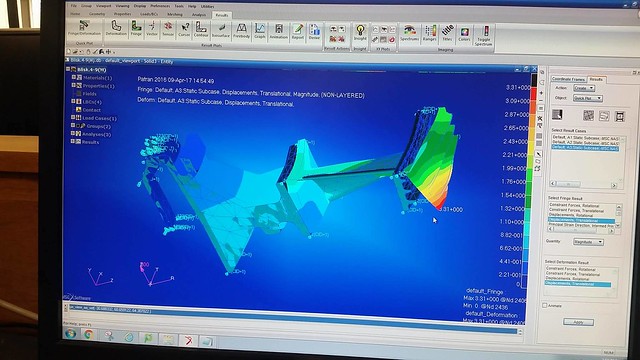 We've also been working on the brakes, which are almost functional. Its coming together quickly. Struggling to cover all our bases on safety and reliability before we present ourselves with the option to drive it, and the temptation to push our luck! 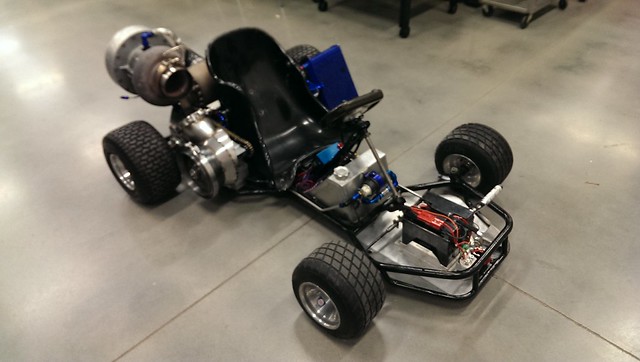 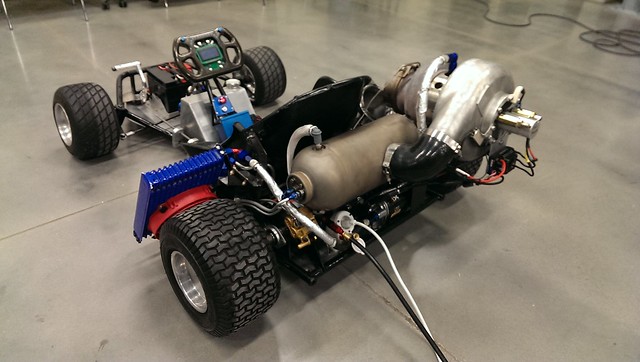 Cheers! - Feathers
|
|
|
Post by racket on Apr 9, 2017 17:13:18 GMT -5
Hi Feathers Thats becoming one fine looking kart :-) C20B N2rpm are 33,290 at 100% with interstage temps ( your freepower's T I T ) of 1460 F - 793 C for takeoff ( 5 minutes) or max continuous of 1430 F 777 C , they can be taken to 34,950 - 105% during ground idle at interstage temps ~800 F - 425 C ...........this vid might "calm" Madeline's concerns www.youtube.com/watch?v=CplnY9TG7NE or maybe not ;-) During a dyno test of my turbine bike equipped with a similar C20 3rd stage wheel , the guys operating the bikedyno ( I wasn't present) took it to an overspeed of ~130% N2, the dyno operator didn't understand that turbines don't reach a max rpm like an IC bike engine , so kept on increasing the "road speed" way past design limit. You may need a heat guard over the tire at your freepower exhaust , you'll be surprised just how much radiant heat comes off its ducting Cheers John
|
|
Feathers
Veteran Member
 
Joined: August 2010
Posts: 169
|
Post by Feathers on Apr 13, 2017 16:56:44 GMT -5
Yikes! Those are good numbers to keep in mind. Hopefully Madeline's studies will shed more light on the burst speed (and mode) of the turbine. We aren't looking to run it at over 20,000 RPM, and have some tricks in mind to keep a chain-off event from resulting in overspeed. We've been working on the air/oil bleed to the power turbine bearings. These will lubricate the bearings, cool the bearings, and provide positive pressure to displace exhaust gas from the hot-side bearing. We're also looking to scavenge some of the oil via compressor bleed pressure back into the oil tank, so galleys will be drilled in the bearing tunnel to facilitate draining. Of course we'll loose some oil via the shield on the hot-side bearing, but hopefully not as much as if we didn't scavenge. Scavenging oil will also allow us to flow more oil, and better accommodate bearings being pushed faster than they would otherwise run safely. We're using a Parker N200S hydraulic needle valve to provide fine control over the rate of oil flow. 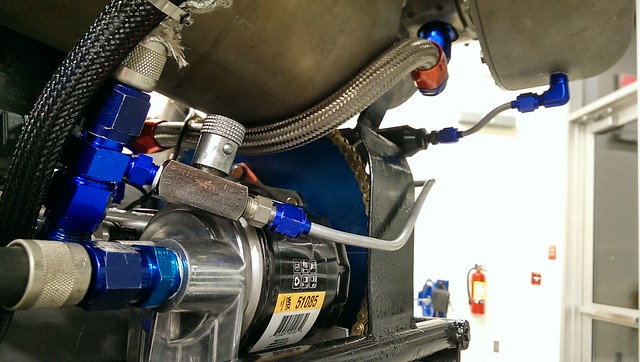 With the valve dialed in at 5-6 drips/sec at an oil temperature of 180*F, we proceeded to fit the compressor bleed. The compressor bleed consists of a 0.072" restriction orifice, and a check-valve to prevent oil from entering the compressor when the engine isn't running. 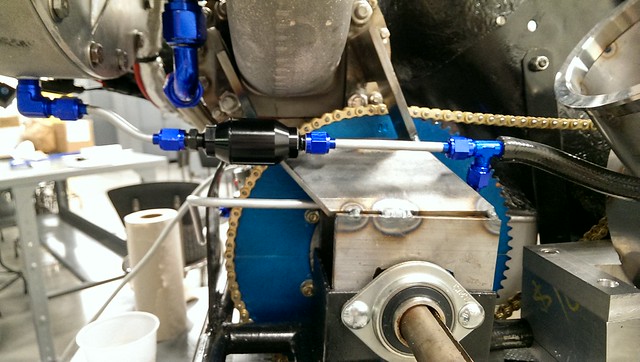 The air and oil bleeds are combined into one line which will service the lubrication galleys of the bearing tunnel. 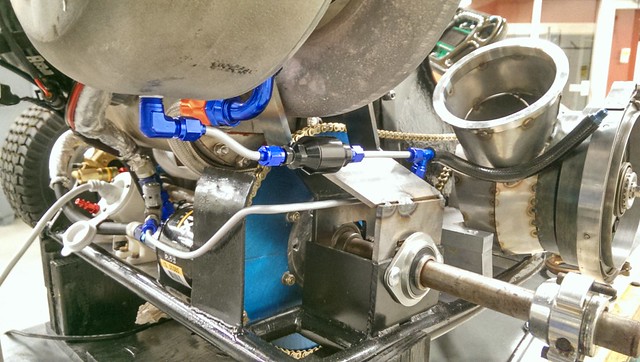 We ran a test of the lubrication system, to get some idea how much liquid and gas was moving, as well as if there would be a fine mist, or ineffective sputtering and blockage through the thin tubing. The test revealed a very fine mist of oil leaving the system at full throttle. Very happy campers The team has also been busy getting the brakes sorted. We're using a motorcycle master cylinder/reservoir, and the plunger is "unconstrained" in it's motion. We fabricated aluminum blocks which clamp to the frame, and hold bronze bushings for a steel rod which will be actuated by the brake pedal. 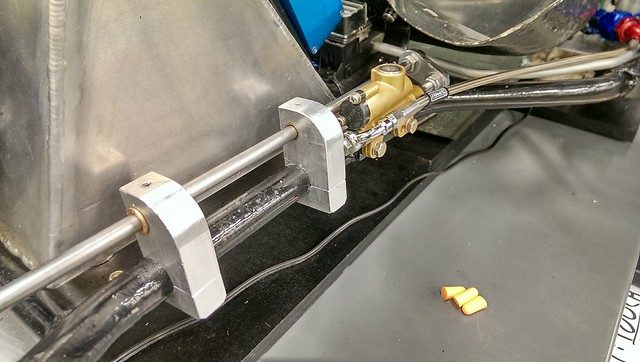  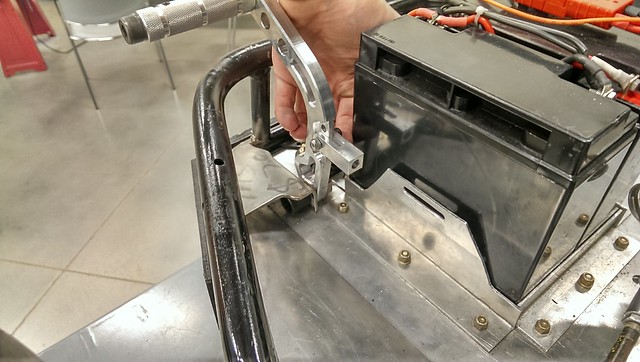 Cheers! - Feathers
|
|
|
Post by racket on Apr 13, 2017 18:14:15 GMT -5
Hi Feathers
A nice air/oil mist , that'll keep the bearings happy :-)
Cheers John
|
|
Feathers
Veteran Member
 
Joined: August 2010
Posts: 169
|
Post by Feathers on May 18, 2018 13:17:33 GMT -5
Wow! There's a lot to update. I'd better get started, this will take a couple posts... So the team has had the power turbine assembly welded, as well as the interstage duct with it's bellows. 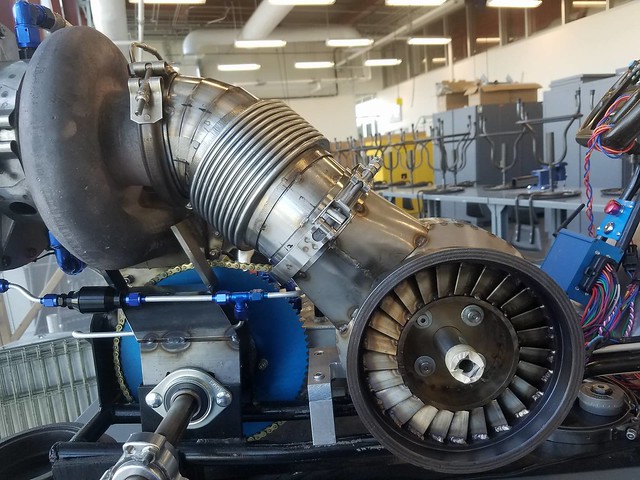 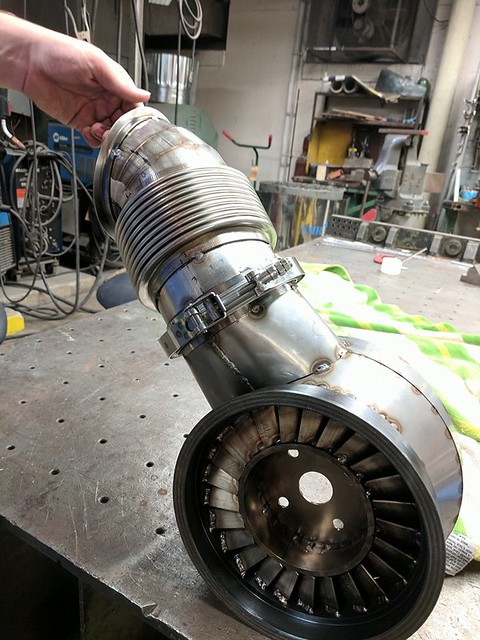 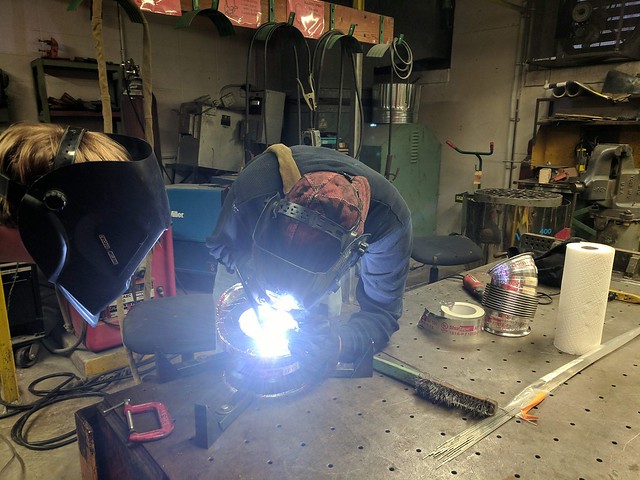 The team bored the hole for the turbine shaft as close as possible to prevent air and oil from leaking out into the exhaust stream: 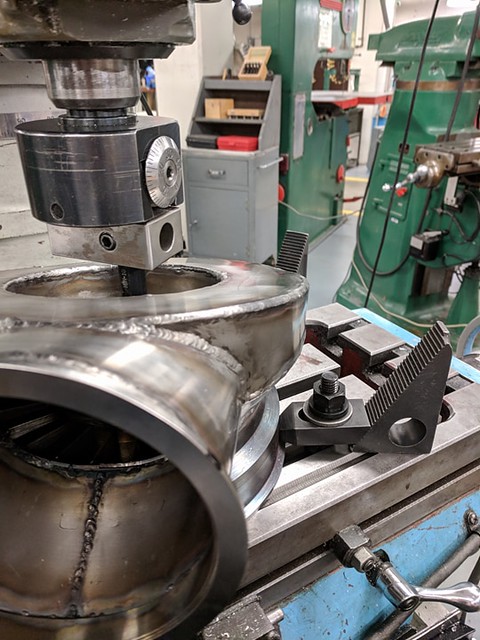 For a nice close fit  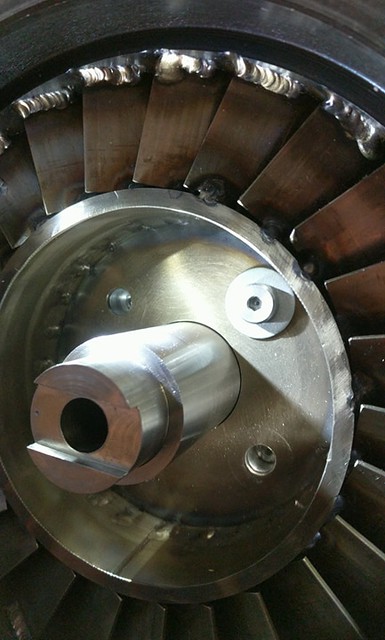 More on the way as I download and organize some photos. Cheers, - Feathers
|
|
|
Post by racket on May 18, 2018 16:46:08 GMT -5
Hi Feathers
Some very nice work :-)
Cheers John
|
|
|
Post by Johansson on May 18, 2018 17:21:51 GMT -5
Wow Feathers, you have certainly kept yourself busy! Keep the pics coming! 
|
|
Feathers
Veteran Member
 
Joined: August 2010
Posts: 169
|
Post by Feathers on May 18, 2018 19:35:42 GMT -5
Wow Feathers, you have certainly kept yourself busy! Keep the pics coming!  Thanks! Unfortunately, I can't take any credit for the progress. I've been in Denver, Colorado this whole time! I must have passed the "turbine itch" on to the rest of the team, because they've been working hard on it ever since I graduated from the University of Kansas. Cheers, - Feathers
|
|
Deleted
Joined: January 1970
Posts: 0
|
Post by Deleted on May 19, 2018 2:42:50 GMT -5
Wow Feathers, you have certainly kept yourself busy! Keep the pics coming!  Thanks! Unfortunately, I can't take any credit for the progress. I've been in Denver, Colorado this whole time! I must have passed the "turbine itch" on to the rest of the team, because they've been working hard on it ever since I graduated from the University of Kansas. Cheers, - Feathers Well they doing a real nice job, it is really coming together, looking forward to seeing it move..... you going to need a runway to have some real fun in it :-)
|
|
Feathers
Veteran Member
 
Joined: August 2010
Posts: 169
|
Post by Feathers on Apr 26, 2019 18:58:20 GMT -5
They've done really great work.
Most recently they've been buttoning things up. Items they've tackled:
Battery has been woefully inadequate for extended runs and starting current. They replaced the current pack with a very beefy 4S Lipo pack. 16V peak keeps the pumps and starter ESC very happy, the old lead acid gell cells were seriously underrated for the startup draw, and died a predictable death.
Given the highly automated and pixie-heavy nature of this project, good batteries are a must.
They're configuring a mechanical chain tension fuel cutout circuit, such that if our #35 chain breaks or slips off, our power turbine doesn't overspeed. I'm still unconvinced that it's possible to overspeed with the gas energy available to us, at least until we choke the NGVs for more power, but I'd rather not find out.
The 16V batteries make the fuel pump a bit more sporty. Since we originally restricted the fuel circuit to deliver max N1 at 100% fuel pump speed and with hot oil, we're installing a needle valve so we can rope fuel flow back in and eliminate the possibility of overspeed at this new drive voltage.
Other than that, it'll be rolling for the first time ever soon. I can't wait to share video.
Thanks and regards,
- Austin
|
|
|
Post by turboron on Apr 26, 2019 20:33:47 GMT -5
Austin, any updates to the FADEC software/hardware?
Thanks, Ron
|
|